4 minute read • published in partnership with KUKA
Case Study: Arrival, its microfactories and reimagining the production process
The announcement of an order for 10,000 electric vans for global logistics company UPS brought the name of Arrival to global public attention. The company is a pioneer not just in manufacturing electric vehicles but in methods of manufacture, advocating ‘microfactories’ as a means to make the vehicles close to the market. Its manufacturing process may attract attention, as well; Starting with a blank sheet of paper, Arrival has reimagined the production process using in-house technology and vertical integration.
Arrival is a young company, brimful of novel ideas about sustainable transportation and how vehicles such as vans, buses and delivery robots should be built. Its Integrated Transport Ecosystem vision embraces transport solutions for cities and the people who live in them.
The vision sounds elevated but the plan for delivery is very much down to earth. Arrival’s first two vehicles – an electric van and bus – are designed to offer “human-centered and intelligent design”, and at prices comparable to fossil fuel equivalents.
The concept caught the eye of parcels delivery company UPS, which in January ordered a fleet of 10,000 vans and also invested directly into the company.
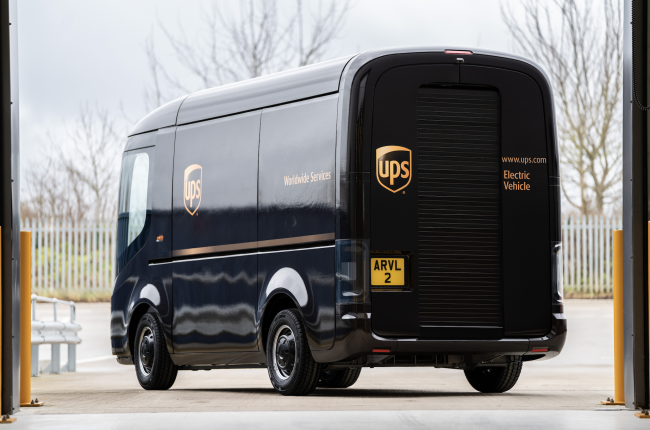
Arrival has reimagined the production process using in-house technology and vertical integration / Picture: Arrival
The conventional way of fulfilling such huge orders would be to boost production at existing plants – maybe take on an extra shift, if the order was big enough. Arrival takes a different approach. It intends to take a distributed manufacturing approach, deploying multiple microfactories around the world, close to the markets being served, utilizing and developing local skills and resource and paying local taxes.
Intelligent solutions
Arrival microfactories will be built inside a standard 200,000 sq ft (20,000 sq metre) warehouse or factory unit, which is around 24 times smaller than most mainstream automotive manufacturing plants. They will be highly automated, which is to be expected of a modern factory, but the real difference will be in layout – and how that layout will evolve. The machinery will be connected and the whole factory utilizes AI (artificial intelligence), in order to evolve and adapt itself to improve performance and productivity. Arrival’s first microfactory in Oxfordshire will feature KUKA robots.
“The microfactory concept takes a fresh look at manufacturing and natively applies modern technologies to maximise their utility from the start, rather than trying to robotize traditional production lines” says Doug Morton, Head of Technology Strategy at Arrival. “In this way, we can draw on alternative disciplines which offer the best value / approach, such as software design. It’s widely accepted that the best way to solve complex software challenges is to give computers the ability to learn, without being explicitly programmed, rather than design each element manually. If you define the rules and the desired outcome, you train the machine to make use of data to optimize everything in between. We are using this same approach in the design of microfactories”
A parallel to AI is the development of generative design, which has produced some very successful designs for automotive components, for example, that look nothing like conventional products. GM applied generative design to a seat bracket mounting point for seat belts. The software was instructed to consider additive manufacturing for production, which led to the design of a structure that looked as if it had been grown, rather than processed. It is 20% stronger than the original part but 40% lighter.

Arrival’s first microfactory in Oxfordshire will feature KUKA robots / Picture: Arrival
Designing for evolution
Arrival argues that generative design can also be applied to factory design – and that it will inevitably mean that factory floors and production lines evolve to look new and different to those of the past. At the moment, if anything in a traditional OEM factory is to be changed, the whole conscious process of design and testing has to be repeated, at great expense. Arrival is thinking differently – or rather it is encouraging AI to quickly adapt its processes.
“The thing that we really care about is that the output is efficient and robust,” Doug says. “If we liberate ourselves from the constraints of everything sub process and tiny activity needing to make sense to a human being, then we can unlock all of the potential that lies in the spaces between , in the gaps in time and in the natural variations.” He draws comparison with the natural world, with ecosystems that have evolved through the process of natural selection.
“Ecosystems and biological organisms, which themselves are terrifically optimized, have absolutely no responsibility to make sense to us. They make full and effective use of all the available resources in a way that human-designed structures and systems often do not.”
Doug says that factories are typically optimized for the human operator. The Arrival microfactory already looks different because production units are in squares, rather than along linear assembly lines. Rather than operating at specific speeds with stations in a specific order, the order of technology cells in a microfactory can be easily changed, or the same cell can be used multiple times on the same vehicle, enabling microfactories to build multiple different vehicle types.
“What we do with the microfactory is relinquish the desire to know explicitly in advance how each operation will be performed,” he explains. “If the location changes every time, it doesn’t matter; what the machines are doing is planning to get the right parts, each time. While humans adapt to overcome limitations in existing production processes, we see a very compelling opportunity to overcome the inefficiencies of the traditional factory environment.”