3 minute read • published in partnership with Mazak
Case Study: Sky is the limit for Tridan Engineering
What began as a private three-man company has grown significantly over the last 50 years to become one of Essex’s premier independent engineering firms. Established in 1968 in Clacton-on-Sea, Tridan Engineering is a subcontract manufacturer of high precision components, globally shipping around 9,000 parts each month.
Able to manufacture everything from small components to workpieces up to 1.6m in size, in single units to large batches, Tridan supplies a variety of industrial sectors including aerospace, defence, medical, marine, high-end automotive, food manufacture and communications.
Meeting the tight turnarounds associated with these industries is a major undertaking. In order to remain competitive, Tridan needed a state-of-the-art machine shop to ensure it had the in-house manufacturing capabilities to keep pace with demand. That’s why ongoing investment in machine tools, alongside a relationship spanning nearly three decades with Yamazaki Mazak, has played a crucial part in Tridan’s success.
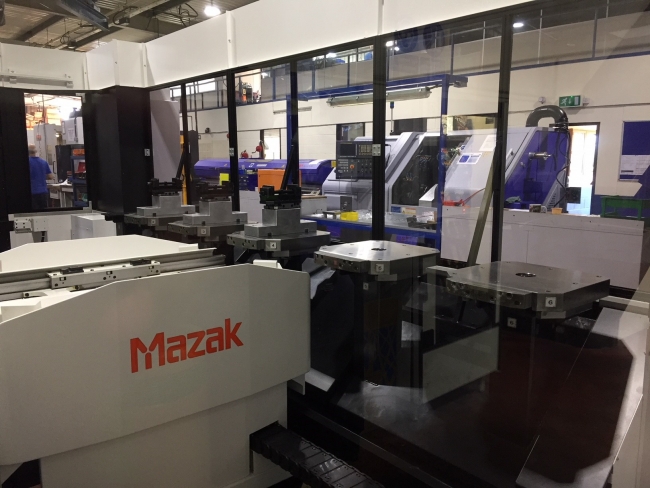
Tridan has grown significantly over the last 50 years to become one of Essex’s premier independent engineering firms / Picture: Mazak
Paul Hawkins, Managing Director at Tridan said: “We bought our first Mazak machine back in 1990. It was an AJV 35-80 twin pallet machining centre – a beast of a machine. That is long gone now, but our relationship with Mazak remains.”
One glance around the factory floor, and this is clear to see. Tridan has 14 Mazak machines for turning and milling applications. In the last two years alone, however, Tridan has acquired two VARIAXIS i-500s, one of which features a PALLETECH automation system; a VARIAXIS i-600, a VARIAXIS i-700, a QUICK TURN 300 and a QUICK TURN 200 MSY. Mr Hawkins even welcomes other local machine shop managers who are considering investing in a Mazak machine to visit and take a look.
“A big turning point for us as a business was in 2007, when we gained AS9100 accreditation. This allowed us to target aerospace and defence, and move away somewhat from the commercial sectors. But this bought its own challenges – a pursuit for continuous improvement and extreme demands – and our factory floor today reflects our growth and the part we play in this supply chain,” continues Mr Hawkins.
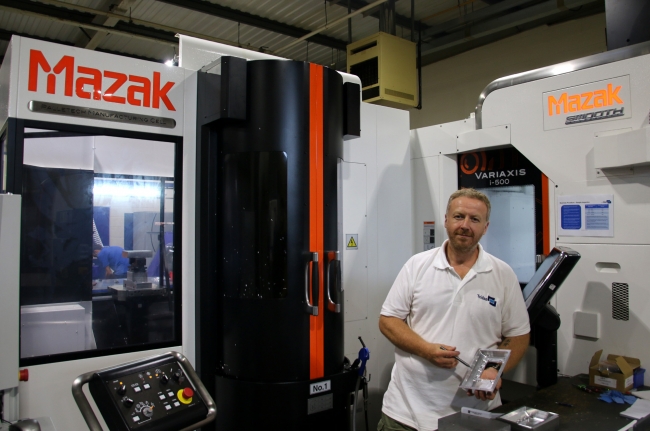
Tridan has 14 Mazak machines for turning and milling applications / Picture: Mazak
However, it’s not just the machines list that has grown. The company is now 70+ strong, and is one of the biggest employers in the area.
“Being based here means you look one way and it’s the sea, and you look the other, and it’s the draw of Chelmsford and London. This can make it a challenge to attract and retain local talent, particularly when there is an industry-wide skills shortage already. However, we’ve made a real concerted effort to grow and develop young talent and for the last decade, we have invested heavily in our Apprenticeship Scheme, forging strong ties with nearby schools.”
The results of this effort are clear for all to see. The programme has seen 21 apprentices come through its doors, but perhaps most impressively, out of the 74 strong team, 15 have completed apprenticeships with Tridan.
Paul Coupland, Machine Shop Manager, at Tridan, added: “For us, the Mazak machines have been an invaluable tool to train our apprentices on. They constantly give reliable results and the beauty with a Mazak is that the controls are so similar through the progressions that it doesn’t take a lot of training to get onto another machine. This means most of our operators can use every machine within the factory, which allows us to be extremely versatile and achieve quicker set-ups.”
In particular, Mr Coupland praises the Mazak SmoothX control, the world’s fastest CNC. “The SmoothX revolutionised our operations and has delivered a complete step-change in how we operate. We have it installed on the VARIAXIS i-700 and i-500 and it’s resulted in much faster processing times, allowing us to run parts off quicker than ever, but also with more accuracy. The operators are really enjoying using it too, which is an added bonus.”
Looking ahead, the business has recently invested in a further third of an acre alongside the site, opening up the prospect to expand by an extra 10-13,000sqft. With this in mind, Mr Hawkins concludes: “We’re a high user and advocate of Mazak, and with this extra space, it would be fair to say that there is a very good chance we’ll be looking to buy more Mazak machines in 2019.”