4 minute read • published in partnership with Atlas Copco
Case Study: Compressor investment helps blinds manufacturer plan for growth
Ventura Enterprise is a start-up manufacturer offering bespoke integral blinds for double-glazed windows and bi-fold doors. The company has invested in multi-tool CNC drilling and punching machines to maximise throughput and boost their competitive edge. These machines have been powered, without issue, by an Atlas Copco G15FF 10 bar air compressor since their original installation.
As an innovative alternative to conventional types, integral blinds fit into the airgap between the two double glazing glass panes within the window or door frame. They are compelling solutions for many reasons: They are neat, tidy, and compact compared to external blinds, and need less time and cost for maintenance. Also, unlike external types, integrated blinds are not susceptible to damage through careless use. As they do not gather dust, they offer a hygienic choice for environments like hospitals.
Ventura currently offers magnetically controlled units, but they are developing electrically controlled versions that recharge either from a solar cell or a mains-powered charger. One remote control will operate up to four blinds.
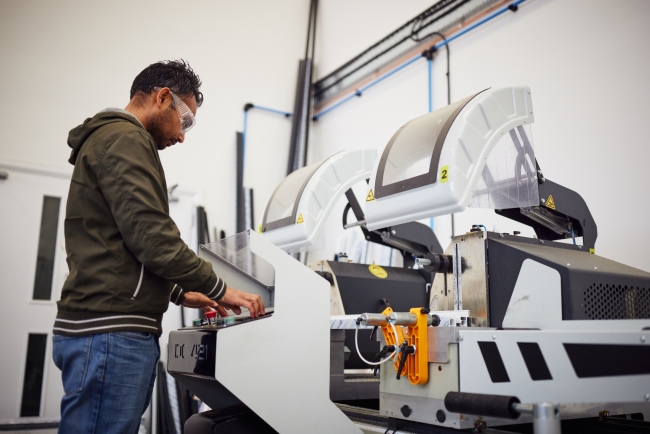
Picture: Atlas Copco
Highly reliable compressed air power
While setting up their operation, Ventura needed to source a rotary screw air compressor to power all of their manufacturing equipment. And as Pritesh Patel, Director at Ventura, pointed out, the compressor had to be completely reliable, as their entire manufacturing process depends on it. Accordingly, the company chose an Atlas Copco G15FF 10 bar tank mounted oil-injected rotary screw compressor for four reasons: Firstly, Atlas Copco was recommended to Ventura by a colleague who had highly favourable, problem-free experience in using Atlas Copco products. Secondly, Atlas Copco was a well-recognised brand name with many good reviews. Thirdly, the price offering was attractive – an especially important consideration for a start-up making a large number of capital purchases to set up their manufacturing facility. Finally, Ventura was also able to purchase the compressor through The Compressor Store, Atlas Copco’s online store, which was convenient and included free delivery.
Although a 10 kW compressor may have been sufficient to handle current production requirements, Ventura decided to futureproof their operation by going for the extra capacity of the 15 kW machine. They also purchased an output filter to ensure delivery of optimum quality air to their manufacturing equipment, to avoid risk of damage.
“Atlas Copco delivered the compressor, and we were able to install it ourselves along with the pipework,” commented Pritesh Patel. “It’s now been running for four months without issue – it has been perfect!” He continued: “We are very happy with the way business and production have been developing, particularly as we are now receiving larger orders. We are targeting large buildings like hospitals to help with their hygiene requirement, but also other commercial premises, where people often use windows carelessly and damage the blinds attached.”
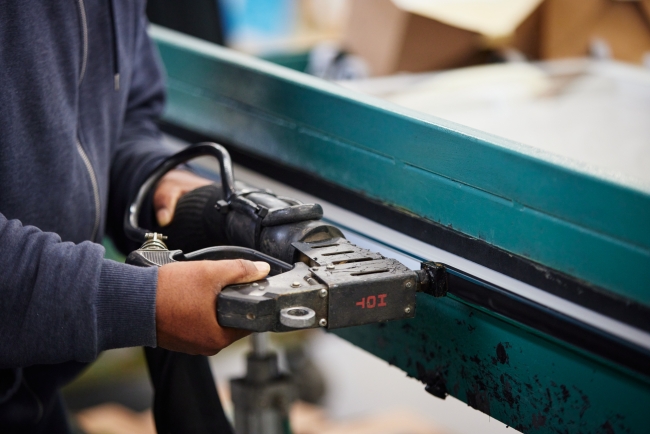
Picture: Atlas Copco
An ideal compressor for smaller businesses
The G15FF 10 bar air compressor is particularly well suited to the demands of smaller businesses. The belt-driven compressor only needs a single-phase supply while being quiet, efficient, powerful, and reliable. This robust package is highly affordable, as a low initial investment is followed by efficient, low maintenance operation.
Its state-of-the-art compression element IP55 (TEFC) totally enclosed motor meets or exceeds IEEE and NEMA Premium efficiency standards, with greased for life bearings. Its robust air filter offers a long lifetime and high reliability for long service intervals and is easy to replace. Additionally, its built-in refrigerant air dryer cools the compressed air and removes any moisture before it can enter the compressed air network. This prevents rust in the compressed air piping and avoids damage to any connected equipment or machines.
The G15FF also installs unobtrusively into small production facilities and workshops. With a fully integrated, compact controller, it makes the best use of valuable floor space. It has a sound insulation canopy and does not require a separate compressor room; it can be installed into most environments, right in the heart of the user’s workplace.
“The G15FF has proven to be ideal for a small business like ours, without expertise in compressed air technology,” commented Pritesh Patel,” It was straightforward to install as a compact yet complete, ready to go unit, and has worked reliably, with low maintenance requirements, ever since installation. With its built-in spare capacity, we are confident that it will support our manufacturing operation for many years to come.”