10 minute read • published in partnership with Make UK
Believe in manufacturing – the inside story of how Siemens is improving factory productivity
Saving the planet – one factory at a time
Brexit and the Covid-19 Pandemic, the switch to electrically-powered vehicles and the need to decarbonise are accelerating the drive to automation and the adoption of novel technologies.
Brian Holliday, Managing Director of Siemens Digital Industries and Chairman of Siemens Industry Software UK, has been an advocate for the adoption of industrial digital technologies in manufacturing for most of his working life, including 28 years with Siemens. He views it as an urgent matter for UK manufacturing.
“When it comes to automation and digital technology adoption, the UK lags most industrial economies. There are sector strengths such as automotive in Germany that part explain the difference, but there is an underlying problem of poor plant and equipment investment which is becoming more important now we understand how digitalisation enables decarbonisation and increasingly informs the optimum sustainability steps.”
Brian champions the cause in the media and trade events as well as industry and government forums, such as Make UK, the CBI Manufacturing Council, the High Value Manufacturing Catapult (HVMC) and the Made Smarter initiative.
The UK Government’s financial incentives to encourage more investment in raising productivity through automation have met with mixed success. Brian highlights a few signs over the past couple of years that signal hope for change – that digital technology can make a difference when it really matters. One is the Ventilator Challenge, brought together under the leadership of Dick Elsy, then CEO of HVMC.
“At the Broughton Airbus/AMRC site, we conducted a ‘hackathon’, involving a mix of early career professionals and more experienced contributors, to try and fix a tricky calibration challenge with the ventilator flow valve sub assembly. This led us to an advanced digital simulation,” he explained. “in which the team were able to rapidly design a precision, additively manufactured part enabling an in-line test process which brought the calibration time down from nearly 45 minutes to about two. Given the extreme pressure to build ventilators at pace, this was about saving lives.” The process had been designed around a takt time of seven minutes so that hack eliminated what had been a serious bottleneck.
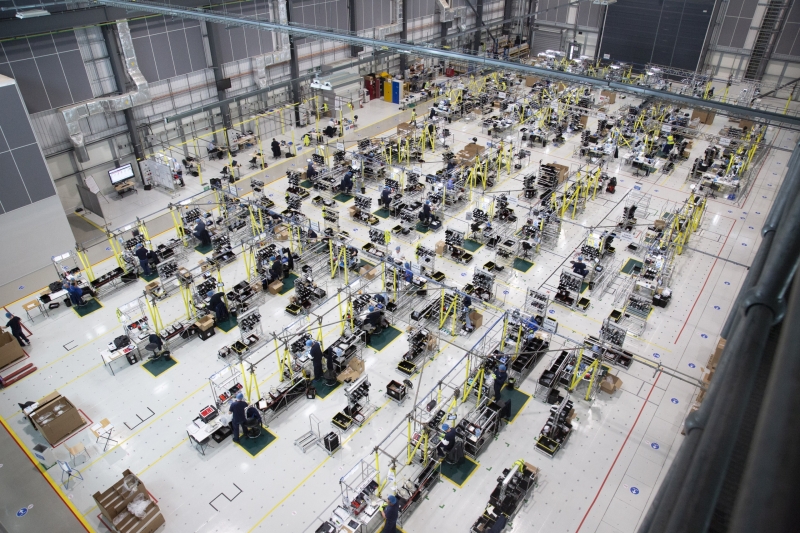
The Airbus/AMRC site at Broughton / Picture: Siemens
What the Ventilator Challenge did – apart from delivering over 14,000 desperately-needed medical devices in record time to the NHS – was to demonstrate how agile, resourceful and effective UK manufacturing companies can be when the chips are down – and how they can collaborate, in the right circumstances.
The challenge now is to make that kind of achievement routine.
At a time when industry is facing extreme challenges in complexity, cost and resource availability to name a few, Brian argues that automation and digitalization are a key part of the answer.
“Automation levels in later factories such as battery plants, will be higher by virtue of the fact that it’s a new sector making use of current technology; you wouldn’t build a factory today in the same way as many of the legacy or brownfield facilities we currently have in the UK,” he said. There are differences between sectors, which also became clear when Siemens was a contributor to the 2017 Made Smarter Report. The automotive sector has characteristically been a front runner in automation technology adoption through the need to invest at scale with ever shortening innovation cycles. This meant that it kept coming back to work with its supply chain and system integrators to install the ‘latest and the best’ – technology would add competitive advantage through productivity. Other sectors might lag-behind but manufacturers are now having meaningful conversations and, whether pushed by Covid or Brexit-induced labour shortages, sustainability, regulation, resilience or competitive pressures, they are approaching Siemens and other automation and technology suppliers, in unprecedented numbers. The need is urgent; the country’s economic future depends on improved productivity.
“Some companies are well underway with quite advanced digital thinking; not just about productivity but linking their digitalization efforts to the enablement of decarbonisation and sustainability,” said Brian Holliday. “There is increasing pressure to build greater resilience into manufacturing and supply chains too. It’s great that we have initiatives in flight such as the Made Smarter adoption programme, which helps the wider supply-chain and in particular, smaller manufacturing companies understand the benefits of, and how to exploit advanced technologies, including automation and 3D printing and digital twins. It’s important to highlight how accessible these technologies are and the business benefits of adoption.
Productive, innovative, adaptable
Siemens’ site at Congleton, Cheshire, has specialised in variable speed drives since 1991, although the plant itself was established 20 years earlier.
“The drives control the speed or the output shaft of an electric motor,” says Andrew Peters, Managing Director of Siemens Drives Plant, Congleton. “There are lots of applications that they are used for, such as fans for air conditioning systems; water or liquid pumps; and conveying systems with gearboxes, in warehouses, just for example.”
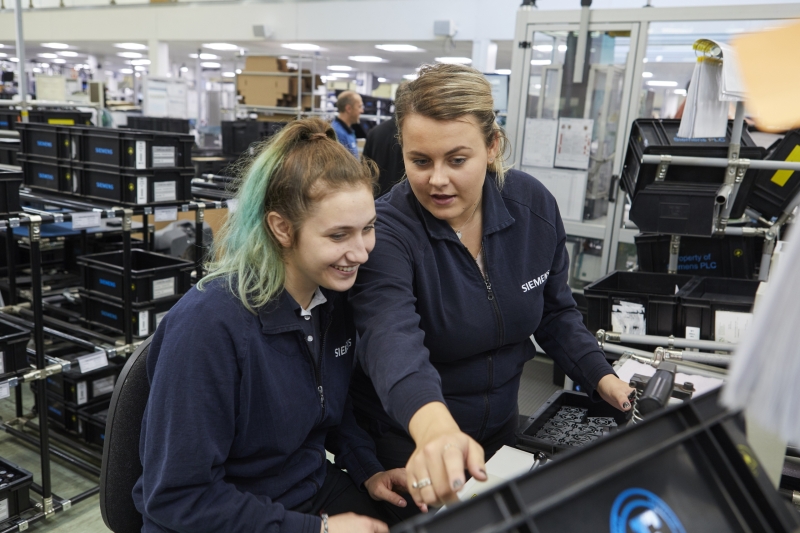
Siemens’ site at Congleton, Cheshire specialises in variable speed drives / Picture: Siemens
Rising demand has been driven, most recently, by the increase in home or Internet shopping and consumer fulfilment direct from warehouses. Another fast-growing market is the manufacture of electric cars.
“None of the automotive players has invested in internal combustion engine development in the past five years; it’s all about electric vehicles,” he says. “There is innovation in battery development and drivetrains but also in packaging. There is a lot of energy in those boxes and the gigafactories that are emerging will have kilometres of conveying, which needs to be managed. Our products may not be immediately visible, being located alongside assembly lines or in cupboards nearby, but they are very important to energy efficiency, as well as production.”
Siemens Drives Congleton expects to produce up to 600,000 variable speed drives during 2022, having started from zero in 1991. It is an impressive achievement, all the more so because that growth has been delivered with a workforce that is essentially still the same size.
“It isn’t about taking on more people to cope with volume, it’s about productivity – which is the reason why Congleton is still open; we are globally competitive with sister factories in China and elsewhere,” Andrew Peters says. “We have been able to drive productivity by seven per cent, year on year; doing more and more with the same number of people.”
The question is: how has this been achieved?
“Lean manufacturing and continuous improvement are obviously essential but it’s about what you’re making, as well,” he explains. Plants making ‘me-too’ products will inevitably decline. “It is very much about innovation, design and development. The big innovation at Congleton has been moving away from standard products to a configured, customised approach, about giving customers more choice.”
Automation is part of the story but Andrew Peters maintains that it is not simply about putting robots in.
“You have to look at your functional organisation, maybe even dismantle the functional organisations of procurement, quality, manufacturing, and R&D and create co-located sets of cross-functional team.” Congleton competes with low-cost labour in the Far East and German levels of automation with a mixture. “Our value add is not just the total value of the product to the customer; it’s the way in which we are designing and manufacturing.”
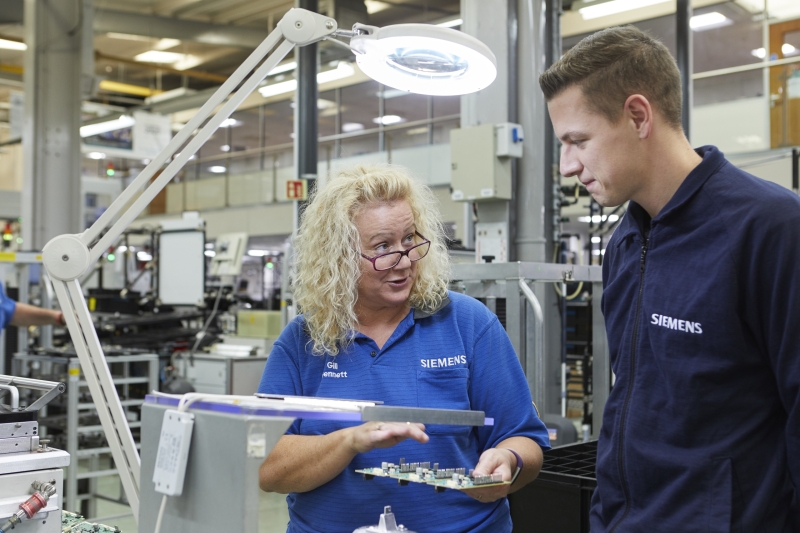
Siemens Congleton expects to produce up to 600,000 variable speed drives during 2022 / Picture: Siemens
Siemens Congleton’s digital transformation has delivered a shopfloor with virtually no paper; everything is digital and accessible by all who need it, instantly.
“The high variation, high variety products we are now producing, where we may have 50,000 different combinations, cannot be produced with individual paper orders. You cannot do it with individual paper orders and instructions for operators – it would take 10 years to read them,” he continued. “We have and are on a digital transformation journey with connected data. We are not contracting out complexity; we are striving to master it. We accept the reality that customers want what they want. We have created a lean, continuous improvement business that delivers their special requests.”
Siemens Congleton has an embedded apprenticeship, training and development programme, which embeds it with schools, nearby universities and UTCs (University Technical Colleges) and career-changing adults, too. A number of its suppliers are local to the plant, which gives it flexibility and responsiveness.
It adds up to a company that embraces change and delivers innovative products in a digitalised, responsive and profitable way.
Covid: Lessons learned and challenges overcome
Siemens Healthineers’ manufacturing facility in Sudbury in Suffolk celebrated its 80th anniversary in 2019, just before the outbreak of the COVID-19 pandemic. The facility manufactures blood gas analysis benchtop products, as well as diabetes and urine analysis instruments, along with consumables.
“Even in normal circumstances, our products are lifesaving, critical equipment for hospitals and this plant is the only place in the world that makes them,” said Ali Burns, Managing Director of Siemens Healthineers in Sudbury.
When news began appearing of hospitals being overwhelmed by COVID-19 patients in China and then in Italy, Ali Burns and his team moved very rapidly to ensure that its component supplies would enable it to meet what was expected to be a significant upsurge in demand. Expectations were accurate; the facility went from making twenty blood gas analysers a day to 70, overnight, with consumables following suit. Although the pandemic seems to have receded in the UK, Siemens Healthineers supplies globally and remains busy. The situation is not so good in, for example, Mexico or the USA.
“I expect there will be a peak in demand for the instruments and that the consumables will then plateau. I don’t see demand coming down; we have seen aggressive growth in the use of healthcare technology and we will expect demand to continue,” he explains.
Siemens Healthineers took an active role in the Ventilator Challenge UK; the emergency response by the UK’s manufacturing base to the need for fixed and mobile ventilators. The project, led by Dick Elsy of the High Value Manufacturing Catapult (HVMC), brought together the talents of UK-based companies from aerospace, automotive, the Formula One motor racing cluster and health technology. UK production was accelerated from a few units a month to delivery of over 13,000, in just three months.
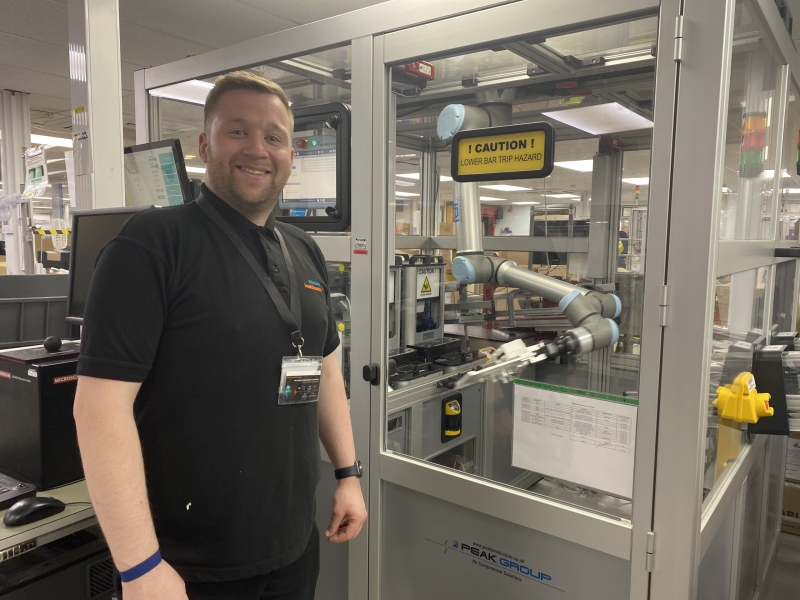
Siemens Healthineers’ manufacturing facility in Sudbury in Suffolk / Picture: Siemens
“COVID changed the world and sped up digital transformation by about 10 years,” says Ali Burns. “Among our challenges was the requirement to cope with restrictions on the number of people physically allowed on site, both production staff and suppliers. We used technology to enable people to start working remotely. We had to look hard at productivity and reviewed the application of the technology, along with what and how to automate things within the facility.”
They found that automation can actually be quite restrictive, particularly when it came to ramping up production, quickly.
“Automation is productive but COVID has taught us to think about surge capacity,” Ali Burns explains. “If there is a sudden rise in demand through then the fully automated system has to build another robot or open another production line. Human beings are flexible and learn quickly how to do new things or to do them better. We have to strike a balance.”
One of the ways Siemens overcame the problem of restricted site visits was to broaden the use of augmented reality (AR).
“We took to using HoloLens to show suppliers what we were doing. They could identify needs for maintenance and train our team to do it,” he continues. “When it came to designing equipment, AR enabled us to abide by COVID restrictions while delivering to customers’ requirements and expectations. I expect we will make more use of technologies like HoloLens because we see it as a more efficient way of working.”
Siemens Healthineers’ staff and partners have shown that they are very good at coming up with innovative ways of coping with challenges. The company has become more flexible but without losing focus on safety and quality. It also broadened understanding of the need for and benefits of community engagement.
“One of my engineers saw a request on Facebook during the pandemic from a nearby hospital asking if anybody could help them with IV drip holders. We have a 3D printer, with which we made one example and sent it to the hospital. They were delighted and asked if we could make some more. Then another hospital heard about it and asked for some,” says Ali Burns. “It’s not our field but our people did it because it was the right thing to do. It showed us that, as you move forward, those different types of technology will be used in a range of different ways.”
Lighten the darkness – sustainably and whilst nurturing talent
The Green Space – Dark Skies project involves up to 20,000 people from all walks of life and age groups in raising awareness of the value and fragility of Britain’s open spaces and natural landscapes. Young Engineers from Siemens developed low-impact lighting for the project.
“Green Space – Dark Skies is one of 10 projects forming part of Unboxed 2022, which is a festival celebrating UK creativity and innovation,” says Annabel Ohene, who joined Siemens when she was 18 and was sponsored through an Electrical and Electronic Engineering degree at Bristol University. After three summer placements with Siemens in Manchester and graduation, she was recruited onto the company’s graduate scheme.
“The projects are shaped across science, technology, engineering, the arts and mathematics,” she explains. “Siemens is the technology partner. Nathaniel and I have been working on it for 18 months.”
Nathaniel Fernandes, who attended the University of Southampton, gained a Master’s degree in Electrical and Electronic Engineering, also attended summer placements with Siemens and is now on the graduate scheme.
“We’re developing a brand new lighting system for the events in the National Parks. Geopositioning technology is incorporated into individual lamps,” Nathaniel says.
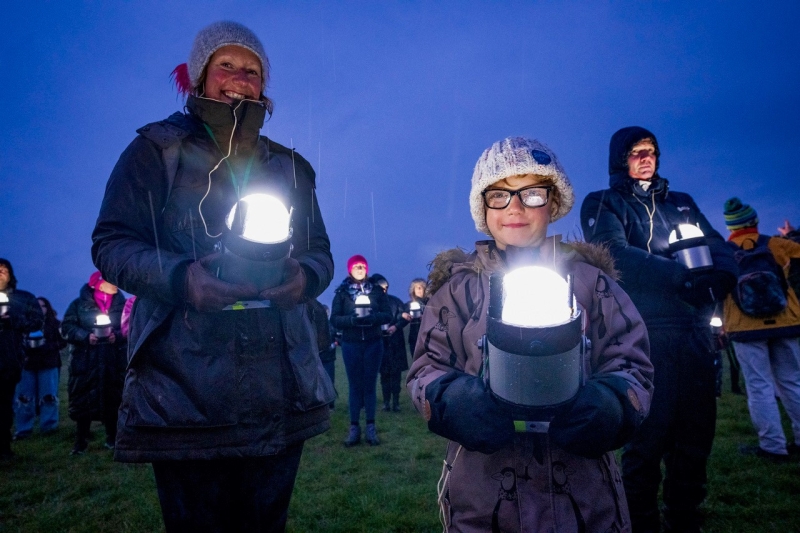
Young engineers from Siemens developed low-impact lighting for the Green Space – Dark Skies project / Picture: Brian Morrison
The project uses existing technology but in innovative ways. A great deal of planning has gone into the events, which will have members of the public moving around in perhaps unfamiliar areas and exploring them, while holding the lamps.
“We are going to be sending cool colour patterns to the lamps and the whole thing will be filmed from a drone above,” Nathaniel continues.
“Incorporating the geopositioning technology means that the people can be anywhere but the pattern will still be coherent,” Annabel says. “Each person will become a pixel in a larger image of live art.”
Each event will be filmed, around dusk. It may sound paradoxical but bringing light to dark spaces will raise awareness of the wealth of natural beauty around the UK, even quite close to cities and urban areas.
“The project is intended to improve public awareness of these areas and the need to conserve them so that, when people go out into the country, they do so safely and will treat the land respectfully,” Nathaniel adds.
The lights will have a legacy and lifetime beyond the Unboxed projects. The incorporation of geopositioning technology could help with displays for outdoor concerts.. Connectivity challenges, such as ensuring all lamps were linked to WiFi, were important problems to solve.
Annabel and Nathaniel began working on the project 18 months before the first event, on 23 April 2022, so they had to work under emergency Covid measures. This meant that physical meetings were restricted and even those working in the same premises could not necessarily meet up for an informal chat or brainstorm.
“It has been very challenging but I think Siemens is really very good at empowering graduates and apprentices to try and own things,” says Annabel. “Experience is an important factor but, with the right support, engineering apprentices and graduates are quite capable of taking on such responsibilities.”
“The example of the Ventilator Challenge came up a lot and what was really good for me was to get entry level talent together. Through things like hackathons and involving even undergraduates on summer placements, Siemens realised what an excellent talent pool it has,” Nathaniel concludes.
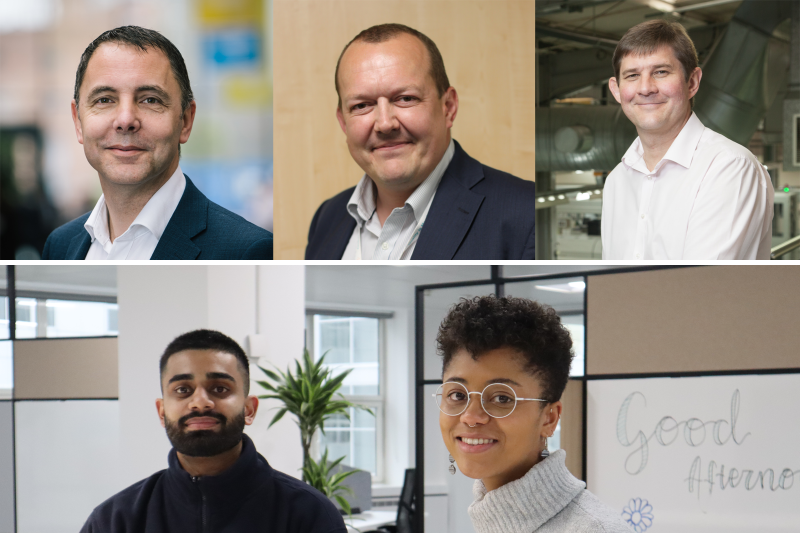
Contributors to this article include: (top row) Brian Holliday, Ali Burns, Andrew Peters and (bottom row) Nathaniel Fernandes, Annabel Ohene / Pictures: Siemens