3 minute read
Order growth sees Apex Group invest and create jobs
Durham-based Apex Group – which includes Apex Wiring Solutions, Artech Lighting, Apex Core and Evo IDC – has reported a surge in post-lockdown orders across all business divisions. As a result, the firm is investing over £400,000 in new machinery and creating around 30 new roles, as it continues to win work across the UK and overseas.
Over the coming months, Apex, which currently employs around 100 people at its Durham headquarters, will increase its production team to satisfy a string of new orders secured in recent weeks.
The investment comes just two years after Apex invested half a million pounds creating the UK’s first specialist prefabricated utility cupboard production line, forming Apex Core. The business has not only managed to secure a string of high-value contracts, but it says it is also changing the way the construction industry thinks about development, with Core units providing a central hub for a home’s utility services.
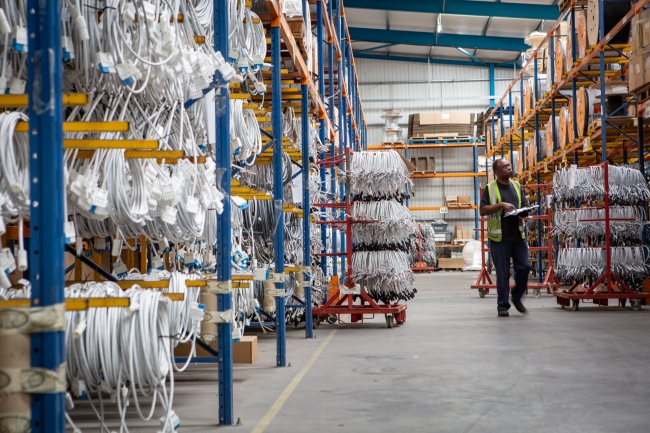
A surge in orders has seen Apex Group invest in its operations and create new jobs to keep up with demand / Picture: Apex Group
Dave Lewis, managing director at Apex, said: “The world has changed, the way we do business has changed and the way our customers operate continues to change, and what we have done is successfully adapt to this change.
“The Core units and Apex Wiring Solution’s modular wiring enables socially-distanced installation, Artech’s product performance and efficiencies continue to improve, as we all do our bit to address the global climate crisis and we are continually upgrading our IT systems to ensure all of our internal processes are streamlined and responsive.
“I also believe businesses must make an effort to ‘Buy British’, not only to aid the economic bounce back, but avoid additional issues around importing products from overseas, which include the obvious reduction in carbon emissions and the creation of manufacturing jobs in the UK. Looking ‘local’ has both economic and environmental benefits.”
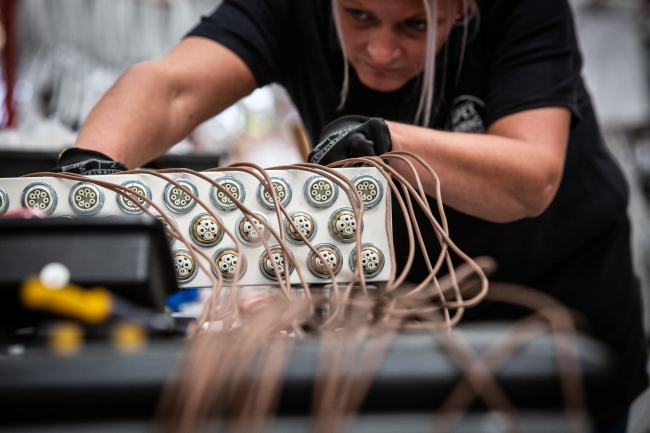
Apex Group is investing over £400,000 in new machinery and creating around 30 new roles / Picture: Apex Group
Artech Lighting is also making a significant investment, purchasing a second paint plant, press brake, profile roller and punch tool, as well as substantial upgrades to its IT network.
Stuart Hylton, managing director at Artech, added: “Work has steadily increased throughout the past two years, but we have seen a real upsurge in recent months across all three of our businesses. The new investment will help us ramp up manufacturing across the entire Artech range, ensuring we keep all production in-house and continue to create even more high-value jobs here in the North East.
“The Artech brand continues to be a major industry disruptor. We are willing to compete with the more recognised brands and offer equal or better quality, output, delivery and efficiency, but with significantly less cost with the added piece of mind that you are buying a UK manufactured product. It is a strategy that is working, as recognition of the Artech brand continues to grow.”