4 minute read • published in partnership with Atlas Copco
Insight: Covid lessons learned by a compressor service provider
Back in March 2020 few would have thought that Covid would have impacted business and lives for over a year. While there is no doubt that it has been both tragic and disruptive, within the compressor industry there have been continual efforts to find any positive trends among compressor users within manufacturing enterprises. As a result, valuable lessons have been learned on how to establish and handle the best approach during this crisis. Paul Clark and Brian Barnes from Atlas Copco share some of these solutions that have been learned.
For a start, working within the limitations of the two-metre social distancing rule does not mean that compressor equipment cannot be serviced on-site by suppliers’ personnel. For the majority of responsible compressor systems suppliers, safety in the workplace remains the highest priority in supporting customers during COVID-19.
Where there is a well-established Health & Safety culture, service organisations have been able to respond rapidly to the crisis by adding extra safety practices and risk assessment processes, enabling them to keep customers and their employees safe. In general, those suppliers complying fully with all government and HSE health and safety requirements have not experienced any problems with their service engineers being allowed on site.
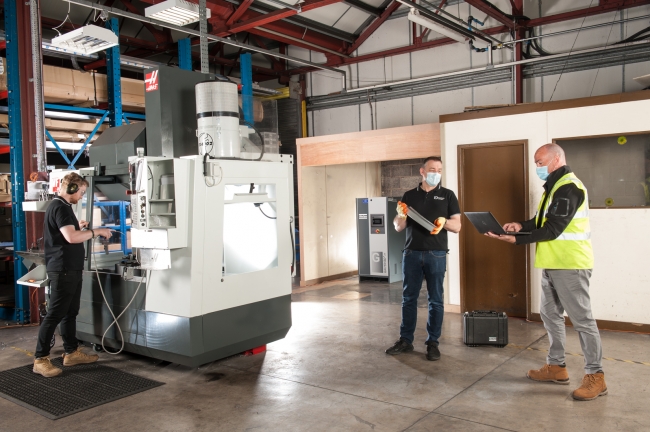
Picture: Atlas Copco
Apart from highlighting safety issues, the economic impact of the pandemic has meant that energy savings became even more of a priority than they were before the lockdown measures took effect. With the initial uncertainty and restrictions, businesses looked urgently for ways to reduce their production costs.
As a result, many compressor users decided that lockdown was a good time to review the performance and energy efficiency of their compressed air system. In particular, that meant tracking down and fixing any leaks causing a pressure-drop that could increase energy consumption.
They found the best way to do that was to book a leak detection test which employs state-of-the-art acoustic leak detection equipment. The procedure can be carried out without interrupting plant operation, reaching system areas that are hard to access, and locating all air leaks within a compressed air network. By locating, logging, quantifying, and costing air leaks, plant operators were able to prioritise the remedial work needed to improve performance and help reduce their energy costs.
Maintaining peak performance at all times has remained an equally essential requirement. During the early Covid period, it was evident that an increased number of compressor users moved away from ad hoc or in-house equipment servicing and opted for supplier service contracts that included connectivity solutions offering remote data monitoring options.
Their decisions made sense in two ways: a service plan that offers stability and optimum uptime, with all costs included in the proposal, takes away any concerns about the health and status of a compressed air system. Without these diversions, customers can then focus on what they do best, continue with their prime production activities. With the benefit of connectivity, they are able to monitor the operation and status of their compressor installation without even being on-site.
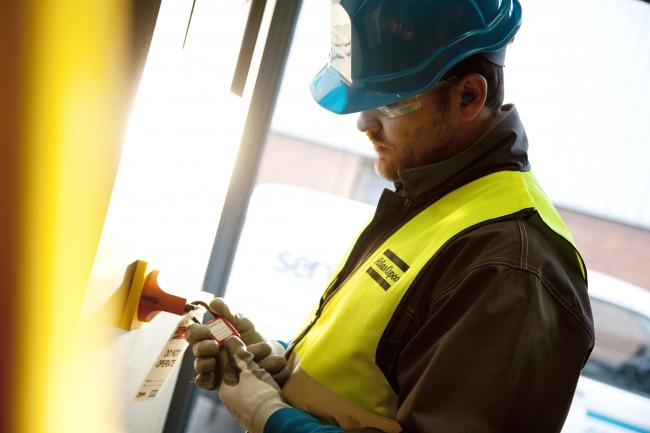
Picture: Atlas Copco
Whether under pandemic restrictions or in normal circumstances, the right calibre of well-trained and experienced service experts are called in to perform maintenance operations that optimise the availability of customers’ equipment. It is their job to spot and fix potential problems early, prevent efficiency loss and breakdowns. Part of that function is to maintain close liaison with customers on any equipment issues that arise, and a little technical advice goes a long way.
The Covid crisis meant that many manufacturers needed to shut down their compressors due to reduced or halted production and then restart them once it was possible to resume core activities. But it was vital that they needed to take heed of potential problems: where this procedure was not carried out correctly, some were faced with condensation issues in the air element or even experienced mechanical seizures.
So, for any users now ready to ramp up production, it is recommended that they first obtain advice on restarting compressors and reconnecting them to a control system safely. Then, if any of these checks highlight a cause for concern, to contact their supplier’s service operation for advice or assistance before attempting the restarting procedure.
Finally, in these challenging times compressor sales and service organisations found it was not only the pandemic that they had to contend with − but they also had to survive the complexities of Brexit too. Service teams had to make sure compressor customers were not affected by all the extra Brexit admin and paperwork, although it may have caused logistics teams some headaches. Well-prepared suppliers were still able to deliver parts and products to customer sites as usual, without passing on any additional cost or import duties.
The other good news is that despite Covid, economic trends are showing that the UK manufacturing sector is now experiencing its steepest pace of expansion for many years. As the UK finally eases out of lockdown, leading compressor sales and service teams are at full capacity and standing by ready to support the production industry.