6 minute read • published in partnership with Kawasaki Robotics
Case Study: How a German brewery automated its entire bottle production process
In 2017, the Westheimer Brewery in Sauerland, which was founded in 1862, took the first step towards automation with a Kawasaki palletizing robot. In the meantime, the entire bottle production has been successfully automated with further robots – from empties management to filling the bottles.
The Gräflich zu Stolberg’sche Westheimer Brauerei in Marsberg (Sauerland) has been brewing regional beer specialties for the German and international markets for more than 150 years. To assert itself in the long term in a competitive market and successfully prevent the worsening shortage of skilled workers, the Westheimer Brewery decided a few years ago to automate its entire production step by step – with great success to date. The core objectives were clear from the outset: on the one hand, to reduce the need for new employees and, on the other, to make processes more precise, flexible, and controllable. They were to be traceable and more efficient. “As early as the 1990s, there were the first attempts at automation at Westheimer with the introduction of a PLC,” recalls technical manager Thomas Juckenath, who has been involved in the topic ever since. “Particularly practical: the Mod BUS systems chosen at that time work perfectly with Kawasaki robots. The basic program created at that time has been the basis for all automation ever since and is constantly being developed further.” Growing product diversity: speciality beers for the German and international markets
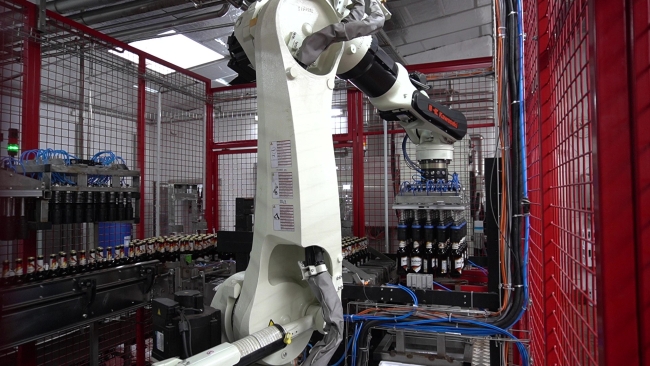
Picture: Kawasaki Robotics
Shortage of skilled workers and predictive maintenance
In-house training and further development of skilled workers has been an important success factor for the Westheim brewery for decades, explains master brewer Jörg Tolzmann: “Longterm retention of good skilled workers is crucial, because the shortage is clearly noticeable in the brewery and the craft sector, especially in rural regions like the Sauerland.” As in almost all industries, there is fluctuation, and retaining experienced employees is particularly important these days – because new employees are increasingly difficult to recruit in brewing and craft industries. Forward-looking work is also becoming an increasingly important factor in ensuring capacity utilization and conserving resources – including human resources, according to Thomas Juckenath: “Where previously there was a short-term response to possible disruptions in production or the older equipment, and repairs and maintenance were carried out as required, the question now is: What can precautions look like before something breaks?”
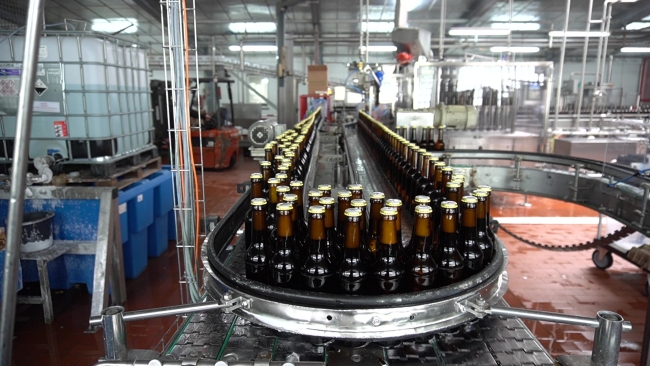
Picture: Kawasaki Robotics
Step by step: automation strategy since 2017
Until 2017, mainly older mechanical solutions were in use at the Westheim brewery, some of them from the early 1980s. In particular, the old palletizing system took up a lot of space in the brewery with limited room and was very susceptible to malfunctions. Thus, for brewmaster Jörg Tolzmann, this was the logical first step for automating the entire infrastructure and production. With a Kawasaki Robotics CP500L palletizing robot, the full automation of bottle production began. After a discussion at the Hannover Messe 2017 and a detailed consultation on site at the brewery, the choice quickly fell on a Kawasaki Robotics CP500L high-performance palletizing robot. In addition to the speed and precision of the robot, decisive purchasing arguments included the simple setup and programming, the independent loading of the machine, and the Cubic-S safety system. A new chain gripper for the same purpose would have been many times more programming-intensive and prone to faults. With a Kawasaki Robotics CP500L palletizing robot, the complete automation of bottle production began.
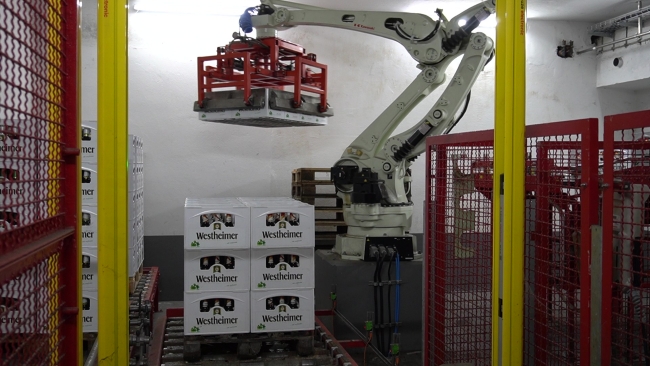
Picture: Kawasaki Robotics
The added value of the robotic system quickly became apparent: Previously, the palletizer had to be shut down step by step, then the pallet was loaded manually and finally removed – separately for full and empty crates. Now the employee responsible is significantly relieved physically and primarily drives the forklift truck. Both the full and empty crates now run down a conveyor belt, are automatically pushed into position, and placed on the pallet by the robot. An important advantage is that many more crates are on the move at the same time. Thanks to optimum capacity utilization, they no longer must be parked to one side as in the past – everything happens automatically. After the successful setup of the palletizing system, the modernization of the entire bottle production followed – with two additional Kawasaki robots of the type BX200L for packing and unpacking the bottles in the centre. Their integration was also very straightforward: Because all relevant machines basically remained in the same place and the robots only require a small footprint, only safety fences and new belt settings were necessary.
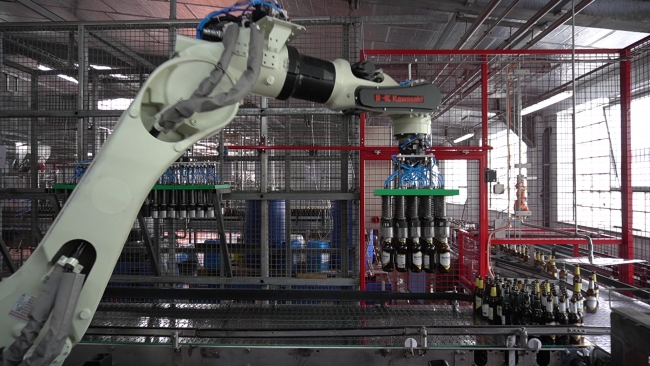
Picture: Kawasaki Robotics
New challenges in the brewery market
The brewery market has changed massively in recent years: “It used to be one type of beer – in small and large bottles. Today we have several private labels, lemonade, and other beverages, and produce for other companies. In short, there is an incredible variety. Our team and production facilities are being challenged much more than before,” says Jörg Tolzmann. The new robot-assisted production offers the necessary flexibility for this: For example, the Kawasaki Robotics BX200L in the packing station can pick up molded parts independently and thus change over to new varieties in the shortest possible time and without any effort. The laborious and time-consuming changeover of the line is no longer necessary. “Our team has really got some breathing room,” says a delighted Thomas Juckenath.
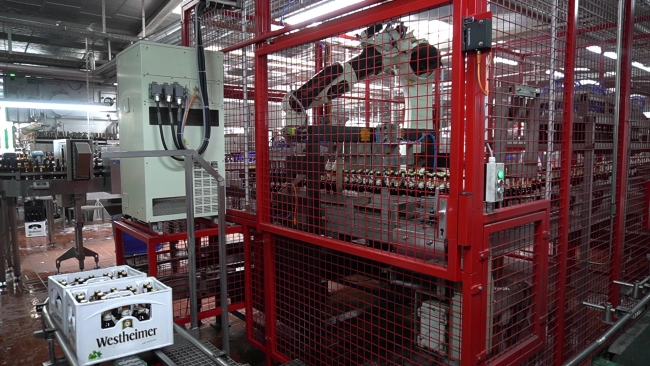
Picture: Kawasaki Robotics
Setting up the plant
A Kawasaki Robotics BX200L removes empty bottles for further cleaning. Production operates on two linked levels – handling empties and end products below and filling above. The crates with empties are fed from the first floor to the bottle line via a conveyor system. There, a BX200L robot removes the bottles from the crates with a gripper and places them on a conveyor. The crates are cleaned in a waiting crate washer and fed to the packer. A Kawasaki Robotics BX200L removes empty bottles for further cleaning. The empty bottles are transferred to the bottle washer via a feeder. There, the bottles are first checked for damage, incorrect shapes, and similar factors, and then intensively cleaned. After cleaning, the bottles are additionally checked by an inspector. Only the bottles in perfect condition move on. They are then filled, checked again, labeled, and packed into the crates provided by the packer – another BX200L. By switching to double crates, the speed of the packer has recently been significantly increased once again. The filled and ready-to-sell crates are then fed via the conveyor system to the palletizer for further processing. Acceptance among the workforce was quickly very high and the robots are perceived as a great relief, according to Jörg Tolzmann: “In the past, you had to get bottles out manually, check them, move pallets here, etc. The robots are a tremendous relief. The robots are an immense relief – physically above all.” And the maintenance factor has also exceeded all expectations, says Thomas Juckenath: “Everything runs perfectly. Maintenance once a year, batteries replaced, grease check – that’s it.”
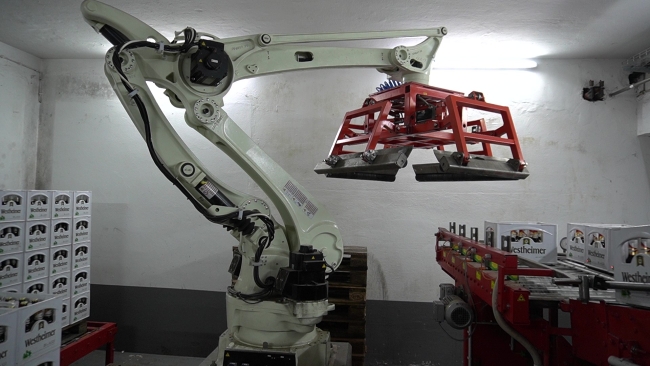
Picture: Kawasaki Robotics
Summary of the automation
Above all, the significantly reduced running costs – especially compared to older machines – have proven to be a tangible advantage for the Westheimer brewery after only a short time. “The robots run easily and reliably. The whole thing becomes more maintenance-friendly,” says Thomas Juckenath. Automation of production was also an important help during the corona pandemic: although the effects on the restaurant trade and the reduced demand for draft beer were clearly noticeable, the demand for more bottled beer and greater product variety – including non-alcoholic beverages – could be met flexibly. This meant that capacity was always fully utilized. Another BX200L packs the filled and labeled bottles into waiting crates. The filled crates are fed to the palletizing robot on the lower level for further processing. Now that bottle production has been fully and successfully automated, the focus is now on the keg line or cask production. Initial considerations are already being made for the full automation of this line as well – for example, the handling of the very heavy kegs is to be simplified.