5 minute read - 19th April 2023
Forterra’s new factory: big on sustainability, big on automation, big on intelligence
Building products manufacturer Forterra has invested almost £100m into the redevelopment of its Desford factory, which will officially open in May 2023. Incorporating state-of-the-art innovations with sustainability mechanisms, robotics hardware and packaging solutions, the project is set to ensure the Leicestershire factory becomes the largest and most efficient brick factory in Europe.
Situated just two miles from the M1 with excellent transport links, the new Desford site will offer a range of red and buff bricks designed to meet the demands of housebuilders across the country.
Energy efficiency
At the heart of the plant’s efficiency improvements will be two new kilns that use cutting-edge technology to reduce energy consumption and carbon emissions. The main benefit of this kiln is its greater thermal efficiency, which comes from the innovative kiln-car design and additional thermal insulation, leading to greater emphasis on whole-life costings and greater energy savings. Additionally, more modern control hardware and methodologies allow for tighter control over the kiln conditions, creating the most efficient use of fuels for the process.
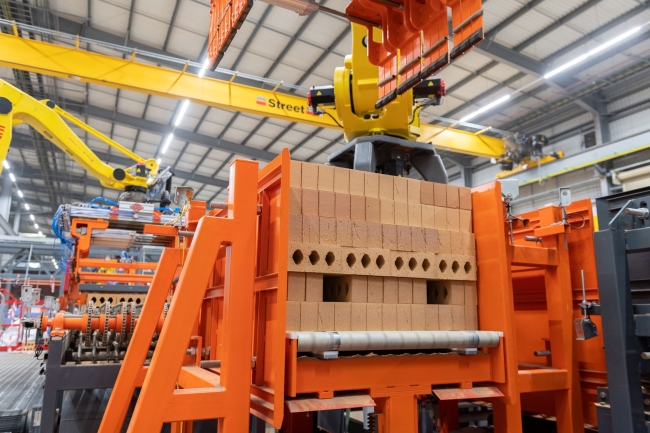
Picture: Forterra
Never miss the latest manufacturing news by signing up to our newsletter here
Modern kilns consume less gas and have more effective emissions-scrubbing technology, reducing the emission of carbon dioxide as well as other harmful waste gases. Supplementing this, the plant will incorporate a tunnel dryer, which is superior in its thermal efficiency compared to the more common chamber dryer that was in place at the previous site and many other UK brick plants.
Cumulatively these innovations will enable the new factory at Desford to emit approximately 25% less carbon dioxide per brick than the old factory, a reduction in emissions that is well in line with the industry drive towards sustainable production.
Increased productivity
The Desford factory will also see a massive increase in the volume of production, from the previous number of approximately 80 million bricks per year to an impressive 180 million bricks per year, which in turn will result in far better economies of scale. On a company-wide level, this factory redevelopment alone translates to a production increase of 16% from 2025 onwards.
In addition to the reduced emissions from the new kilns, the Desford factory will generate a large proportion of its energy from solar panels installed there. There are just over 7,000 of these solar panels being used, which will generate approximately 2.9 million watts of power, thereby constituting around 16% of the onsite electricity demand. This innovation is set to help Forterra lead the way in modern sustainability initiatives in the UK construction industry as 2023 begins.
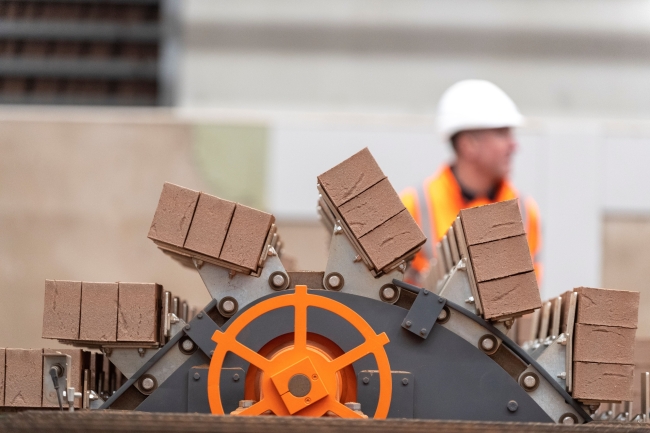
Picture: Forterra
Alongside sustainability solutions designed to reduce emissions, new technologies and methods are being implemented to reduce plastic usage and wastage. Forterra has partnered with packaging machinery and consumables suppliers to introduce a new type of packaging to the UK brick industry, that is specific to the needs of a hoodless pack. This ‘belly-band’ solution will be implemented at the Desford factory, and has already been implemented across 30% of Forterra’s production, including at Accrington Brick and Kirton.
This new packaging solution will use 36% of the amount of plastic used in the previous packaging technology. Part of this new packaging is a belly wrap material, 30% of which is composed of recycled polythene, sized to be as thin as possible without incurring any reduction in performance. This is necessary because on a hoodless pack there is one layer of rotated bricks that is at a greater risk of falling out of the pack when being transported via forklift. The belly wrap was developed to specifically retain this layer of brick while keeping the amount of plastic used at a minimum.
To integrate this packaging solution into the production line, Forterra has utilised horizontal banding machines, which are fully automatic and excel at high-speed strapping for high volumes of product.
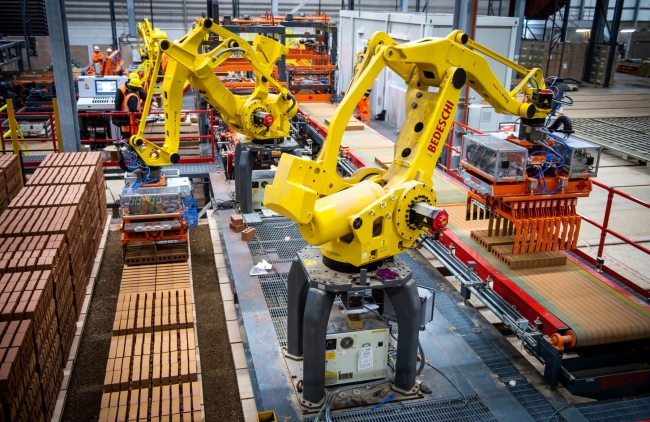
Picture: Forterra
Robotics
The overall philosophy of the plant design is twofold. First, that there should be no single point of failure; and second, that in the cases where there is a breakdown, any repair should take less than fifteen minutes to complete. This will enable the plant to have class-leading levels of OEE (Overall Equipment Effectiveness) beyond anything else that is seen in the UK brick industry.
The Desford site will also involve digital and telematic transformations as Forterra stays abreast of cutting-edge technology. The brand-new manufacturing SCADA system is able to feedback what kind of faults a machine has suffered each shift, right down to a component level, so that the question of what needs to be fixed or optimised is not limited to what the naked human eye can observe. With the SCADA system in place, faults will be picked up far earlier, meaning that not only will they be fixed faster, but that more significant breakages will be avoided pre-emptively. Where machines previously needed to be serviced every few months in order to check for faults, regardless of whether there were actually any faults in place, the new technology will ensure that only those machines in need of repair will be serviced, thus allowing for a more economical, high-performance approach to production.
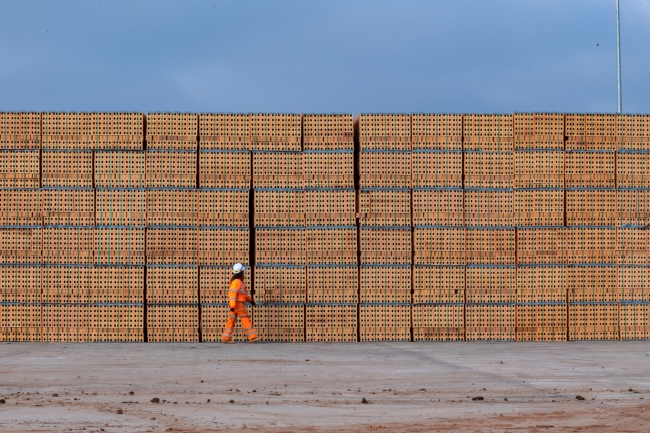
Picture: Forterra
In combination, these innovations will ensure that Desford is not only the largest brick factory in Europe, but that its high production capacity is coupled with excellent standards of sustainability alongside a modern approach to streamlining and optimising the entire production process. To ensure continued production during this redevelopment project, the existing Desford factory remains open and continues to produce high quality bricks.
Neil Ash, CEO of Forterra, said: “With ambitious ESG targets to reduce our carbon output by a further 32% by 2030, we know that sustainability has to be approached holistically, which is why at Desford we’ve incorporated advanced sustainability mechanisms across all aspects of production, packaging, and delivery. Complementing this, the factory’s impressive production capacity makes it the largest and most efficient brick factory in Europe. This will ensure we can manufacture hundreds of millions of bricks per year using a process that has been streamlined to be efficient and sustainable while satisfying the ongoing demands of our customers.
“The Desford factory complements several other investments and developments Forterra have made over the past year, such as a solar farm, which will render 70% of our power usage electric by 2025; a new eco-fleet of trucks, which will reduce our transportation emissions; and new packaging solutions, which place us a step closer to our goal of attaining a 50% reduction in single-use plastics by 2025. We’re delighted with the progress made at Desford, and eagerly await the full factory opening in May.”