4 minute read • published in partnership with KUKA
Feature: Scotland’s big plan to upgrade manufacturing
Scotland has a long and proud manufacturing heritage but some of its traditionally strong industries – shipbuilding, steel making, railways – have declined due to the impact of globalisation. It also features pockets of very modern manufacturing and the heritage of a big electronics manufacturing industry.
“Making Scotland’s Future”, the Scottish Government’s manufacturing action plan launched in 2016, set out a route map of capabilities, training, and technologies Scotland required to invest in to become an internationally attractive manufacturing destination. At the heart of the programme is the National Manufacturing Institute Scotland (NMIS), which is operated by the University of Strathclyde, part of the High Value Manufacturing Catapult and located within the Advanced Manufacturing Innovation District Scotland (AMIDS) in Renfrewshire.
The NMIS Group forms a proactive network between industry, academia, and the public sector. It includes specialist technology centres, the University of Strathclyde’s Advanced Forming Research Centre (AFRC), and the Lightweight Manufacturing Centre (LMC), along with its Digital Factory and Manufacturing Skills Academy, which are both fully operational and will be housed in the new NMIS headquarters currently under construction near Glasgow Airport and set to open later next year.
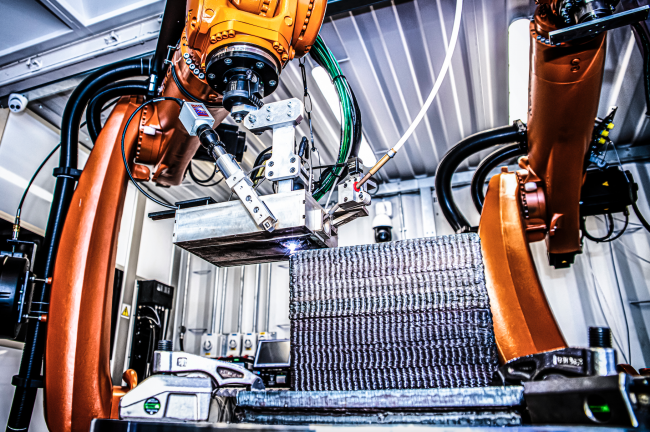
KUKA supports the National Manufacturing Institute Scotland to automate the manufacturing of 3D metal components layer-by-layer, creating an accurate and repeatable process / Picture: NMIS
As the future of manufacturing, NMIS’s ambitions are to:
• Increase productivity by reducing barriers to innovation
• Grow the economy by galvanising investment and increasing manufacturing competitiveness within Scotland and internationally
• Catalyse job creation and strengthen supply chain links across the country
• Provide leadership, build collaborations, and enhance capability to influence adaptation and exploit manufacturing opportunities, boosting Scotland’s transition to a net-zero emissions economy by 2045
• Inspire and attract talent, while equipping current and future workforces with the skills they and the manufacturing and engineering community need
NMIS engineers, automation experts and consultants work with manufacturing businesses of all sizes from across the manufacturing and engineering sectors to improve manufacturing processes and products.
“We’re providing leadership, building collaborations, and enhancing capabilities to influence how industry adapts, while exploiting manufacturing opportunities to boost Scotland’s transition to a net zero emissions economy by 2045. We work with manufacturing businesses of all sizes from across the globe and in multiple sectors, providing benefits across the whole of Scotland and beyond,” says Dr Misael Pimentel Espirindio e Silva, who currently leads the wire-arc additive manufacturing (WAAM) area within NMIS and is a Knowledge Exchange, Associate Manufacturing Engineer.
How does NMIS support manufacturers?
Filling the space between fundamental academic research and industry, NMIS provides access to cutting-edge R&D facilities and talented engineers, researchers, and business professionals, who are securing the manufacturing sector in Scotland and the UK for generations to come.
Research and Development is critical to promoting innovation. As a result, NMIS is constantly developing its technical capabilities. Through this it helps businesses improve their products and processes, allowing them to better compete. From solving the toughest manufacturing challenges to exploring the benefits of digital technologies or navigating the early days of new product introduction, NMIS helps organisations take a step back from day-to-day operations and provides a fresh perspective to stakeholders.
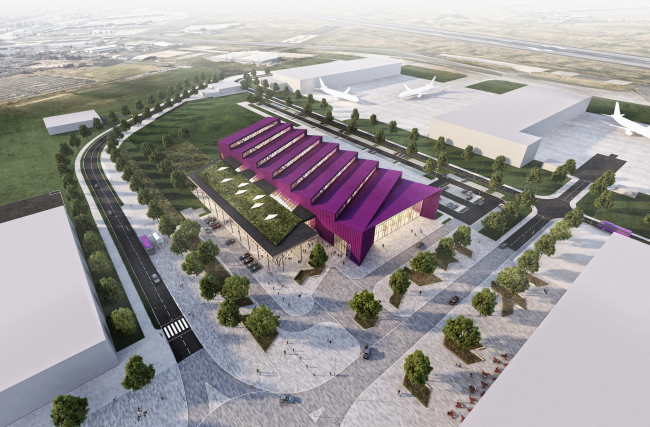
NMIS’s ambitions are to increase productivity, grow the economy, catalyse job creation and strengthen supply chains, provide leadership and to inspire and attract talent / Picture: NMIS
The role of KUKA robots at NMIS
NMIS is a leading research centre for WAAM. Researchers and engineers use KUKA robots to automate the manufacturing of 3D metal components layer-by-layer, creating an accurate and repeatable process.
“The robots permit more flexibility during metal deposition, while delivering more accurate outcomes when compared to manual procedures,” says Scott McKegney, who leads WAAM research as Knowledge Exchange Associate Manufacturing Engineer at NMIS. According to Scott, “it allows for consistent beads and geometries, leading to better repeatability of the process.”
WAAM permits the production of large-scale metal components for various applications. Within NMIS, these include valves for the oil and gas industry, structural seats in naval and commercial shipbuilding, and landing gear lugs for aerospace.
“We are using both WAAM cells in High Value Manufacturing Catapult (HVMC) funded projects within NMIS as well as in collaborative R&D projects such as the ATI Sprint Hybrid DED (Direct Energy Deposition),” says Dr Pimentel, who is leading the collaborative project. “Led by NMIS and funded by ATI, this project will assist with developing alternative manufacturing routes for the fabrication of aerospace components using WAAM.”
Beyond WAAM, NMIS and the University of Strathclyde is using robots for other applications such as non-destructive testing (NDT), grinding and polishing, and cobots for loading CNC machines with parts. Its NDT research will lead to in-process monitoring, where a weld and/or layer will be deposited and assessed in the same operation using a robot, saving hours of valuable time.
NMIS also promotes research around other welding technologies, where it will use robots to achieve the quality and repeatability required by manufacturers. For example, the WAAM team is exploring different ways to improve gas metal arc DED and plasma arc DED processes. Using the latter, the ionisation of gas produces a plasma, melting the alloy wire fed into the system.
“Both processes offer pros and cons and are selected based on deposition rates, finish bead quality, materials being deposited, metallurgical considerations and cost,” says Scott McKegney.
“This research, with and without robots, is a good fit for our wider aims at NMIS since welding and joining, as well as additive manufacturing technologies are essential for sectors such as construction, oil and gas, maritime, and aerospace, where Scotland has heritage but requires modern approaches and innovation,” he adds.