3 minute read • published in partnership with KUKA
Feature: Robotics and automation are propelling the food industry forward
The food industry now ranks as the UK’s largest, overshadowing the automotive and aerospace sectors combined. But, as a market that is both dynamic and continually diversifying, consider functional foods and plant based alternatives, KUKA Robotics looks at why the need to adopt automated technologies is key to remaining competitive in both domestic and international markets.
The 2023 Food and Beverage Industry Report numbers show that more brands are embracing digital tools to automate manual processes. Senior VP of Marketing & Business Development Gary Iles at TraceGains said, “Rather than allow market conditions to overrun their business, more food and beverage brands are taking matters into their own hands. The future looks bright for CPGs that remain focused on putting consumers first by bringing new products to market faster and more cost effectively.”
Growth in the food industry could be attributed to several influencing factors, including but not limited to increases in demand accelerated by ecommerce and household commercial trends and a rising population. Whatever the reason that growth and demand must be managed. Reacting to changing market dynamics is not enough – the ability to predict when and where fluctuations may occur and proactively manufacturing to satiate that demand is key. Utilising big data and using digital tools, and robots fall within this category, can enable a factory to operate more efficiently and flexibly as demanded by the consumer.
KUKA’s wide variety of robot applications in the food industry
Using big data is much more simple than it sounds. By leveraging big data manufacturers can enhance efficiencies across many aspects of their operations. This means that by collecting and analysing large amounts of data across internal production processes and looking at market trends, manufacturers can gain valuable insights into areas for optimisation, including identifying production bottlenecks, and optimising resource allocation. This level of visibility enables manufacturers to make data driven decisions based on fact, rather than trying to predict what might happen. This level of visibility can have a positive impact in areas such as inventory management; using only the base materials that are needed, reducing waste and costs associated with storage, and even in areas such as recruitment and staffing – using only what is needed to operate cost efficiently – lets substantiate that…
According to a report by recruitment firm Robert Half, UK SMEs spend an average of £125,347 annually on recruitment costs. These costs can escalate however if the recruitment cycle has to be repeated, which can be the case when hiring transient labour. That’s a huge amount off a business’ top line. But why not use robots? You have the data, you know when your busiest periods are and the volumes that align with these peaks. There is no need to hire, and hire again, but invest once, in automation. There’s no need to retrain or educate staff upon multiple product iterations or packaging configurations, just the necessary application input into your automated system. Changes in product dynamics can be attended at the push of a button.
But, once this technology is in place, how do we optimise and manage it. Data!
Data analytics can enable predictive maintenance, which allows manufacturers to anticipate equipment downtime and schedule proactive maintenance activities, which minimise potential downtime. Platforms such as KUKA’s iiQoT which at entry levels is free to use enable the uptime of robotics assets through with condition monitoring, asset management and/or predictive maintenance.
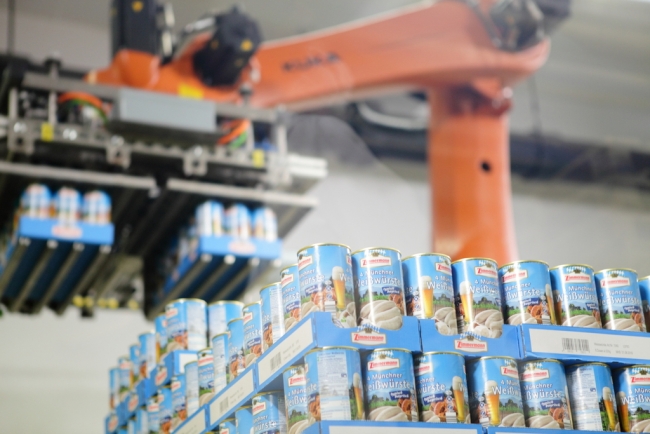
Food manufacturers need to adopt automated technologies is key to remaining competitive in both domestic and international markets / Picture: KUKA
Overall, the utilisation of big data empowers food manufacturers to make data-driven decisions that drive efficiencies, reduce costs, and enhance competitiveness in the market, and remaining competitive relies upon the ability to compete with technology.
The UK’s current robot density is 111 per 10,000 workers which is woefully below the global average of 141. What does this mean? Essentially that the UK is not as productive as our international peers, we can’t manufacture as cost efficiently as our competitors because we are too reliant upon an aging, and expensive workforce. The stark reality is that the UK cannot compete on an international stage unless we automate.
So coming back to the topic of data, by using robotics and automation we are not only increasing our ability to compete, but we are making available a whole new internal perspective of how productive we are, or may not be and improvements that need to be made.
We are operating in the digital age so it makes sense that surely we should be harnessing the power of digital tools?