4 minute read • published in partnership with KUKA
Case Study: The automation doing a better job in the dairy industry
Milking cows is a challenging process that involves synchronisation, engineering, animal welfare, hygiene and sanitation. The precision and consistency of post-milking disinfection can be improved through an automated robotic system, leading to healthier, happier and higher yielding cows.
There are over four million dairy milkings each day in the UK alone. Teat infections caused by mastitis or environmental bacteria affect the cow’s health and reduce milk yields, so accurate and effective disinfection is essential. Farmers and milk buyers seek high animal welfare standards, improved milk quality and reduced use of medical treatment. Post-milk teat disinfection is essential to achieve these objectives.
The IDS (Intelligent Dairy Solution), a teat post-milk spray system by Peacock Technology, uses a KUKA robot guided by Peacock’s proprietary vision system to achieve post-milk spray disinfection on rotary milking parlours.
Every cow’s udder is different. Teats are different in size and are positioned in different places depending on the size and age of the cow. The IDS uses 3D vision to identify the teat location, and then accurate and effective application of the disinfectant. Occasionally, a teat should not be sprayed, if damaged or dysfunctional. Gareth Hughes, Operations Director at Peacock Technology, explains, “In contrast to factory automation where the robot action can be identical every time and interacts with inanimate objects, with dairy cows in the real world each animal is different, the system must assess each udder individually to decide how to treat each cow.”
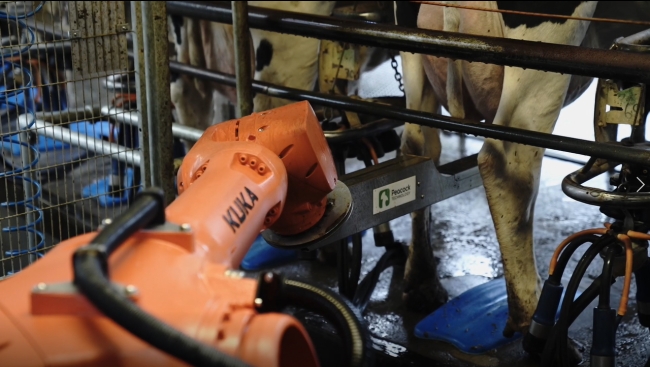
Picture: Peacock Technology
Robots do a better job
Normally left to human workers, post-milk teat disinfection is repetitive: the worker may have to focus on this single task alone for a four-hour shift, often early in the morning. Simultaneously, the importance of this task demands close and careful attention. Farmers know that manual spraying consistency can decline over time, due to repetitive strain issues or attention fatigue. Independent benchmark testing has shown less than 50% of the teats being satisfactorily disinfected by manual spraying alone.
Peacock’s IDS post-milk spray system is able to repeatedly achieve 100% teat coverage. “It shows emphatically that automated spray application provides a consistency that the farmer was previously not able to achieve,” says Gareth.
Moreover, farms are increasingly struggling to find labour. Brexit has reduced access to the EU labour pool and, during the covid pandemic, local families who had worked on farms stayed at home. “Dairy farmers are now very switched on to the benefits of technology and more are concluding that our IDS systems are a better approach, because unpredictability of the quality and availability of labour is proving too big a challenge for many farms,” says Gareth.
Peacock Technology’s system is already installed throughout the UK, with planned installations abroad in the coming year.
Time-of-flight technology
In rotary milking parlours, cows enter a stall on a large carousel that rotates. After milking, she arrives at the IDS spray disinfection robot. A time-of-flight camera system, custom developed by Peacock, identifies the presence of the cow in the milking stall then moves the spray tool between the cow’s legs, then identifies the precise coordinates of each the four teats to direct the spray precisely.
CCTV cameras are fitted to every robot and the system is remotely monitored 24-hours a day. Peacock has built its IDS Teat system so that, unless there is a physical failure, 95% of issues can be dealt with remotely and the farm can be back online in 20 minutes.
Dairy is a low margin business. Farms need high volumes to make a living and if cows contract illness and stop producing milk, high costs can be incurred. Because Peacock’s IDS robot system helps prevent infections and improve yields, it can demonstrate very fast payback – ROI is often less than 12-months.
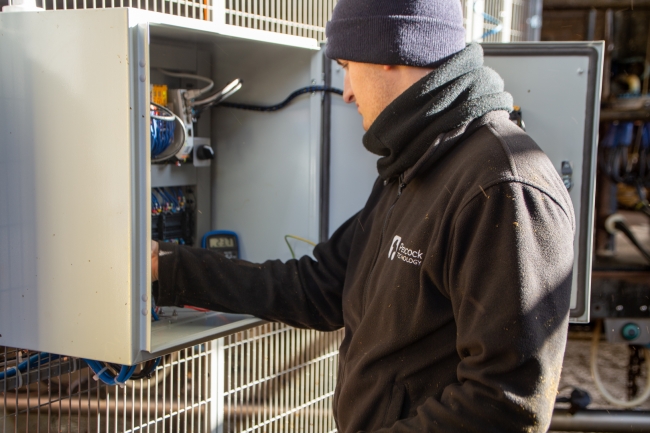
Picture: Peacock Technology
Big farms demand fast turnover
Takt times – in this case the per cow time – for teat spraying range from six to twelve seconds, making speed as important as accuracy, but larger herds can demand takt times of just four seconds. Again, KUKA can help. “The flexibility of KUKA’s conveyor tracking software allows us to claw back a lot of dead time, so that we can include the maximum available time to the process,” says Gareth.
The challenge is in the dynamic nature of the application, where every cow at every milking has a different set of coordinates, but the time allocated to each cow must remain constant.
Why KUKA?
The IDS Post Milk System is designed using a KUKA robot and its controller – KUKA is the sole robot supplier for this system.
Peacock chose KUKA for several reasons. “In our experience, KUKA has one of the best performing robots for this application. And it has a huge support network worldwide,” Gareth says. “The flexibility of KUKA’s KRL programming language was also a major reason for choosing it.” KUKA’s software has allowed Peacock to push the boundaries in automation. “Often with PLC and robot suppliers there is a hard stop,” he explains. “The KUKA software allows lots of flexibility; there is wide interconnectability between different devices when we needed to work with third party suppliers to maintain the speed and accuracy of the application for other non-robotic elements.”