3 minute read
Getting your business Industry 4.0 ready
For mid-sized manufacturers, the road to Industry 4.0 is probably less one of massive digital transformation at huge initial cost than it is of making focused incremental changes linked to business value. As we approach 2019, Tom Lawton, Partner and Head of Manufacturing at BDO explains four topics manufacturers should focus their efforts
Before embarking on any Industry 4.0 developments, it is important for it to be underpinned by a clear strategy tailored to the business. We would suggest four key areas to think about:
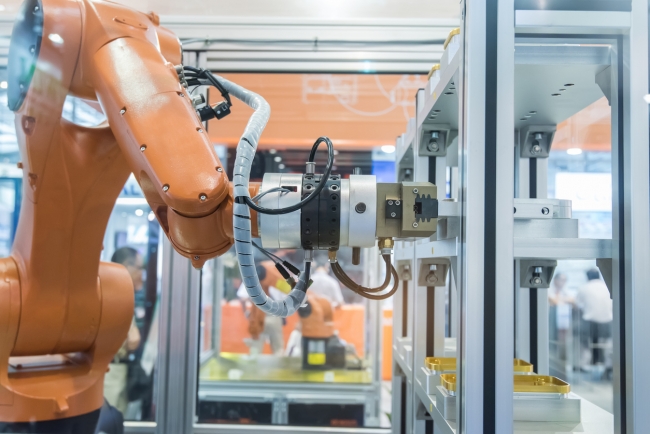
Prioritise Industry 4.0 investments based on where you see the biggest gaps and greatest opportunities / Picture: Getty/iStock
1 – Define your vision:
Once you know where you are today, you can define where you want to be tomorrow, next year and five years down the line.
Instead of focusing on specific features or tools, define your vision and set KPIs based on value to the business. The end goal of Industry 4.0 is about creating value from your data and processes. Prioritise Industry 4.0 investments based on where you see the biggest gaps and greatest opportunities.
The best enterprise technology innovations are those that are developed to solve existing customer and supplier challenges or provide your business with a competitive advantage to better serve them.
2 – Set up your pilot:
Innovation in small pilots enables faster decision making and implementation.
Fail to act quickly, and you fall behind; act too fast, and you risk messing up. Failure is a necessary part of the innovation process. But to make failure profitable, you not only need to fail fast, you need to fail smart. For most mid-sized manufacturers, that means dreaming big but starting small and then scaling up what works fast.
That’s where the three I’s of innovation come in. Iterative, incremental innovation (‘incrovation’) in small pilots enables faster decision-making and implementation, as well as the ability to adapt or change course at any point. The goal is to learn quickly and apply those learnings to the next experiment and/or scale the solution.
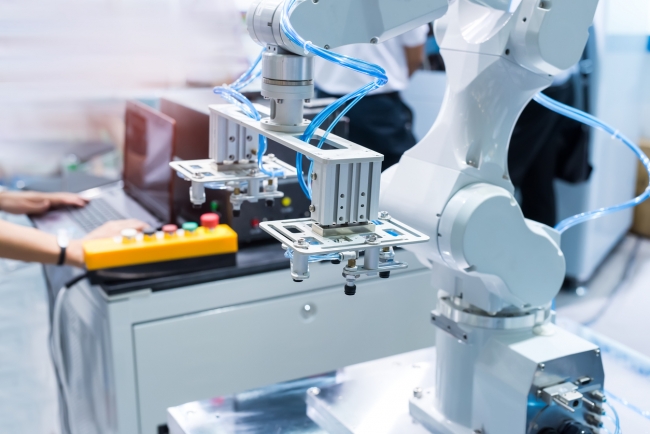
Training for the age of Industry 4.0 is going to be one of the key factors in the success of UK manufacturing / Picture: Getty/iStock
3 – Engage external stakeholders:
Industry 4.0 will likely create ripple effects across the value chain and require external process and technology changes.
Even if total value chain integration is a faraway goal, you will still need to think about external interoperability and processes for collaboration. Sharing sensitive data to an external network is easier said than done. Doing so requires a fundamental shift in relationships between suppliers and customers, and raises new questions about data privacy and information security.
Collaborative planning with key customers and suppliers early on in your Industry 4.0 journey will help accelerate implementation and lay the groundwork for secure co-creation of value. And it will also tell your customers and suppliers that you are engaged in moving positively towards digital transformation. This will be an increasingly important requirement for multi-national OEMs.
4 – Prepare your people:
Too often, organisations embark on a digital initiative but forget about the human element.
Even as processes become automated and AI might start to take over some data-driven decision-making, change still needs to start with people. You need your employees to understand why they need to leave the status quo behind, believe in the strategic vision and feel engaged in the process. Most importantly, they need to understand what’s expected of them and have the resources, training and development to get to the new destination. Training for the age of Industry 4.0 is going to be one of the key factors in the success of your company – and indeed UK manufacturing generally.