3 minute read • published in partnership with KUKA
Costs, skills, quality, carbon: new KUKA robots provide answer to industry’s many pain points
A new report from KUKA UK and Ireland shows industrial companies many real examples of companies using robots to cope with a host of challenges: labour shortages, accuracy, quality, labour retention and flexible hours – as well as cutting carbon and bi-product waste in every customer example.
An LCD monitor recycling system that processes 10-times more LCDs than the manual rate. A plug-and-play robot operated metal additive manufacturing machine for +one metre aerospace components. A dairy automation system that disinfects cows’ udder teats before and after milking, saving time and raising hygiene standards.
These and other examples show the versatility and variety of robotic automation in 2024. And they have something else in common essential to manufacturing operations that are facing higher costs, labour shortages and pressure to decarbonise: they also show how robots can reduce waste and carbon while increasing repeatability and quality. As UK job vacancies across manufacturing top 76,000 – and 62,000 in the construction industry1 – with immigration being controlled and a rising wave of industrial retirees coming
These case studies and others are a key part of a new report on robots and automation by leading robot supplier KUKA UK and Ireland. Stronger, faster, more productive_the endless opportunities for robots and automation is a new 32-page analysis of the use of robots in the UK and Ireland. The range of applications for robots is richer today than ever, as more companies discover the capabilities of robots, their accuracy, repeatability, and the range of end-effectors to fulfil complex tasks.
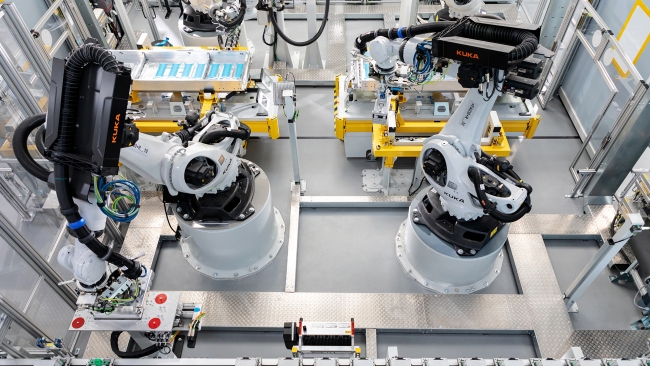
KUKA has released an industry report to highlight many real examples of companies using robots to cope with a host of challenges / Picture: KUKA
A cocktail of tough business challenges can partly explain both a strong year for robot sales in 2022, and the proliferation of new applications. Component shortages, labour shortages, rampant inflation, high energy bills, automotive electrification, near full employment.
“Neither the UK nor Ireland, but especially the UK, has a cogent industrial strategy – we’ve tried but there is clearly no appetite for this in government,” says CEO of KUKA UK, Jeff Nowill. “Inflation means margins are being stretched to the limit in traditionally strong robot markets, so KUKA is pursuing new applications, and factors like labour shortages and accuracy mean there are many companies which have adopted robots that were previously unknown to us. New robot technology, customer digital applications, the range of robot sizes, and competitive pricing means that new customers are now actively enquiring about robots, rather than needing any hard sell.”
The KUKA report covers:
• Seven customer case studies showing the advantage of robots for very different businesses. Common themes are waste reduction and high productivity
• Expert overview of the manufacturing sector and robot market forecasts from seven KUKA UK and Ireland experts with decades of experience.
• New digital customer services – including KUKA.Sim, my.KUKA and WarrantyPro – give customers more effortless support than before. From simulating the application to post-commissioning, unlimited maintenance visits, including preventative maintenance, using WarrantyPro.
• Robot range: explanation of each KUKA robot class, from the 3kg payload Delta robot to the 1,300kg KR1000 Titan, via the popular QUANTEC and CYBERTECH ranges commonly seen in automotive and mid-range industrial applications.
• Network power: KUKA’s System Partner network gives companies twice the technical support: 31 Platinum partners across UK and Ireland, with Gold and Silver partners, provide very narrow application experience, combined with KUKA Group’s IT systems, troubleshooting and maintenance support, means companies can keep their robots running for longer with more uptime.
• It’s not only manufacturing: FUTURECAST is a construction manufacturing centre in Ireland that is rethinking building and quarrying to make better use of the tech-based skills of young people to overcome the industry’s image as a dirty and dangerous occupation. The centre also addresses sustainability and embraces solutions such as the adoption of green energy.
• Training: different levels of training, including planning, operation and maintenance, to end-of-life. KUKA provides a continuous learning cycle, depending on customers’ skills levels.
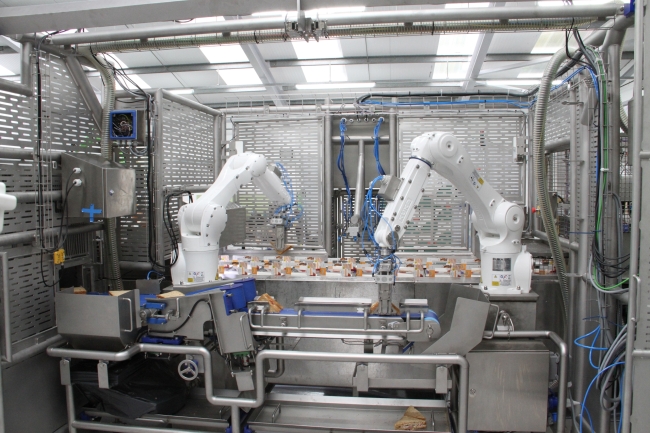
Stronger, faster, more productive_the endless opportunities for robots and automation is a new 32-page analysis of the use of robots in the UK and Ireland / Picture: KUKA
Robots are an important decarbonisation solution
The report regularly points to areas where KUKA robots reduce carbon, waste and energy consumption.
The seven cases studies, covering diverse businesses from LCD screen recycler Votechtik and pharmaceutical device manufacturer Merck Millipore, to 3D printing companies FUTURECAST and WAAM3D, all have a low carbon, waste-cutting story to tell. In a robot refurbishment story for a global automotive customer, KUKA demonstrates its commitment to the environmental impact of precious metals and rare earth materials, as robots old PLCs are refurbished and given a second life with other customers and applications. And the KUKA QUANTEC range typically uses many recycled parts.