4 minute read
Insight: Creating value in UK manufacturing from digitalisation projects
Ahead of the Subcon Show and The Engineer Expo, taking place 4th to 6th June, we caught up with Dr. Lina Huertas, Chief Technologist at The Manufacturing Technology Centre to discuss digitalisation and the insight she will be sharing at this year’s event.
In her current role, Dr. Lina Huertas focuses on driving the creation of value in the UK through the digitalisation of UK industry. This includes shaping the UK national strategy and policy, leading the relevant activities at High Value Manufacturing Catapult and running the MTC corporate strategy on Digital Manufacturing.
In the past three years, she has formed and led different engineering and technology teams that offer unique capabilities to develop and mature technological solutions for the UK manufacturing sector. Her experience includes a PhD in the application of simulation and informatics solutions to support manufacturing, and 12 years’ experience delivering industrial projects that generated business benefits on the back of digital technologies. Lina is a Fellow of the IMechE and has a first class honours degree and a master’s degree in Mechanical Engineering.

The MTC supports manufacturers of all sizes to embrace Industry 4.0 and digital manufacturing projects / Picture: The MTC
Can you share an example of a manufacturer the MTC has helped embrace digitalisation and what did they achieve?
We are not at liberty to disclose company names, other than those in the public domain, such as Harris RCS. However, we have three main customer profiles.
The first one is OEMs who are more advanced in their journey. With them, we focus on the development of innovative technology solutions based on digital technologies. Some examples of projects we have delivered for industry include use of Factory Simulation solutions to design and specify new factories, use of novel physics simulation techniques to accelerate the development of additively manufacturing products, development of machine learning methods for inspection of manual assembly activities, customisation of Autonomous Factory Vehicles to facilitate flexible routing of product through a factory and implementation of mixed reality solutions for delivery and conformance checking of assembly instructions directly from PLM and MES systems.
The second audience is technology vendors. We work with technology vendors helping them develop and test new technologies that can enable the future of manufacturing. We have primarily worked with software and manufacturing equipment & tooling vendors in this area.
The third area are SMEs. SMEs are usually earlier in their journey than OEMs and the focus of our work with them is on raising awareness of the potential of Digital Manufacturing, helping them define a roadmap of implementation specific to their business characteristics and needs and finally, helping them implement this roadmap in “sprints” that deliver value. This is what we have done with Harris RSC. With other organisations, we have gone through similar journeys, but all starting from different places. While for some the first step is the visualisation of data, for others is the implementation of ERP-type platforms, the deployment of solutions to support manual tasks and for others is the accelerated development of a new product and the selection of a manufacturing process.
Harris RCS is a great example as they have real-time monitoring for all staff and increased productivity by 20%. It isn’t something that costs a lot to money. How did they begin their digital journey?
As well as becoming more efficient as a business by using some lean principles and practice, Harris RCS were able to explore digitalisation. The digital journey for Harris RCS began with an understanding of where the business currently is, against where it wants to be in the future. For them, the key step was extracting value out of data and using it to support day to day operations on the shop floor. Information for workers was achieved through digital dashboards enabling visibility of tasks and status of jobs.
You can find the Harris RCS case study here.
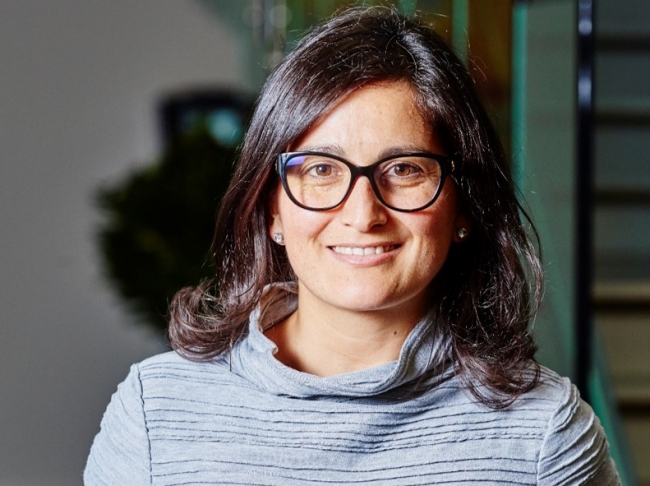
Dr Lina Huertas, Chief Technologist at The MTC / Picture: The MTC
Why do you think some have a misconception that Digital Manufacturing will cost millions of pounds when it doesn’t always necessarily have to be that costly? What are your thoughts on this?
Digital Manufacturing or Industry 4.0 has been traditionally driven by large providers who have provided multi-million-pound systems to OEMs in the past and have multimillion customisation and maintenance service contracts. This has created the perception that to do ‘Digital Manufacturing’ you have to invest millions in the implementation of traditional enterprise systems such as ERP, PLM and MES, not to mention new bolt-on capabilities, usually associated to AI. The reality is that it doesn’t have to be like that. Everyone should design their own journey to maximise the benefits based on their current foundations and their ambitions. We have numerous partners who are taking a more agile approach by doing smaller implementation steps that generate value quickly. By doing this, they are putting pressure on technology providers to provide modular solutions that can be implemented selectively in phases, unlocking value quicker and more efficiently. The most disruptive providers of digital technologies are changing their business models to suit these requirements and there are even examples of large traditional providers who have started to widen their SME customer base by providing their solutions on a pay per use service.
Lina will be speaking at the Subcon Show conference on 4th June.