4 minute read • published in partnership with Ideagen
Case Study: How global snacking giant, pladis, improved global compliance operations
As a global snacking business with 34 factories in 13 countries, pladis Global is certified to the BRC Global Standard for Food Safety and, within its health and safety function, its sites are compliant to ISO 14001 and OHSAS 18001.
As Global Head of Health, Safety, Security and Environment for pladis, David Orton is responsible for defining and developing the company’s health and safety, security and environment strategy which enables the company’s sites to provide safe workplaces and to operate with safe working practices.
Key to this strategy is ensuring that all sites comply with pladis’ global standards and policies, as well as maintaining compliance with laws and regulations in the countries in which they operate.
“We were looking at merging several systems into one platform that could bring our crisis and incident management (CIM), auditing and document system controls together,” explains David. “We had various different systems, some regional, some site-by-site, but none of them were linked together, which made it very difficult to understand just how well we were managing health, safety and environment and food safety and quality and security across our business.”
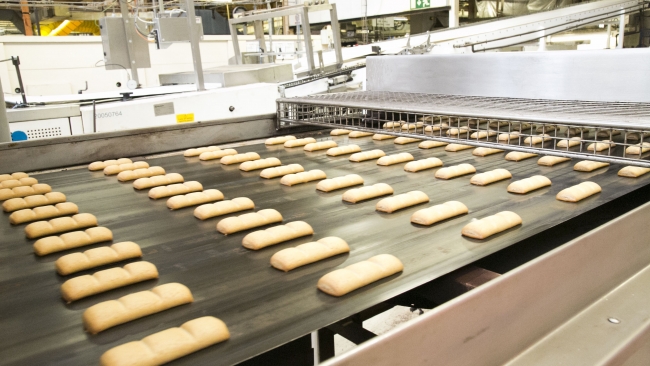
pladis Global operates 34 factories in 13 countries / Picture: pladis/Ideagen
As both Chief Safety Quality Security and Environment (SQSE) Officer for pladis and Chief Safety Officer for Yildiz Holding, Denis Treacy is responsible for ensuring that the company is able to protect its consumers, its employees and the environment, as well as the footprint that it leaves. “We source our materials around the world, so we want to make sure not only that the materials we buy are of the substance, nature and quality that we expect, but also that the way those businesses operate is ethical, environmental and meets with our pladis beliefs and business values.”
He continued: “As we’re a global business operating across continents, time zones, languages and cultures, in order for us to bring all of this together into a cohesive, agile and reactive process, we needed an integrated management system.”
How did pladis ensure global compliance operations and improvements?
pladis, which owns snacking brands such as McVitie’s, launched a new software system to enhance its global safety, quality, security and environmental (SQSE) operations which in turn boosted compliance.
The global snacks leader replaced a series of current legacy systems with Ideagen’s Coruson software as it looks to streamline several operational processes.
Coruson became the company’s single system for SQSE, helping pladis enhance quality, speed of manufacturing and distribution as well as the safety and security of its 26,000 staff globally.
“For us, Coruson had the best combination of availability, of system performance and trading off the different elements required between CIM, audit and document management,” says David.
“Coruson enabled us to develop our own global SQSE integrated management system into a platform that meets the requirements of our certifications. Through doing that, it allowed us to make it quite clear how we meet those international standards and therefore when we are audited against them to be able to demonstrate simply that it is quite a benefit.”
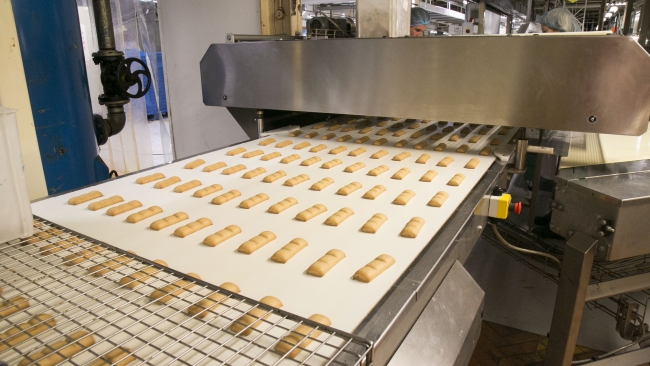
pladis has to ensure that all sites comply with global standards and policies, as well as maintaining compliance with laws and regulations in the countries in which they operate / Picture: pladis/Ideagen
Ruth Furborough is Global Head of Audits and Assessment for SQSE at pladis and said: “We used to conduct all of our internal and external supplier audits via Excel spreadsheets, which was quite a painful process for us, but Coruson now gives us greater visibility of audits, both internal and external and the progress that’s been made on them.
“The mobile app allows us to action any issues that are identified during audits with our suppliers in real time and our suppliers can also now access the system and directly input the actions that they’re taking, so it saves everyone a lot of time.”
Andrew Cheale is Group Consumer and Product Quality Manager at pladis and is responsible for consumer, customer and CIM management, which includes consumer care, customer issues management and crisis and incidents management.
“One of Coruson’s strongest points is its workflow management, which ensures that, at each stage in the incident recording process, you have completed it, closed it out, assigned the tasks that you need to and made sure that everyone who needs to be is responsible for each action that you have.”
“We have Coruson for CIM, document management and audit and assessment,” continues Andrew. “But we want to make sure that as many of the technical applications that fit with the system can be added and that people can use it as a one-stop shop for all of the technical requirements.”
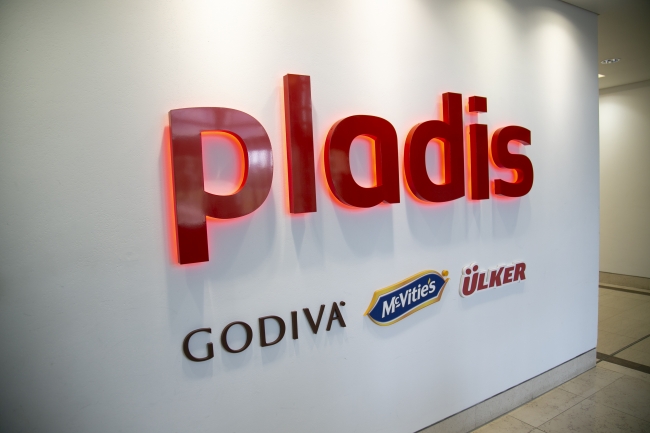
pladis launched a new software system to enhance its global safety, quality, security and environmental (SQSE) operations which in turn boosted compliance / Picture: pladis/Ideagen
“Coruson enables us to apply pladis’ global standards across all the different countries that we operate in,” added David. ‘In addition, it has the flexibility to allow each region to then add to those standards where applicable to meet the legal requirements within that country.
“By putting the right documents into Coruson, managing any crises that we do have correctly through it and, ultimately, the more proactive internal auditing of our locations to ensure they do meet our required standards and continue to deliver – all of that helps drive our strategy of promising happiness to the world with every bite.”
Denis concludes: “My responsibility is for the wellbeing of 26,000 employees in 13 countries around the world to ensure that they get home safely to their families every night, whether they are operating a factory in Nigeria or driving a car across Turkey to deliver a product.
“And with 4 billion consumers, an information system that gives me the information I need to provide the right decision support to the business is critical. The system must deliver consistent and repeatable processes so – welcome to pladis’ IMS system.”