4 minute read • published in partnership with KUKA
Case Study: How KUKA is helping to bridge the skills gap with The NITC in Northern Ireland
The Northern Ireland Technology Centre (NITC) at Queen’s University Belfast, has been working for 53 years to bring practical solutions and helpful innovation to businesses operating in the aerospace, transport, automotive and other industrial sectors, whether suppliers or OEMs. Its customer base includes Saab AB, Airbus and Spirit AeroSystems.
“Located at Queens University Belfast, the NITC is an industry-facing part of the university. The NITC is an innovation centre working at TRL4-7,” says Colm Higgins, manager of the NITC, who has been at the institution for over 20 years. “Our goal is to translate research from the university through to industry, help it to implement and apply the latest technologies and to make manufacturing businesses more productive and competitive.”
Colm describes the NITC as “well-networked with other research technology organisations, particularly the HVM Catapult centres” collaborating on projects in Aerospace and Made Smarter technologies. The NITC will become a key component of a £90 million project in Northern Ireland called the Advanced Manufacturing Innovation Centre (AMIC), which will build on the NITC’s history and develop the relationship with the UK’s High Value Manufacturing Catapult network on a more formal basis.
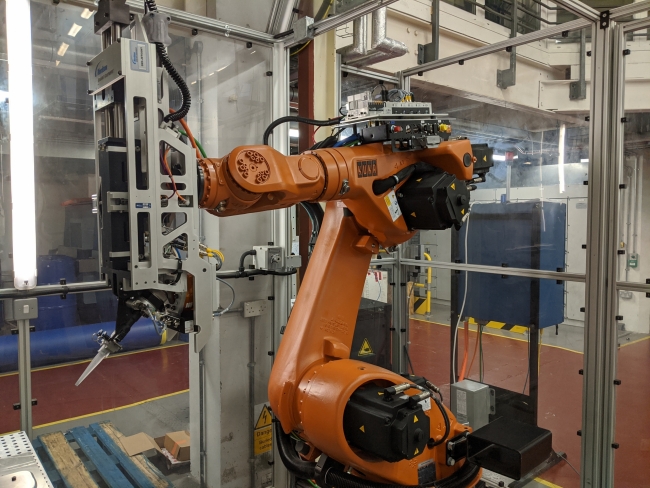
KUKA and the NITC are helping more manufacturers bridge the skills gap by helping them embrace robots and automation, and support with staff training / Picture: Queen’s University Belfast
While it gets involved in large, collaborative R&D projects funded by the UK government’s innovation agency, Innovate UK, for example, with the clear intention of disseminating to industry at higher Technology Readiness Levels (TRLs), NITC will continue to be driven by customer and industry need, while translating academic research from Queen’s University.
Knowledge transfer
“A lot of our work starts in the aerospace sector and expertise and experience gained there is translated to other businesses, maybe at a slightly lower level,” Colm continues. “We have done some very innovative work in automating the assembly of aircraft structures. Our target with the supply chain would be to help them become more cost-effective and efficient, in order to better engage with their OEM customers.”
Aerospace companies work with exotic alloys and lightweight materials that are not very easy to join. It’s a big challenge and experience and knowledge gained there can be applied in other sectors.
“Our traditional TIG and MIG welding is used across aerospace and other sectors, but we have done development work in the laser welding of titanium, for example, and in a European project called Oasis, with Saab and TWI, looking at friction stir welding and laser beam welding of alloys,” Colm says. “Welding in aerospace is really challenging to implement, particularly with structural components. The stress specialists still favour the riveted solution. The technologies all demonstrate capability and significant cost and manufacturing savings but certification remains a challenge.”
Material handling on the up
Aerospace is not NITC’s sole focus. As well as aerospace, the MIG and TIG in particular, is being utilised with wider industry, including in materials handling, agri-tech, transport and wider metal fabrication, working with aluminium, steel and similar materials. OEMs in these sectors include Terex, Sandvik, WrightBus, McCloskey International and it is undertaking innovation activity in their supply chains.
“There is a very significant supply chain in the material handling sector in Northern Ireland. It is worth about the same as aerospace,” he says. “That’s where we see a lot of growth in our welding activities.”
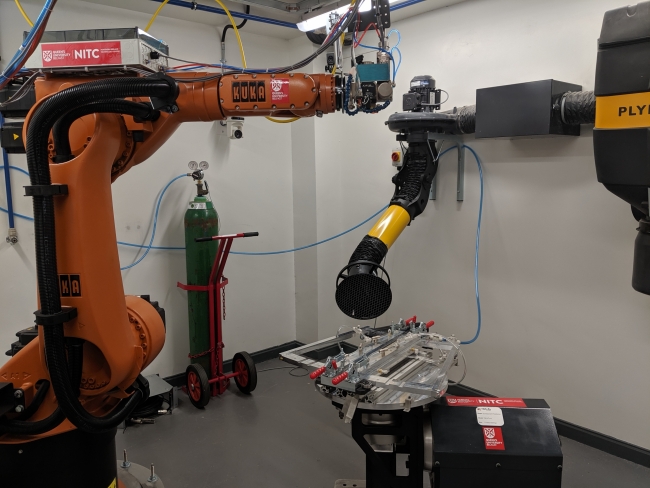
The NITC helps bring solutions and innovation to businesses operating in the aerospace, transport, automotive and other industrial sectors / Picture: Queen’s University Belfast
Demonstrator, laser and sealing cells
The NITC has a MIG robotic welding cell commissioned by Bauromat, the integrator company and KUKA Systems Partner. It includes a KUKA KR8 welding robot, which is fitted with a Fronius welding kit and one tonne tilt and turn manipulators.
“This is a development cell so the head and tail are on one side of the tilt and turn,” Colm says. The cell gives NITC a good demonstration capability and the centre is planning to put in a new TIG system in 2022, as part of a new project.
“We have reasonable welding capability already but if we want to scale up then we come back to digital simulation. If a customer is looking at welding something larger than our capacity, then we validate the simulation with our cell and then demonstrate what a bigger cell would look like in their factory using these digital tools. We demonstrate how it can be integrated into their line and how it would impact production.”
As well as the demonstrator cell, NITC has a cell equipped with a KUKA KR 60 with an IPG laser welding head. It uses sensors to collect data, perform more in-line monitoring and boost quality control – all of which are vital in mission-critical processes such as aerospace applications, for example. The third robotic cell uses a KUKA KR 60 to develop robotic sealant applications for aerospace repair in partnership with a company called Nordstrom.
Bridging the skills gap
The challenge in the availability of trained welders is keeping the NITC busy. “The shortage of skilled welders means that companies are looking urgently at automation and roboticized processes,” says Colm. “NITC wants to help businesses avoid too much dependency on the ‘black box’ solution, to recognize that it needs to upskill the workforce and have more robot capable engineers.
“We are encouraging companies to look at their own workforce. We are looking to make robotic welding more efficient, to raise the technical capabilities within the business and, to get them to understand and implement more automation.”