4 minute read • published in partnership with K3 Syspro
Insight: Four ways technology can weather the Brexit storm in electronics manufacturing
The electronics sector is an integral part of British manufacturing and also one of the most diverse, but Brexit has helped create the perfect storm of challenges. K3 Syspro looks at the technology available to electronics manufacturers to help them respond rapidly to market changes and remain competitive.
When you look at the contribution of electronics manufacturers to modern living, it’s difficult to believe that the sector is beginning to contract. Despite widespread adoption of smart devices, modern technology and electronic solutions, Make UK’s recent sector bulletin reveals slower growth for electronics manufacturing throughout the past 12 months when compared to 2017.
The reason? Few vertical manufacturing sectors have been as heavily affected by Brexit uncertainty as electronics. It’s rare for many components such as resistors and integrated circuits to be manufactured in the UK and with a fluctuating exchange rate, such products have become more expensive and difficult to import. For a market so reliant on overseas goods, the flow of logistics and entire supply chains have been significantly disrupted, resulting in challenging production environments. Furthermore, with Brexit continuing to be delayed, the future remains uncertain for this pillar of industry.
However, there is hope. When you look at the DNA of the UK’s electronics industry, 93.2% of businesses have a staff level below 50 employees*. Indeed, only 1% has more than 250 members of staff. These small but highly agile SMEs are typically less risk-averse than larger corporations and well positioned to maximise some of the opportunities presented by digital transformation.
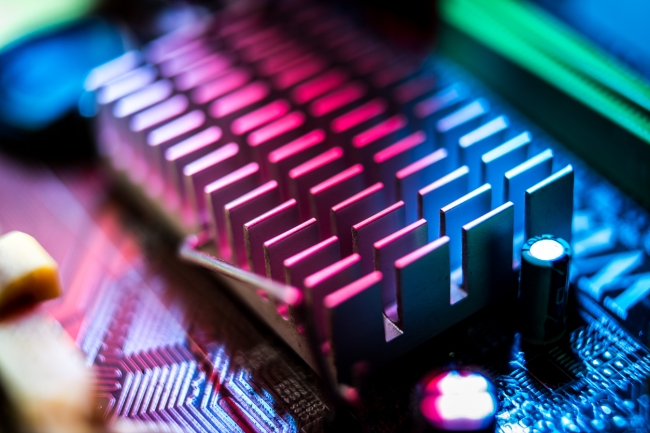
Brexit has helped create the perfect storm of challenges for the electronics sector, but technology can a key roll in helping manufacturers respond rapidly to market changes and remain competitive / Picture: Getty/iStock
The right technology can help electronics manufacturers find a way through some of the complex challenges they are facing. Not only do manufacturers need to mitigate the risks of uncertain export conditions, but they also continue to face ever-shorter product lifecycles, shifting customer preferences and fierce global competition. By embracing a flexible and adaptable Enterprise Resource Planning (ERP) such as SYSPRO at the heart of their business, electronics manufacturers can respond rapidly to market changes and remain competitive. Here’s how…
1 – Staying on top of changing circumstances
Highly volatile material costs and fluctuating prices make operating a lean and highly-efficient business model an enormous challenge. To survive and thrive, electronics manufacturers need to be able to operate different business models simultaneously, moving between Kanban systems to Materials Requirement Planning and Materials Execution Systems, to ensure effective execution of manufacturing operations and improved production output. Dashboards can be built within SYSPRO to display all this information on one screen at a glance, and the integration framework upon which SYSPRO ERP is built makes it possible to operate an ever-evolving and adaptable business solution, rather than a one-size-fits-all system.
2 – Connecting the supply chain
Working with so many suppliers across different areas of business is also a challenge, particularly when components can quickly become unavailable, lead times can change frequently, and parts are sourced from a large list of different vendors. As a result, keeping on top of inventory is essential to avoiding excess order intakes and duplicated material purchasing. An ERP solution that promotes intelligent procurement practices based on real-time demand and existing inventory levels can help deliver long-term cost savings and leaner inventory models. When combining stock management with forecasting technology, electronics manufacturers can ensure that enough inventory is held at all times and material imports are not being held up on borders or being unexpectedly delayed.
3 – Visibility over return items
A real challenge for electronics manufacturing businesses is staying on top of return merchandise authorisation, a key condition of most service agreements. Returns can be costly and inconvenient for customers and therefore, manufacturers are often contracted to quickly diagnose and correct any issues with products themselves. A fully integrated ERP solution provides manufacturers with the means to easily keep track of returned goods and ensure items do not become lost on the factory floor, keeping to agreements at all times.
4 – Seamless backflushing
Several electronics manufacturers will already be operating Bill of Material (BOM) backflushing in order to benefit from a just-in-time production model. Backflushing means that whenever a part is made, the stock of the components on the part’s bill of material is reduced by the quantity on the bill of material. An effective ERP solution will offer backflush functionality to support this process and enable manufacturers to clearly define what type of raw materials are required to be backflushed and what may not, at every BOM line.
With demand for electronic devices remaining high and uncertainty over Brexit continuing for the foreseeable future, electronics manufacturers are not yet out of the doldrums. However, the old adage fail to prepare, prepare to fail often rings true and by preparing a flexible, integrated and effective enterprise-wide solution, electronics manufacturers can weather any storm that comes their way.