5 minute read • published in partnership with KUKA
Case Study: Adding up the savings with RoboWAAM
The age of 3D printing, even of large and very large, safety-validated metal components for aerospace and construction has arrived. Of the many ways to decarbonise industry and society, some attract more attention than others. Lightweighting and waste reduction, especially in transportation, are essential parts of the solution but can seem low profile. But the question should be asked: why manufacture a component in the traditional way if you can save waste and weight doing it differently?
That is the central problem that Dr Filomeno Martina, Prof Stewart Williams and partners set out to solve at Cranfield University in a project that began in 2007. Large, load bearing structures – used in aerospace, construction, defence and other “big” applications – were typically CNC-machined and fabricated, producing megatonnes of metal swarf every year as an unnecessary byproduct. Companies were already printing components in other industries but 3D printing for safety-critical applications needed time, development, testing, and rigorous type-approval.
Fast-forward 15 years and WAAM 3D Ltd, a new company spun out from Cranfield, has launched its RoboWAAM and made it commercially available.
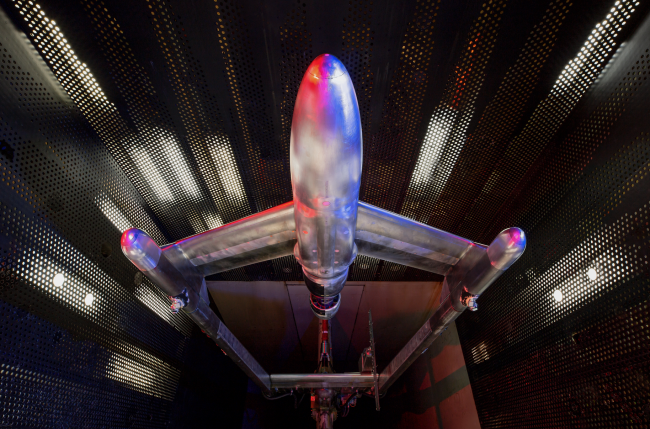
Picture: WAAM 3D
This is a fully integrated, turnkey wire arc additive manufacturing (WAAM) machine to print large and approved metal components, from nothing to the finished part. It eliminates wasteful machining and truckloads of valuable swarf. The specific technology that WAAM3D harnesses is DED AM (Direct Energy Deposition Additive Manufacturing). The deposition head is guided by a KUKA robot. The RoboWAAM cell is a game changer for companies because it provides everything the manufacturing team needs to fabricate these parts in a single, fully compliant package, with KUKA’s KR IONTEC, a versatile, modular robot in the 20kg to 70kg payload range. In previous years, printing such big parts had huge ‘demand pull’ from industry but not the supply chain – the materials, control system and process rigour – to support it. WAAM3D persevered and is now reaping the rewards. In June, the company won UK media company TCT’s 3D Printing and Additive Manufacturing Award in the non-polymer hardware category, against five strong entries.
KUKA: platform partner since Day One
The RoboWAAM machine is the granddaughter, and namesake, of an original R&D project part-funded by the government’s innovation agency, Innovate UK, in 2018. KUKA was, and remains, the original robotics partner for RoboWAAM. It was selected because of its desire to develop control parameters with the team, its willingness to partner on the development of RoboWAAM and the suitability of its robot controller, the KRC4. The project required a lot of technical developmental work for no quick return.
The 2018 project proved that 3D printing long-section (three metres plus), often heavy, metallic components, to specified physical parameters was possible but the technology needed several refinements and “packaging”, or simplifying, to appeal to industry. RoboWAAM has a robust enclosure, fully integrated safety guard access, a control station with integrated PC and twin screens, and a suite of proprietary WAAM3D software to allow production engineers to programme the part build with no need for deep expertise in either additive manufacturing or robotics.
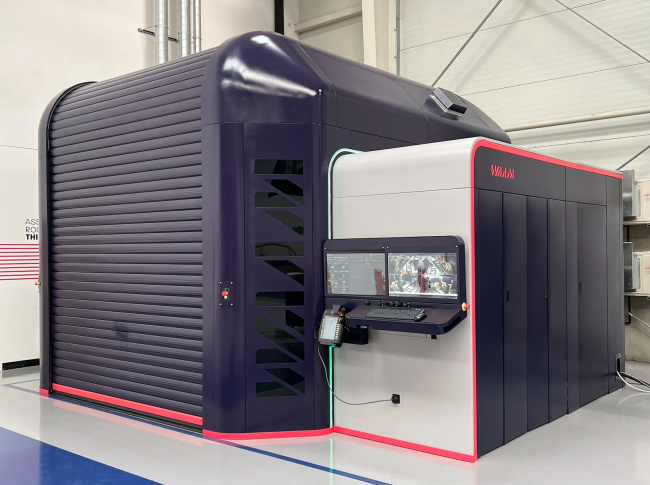
Picture: WAAM 3D
Control is everything in advanced manufacturing. Precise control gives these printed parts the validation they need to fly in an aircraft carrying hundreds of passengers. Dr Filomeno Martina, CEO of WAAM 3D, says “Two key features of RoboWAAM are that it is available as a plug-and-play package, rather than requiring a company to build the machine from separate, off-the-shelf parts. We have some off-the-shelf components, like the KUKA robot, but the core system uses our proprietary controls, our software and WAAM3D own sensors, which makes it very reliable and enables easier customer support. Secondly, the software has been painstakingly developed to be modular and intuitive, to help the expert or non-expert engineer to plan the tool paths, deposition parameters, and other background tasks.”
Software is provided in four modules, which break down the process of planning, setting up and delivering the parts: WAAMPlanner, WAAMKeys, WAAMSim and WAAMCtrl. WAAMKeys, for example, controls the print geometry, specifically the layer height using WAAM3D’s list of material-specific algorithms that automatically allocate process parameters around the toolpath – as well as offering compensation strategies to manage changing thermal inertia.
“This machine needs to work like a machine tool. Everything has been designed to squeeze additional performance out of (the machine), as opposed to additive systems adapted from standard welding kit, which require a lot of manual intervention,” says Filo.
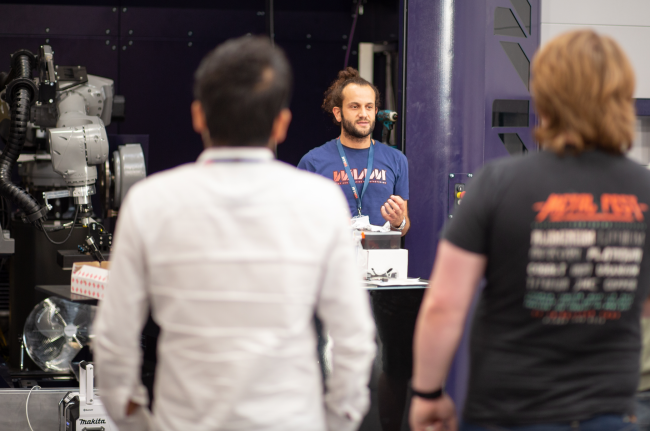
Picture: WAAM 3D
Operator interface – avoid costly errors early
Up to 60 sensors are fitted to RoboWAAM, with statistical process control applied to the most critical ones. If something goes wrong, the operator is alerted – the interface users a traffic light green, yellow and red system. The “build” is rendered on screen in a very modern User Interface, providing the realism that operators need as a veneer over the huge amount of data being generated during the building. “We look at that (data) as an opportunity, to continuously demonstrate that each part’s building stage, point by point, at each moment and stage, sits within a spec and is compliant. If it doesn’t fit in the spec, you have some recovery options, or you may have to discard, but the system reduces waste as much as possible.”
RoboWAAM is a triumph – an advanced, validated, turnkey 3D metal printing solution for large components, with accurate process control and metallic materials developed especially for the system. WAAM3D’s close partnership with KUKA and other technical partners is critical to ensure the system not only works well but is user friendly and provides multi-level control.