5 minute read • published in partnership with Desoutter
Insight: Driving manufacturing efficiency and growth with strategic supplier collaboration
Manufacturers are gearing up for expansion with ambitious plans for new product development and increased capacity. Yet, challenging current conditions demand a savvy approach to capital investments, elevating the role of productivity-enhancing allies like never before. Desoutter Tools is one ally committed to making a difference.
Despite enduring another challenging year, the manufacturing sector ended 2023 on a positive note. Improved conditions, a more supportive policy environment and the UK’s rise to eighth in the global industrial economy rankings have sparked a sense of cautious optimism among companies and a renewed appetite for growth in 2024.
More than half of manufacturers* see opportunities in new products, with one in four venturing into new markets. A similar proportion views Net Zero as a significant opportunity for their businesses in the year ahead.
With companies eager to boost their output, most are planning to invest in new capital equipment within the next 12 to 24 months or are considering such investments. Notably, even though three in four recognise the transformative power of digital technologies for operational efficiency, fewer than half plan to invest in them over the next 12 months.
This is particularly surprising given that the majority of manufacturers who have previously adopted digital technologies say their past investment has paid off** and they are now better prepared to weather storms such as supply chain volatility and labour shortages.
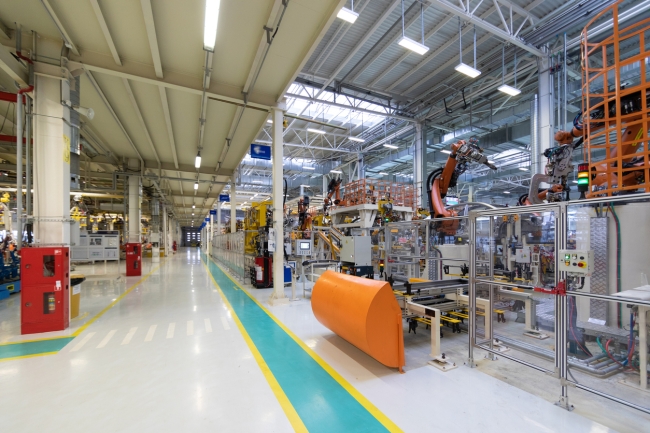
Manufacturers need a savvy approach to capital investments, elevating the role of productivity-enhancing allies like never before / Picture: Getty/iStock
Beyond keeping manufacturers agile and competitive, digitised and more efficient processes also deliver significant cost savings. Manufacturers report savings of up to 20% on their electricity and gas bills – particularly welcome given energy prices are cited as the biggest risk to growth*** for UK manufacturers in 2024.
Now more than ever, manufacturers need to understand what tools are available – whether digital or physical, if they apply to their specific processes, what the strategic business benefits could be and how best to integrate them.
“Industrial decision-makers are being much more proactive in grasping what tools and technologies are available and how they can help maximise productivity, efficiency and, ultimately, their investment,” says Mark Taylor, UK General Manager for Desoutter – a global leader in assembly solutions and process control.
“The companies we engage with have a sharp focus on automating processes, increasing efficiencies, fostering operational flexibility and striving to transform into the most sustainable organisation possible.”
Helping make your vision a reality
Desoutter has undergone its own transformative journey, moving away from a features and benefits sales approach to offering a more knowledge-led, consultative service. This strategic shift is fuelled by a commitment to understanding customers’ goals, pinpointing bottlenecks hindering their progress, and empowering companies to be the best at what they do.
The transformation has been a hit with industry, says CPI Business Line Manager, Stephen Draper-Garcia. According to him, these changes have elevated Desoutter up the value chain, resulting in a shift in how companies engage with Desoutter.
“People know Desoutter for our fastening tools, and historically, they would engage us at the end of their factory extension or new cell build. But if you don’t know what tooling is available and its true capability, how can you ensure your assembly process is as efficient as it can be?
“Now, we are supporting our customers far earlier. To the extent that for some partners, we’ve worked alongside their R&D team to ensure that their new product is designed in such a way to enable efficient manufacturing. Likewise, we’re collaborating with line builders to ensure the right tooling is proposed as early as possible to future-proof their decisions.”
The opening of a dedicated iNNOVATION CENTRE in Cheshire marked a pivotal milestone in the evolution of Desoutter, says Mark. This cutting-edge facility serves as a sandbox for companies to fully immerse themselves in what’s possible through the Desoutter ECOSYSTEM.
In addition to demonstrating current products, it allows Desoutter to showcase its product roadmap and unveil upcoming innovations.
“Visitors often arrive with an idea of what they need to address, a recurring issue or improve worker efficiency, but the iNNOVATION CENTRE provides an opportunity to really get under the skin of their challenges. Here, they can see our tools and solutions in action and how they can be configured, combined and connected,” he says.
“By taking time to step back and critically evaluate their processes, guided by our experts, companies arrive at the best solution for their current need, with consideration about their future needs.”
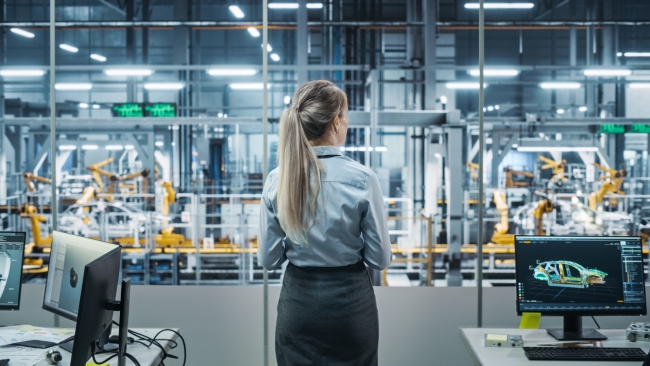
Desoutter takes a collaborative approach with partners to help maximise productivity and enhance growth / Picture: Getty/iStock
Expert help to futureproof your investment
The iNNOVATION CENTRE also serves as a hub for Desoutter to host in-depth training workshops, reflecting their philosophy that solutions should be ‘owned’ by customers. As well as being taught how to operate the equipment, users are encouraged to explore ways to maximise its potential through process and data review.
Additionally, Desoutter offers the option of dedicated on-site experts to provide guidance and support, particularly beneficial during the initial phases of integrating a new solution.
Depending on requirements, these experts can work with a customer’s engineering team for a set amount of time every week to help maintain project momentum or establish a permanent on-site presence focused on continuous process improvement.
Desoutter’s technologies are built on a common global foundation and trusted by leading brands such as Airbus, Ford, Saab, Toyota and Honda.
“Our commitment to continuous improvement and development ensures that our offerings remain at the forefront of innovation,” says Stephen. “At the same time, advancements in smart tooling, process control software and real-time data analytics are known knowns, with proven benefits, integration strategies and payback periods.
“There’s no reason not to get on this journey. Indeed, the cost of inaction could have severe consequences in the long-term.”
Mark agrees, adding; “UK manufacturers increasingly recognise the huge threat to their competitiveness from industrial giants like the US, India and China. The world of manufacturing is evolving at an alarming pace. The emergence of BYD in China, with plans to establish a production plant in Europe, shows the dynamic shifts happening on a global scale.
“Agility, flexibility and efficiency are paramount. Achieving these goals relies on adopting new processes and technologies, coupled with optimising your existing equipment. If not, UK manufacturers run the risk of lagging behind.”