3 minute read • published in partnership with ATS
Insight: How advanced planning & scheduling systems help improve factory operations
There are several reasons why manufacturing facilities, particularly injection moulding factories, should invest in Advanced Planning & Scheduling (APS) systems to improve their on-time-in-full deliveries in the face of supply chain issues. ATS looks at what manufacturers should focus on as part of their transformation journey.
Increased Visibility and Control: An APS system provides greater visibility and control over the entire production process, from raw materials to finished products. By analysing historical data and real-time information, an APS system can help identify potential bottlenecks and other issues that could affect delivery times. This allows manufacturers to make better decisions and proactively adjust production schedules to avoid delays.
Improved Efficiency: An APS system can help improve efficiency by optimizing production schedules, reducing waste, and minimizing downtime. This not only helps to improve delivery times but also helps to reduce costs and improve overall profitability.
Better Demand Planning: An APS system can help manufacturers better understand and forecast demand, allowing them to adjust production schedules accordingly. This helps to ensure that the right products are produced at the right time, reducing the risk of overproduction or underproduction.
Faster Response Times: In the face of supply chain disruptions, an APS system can help manufacturers respond quickly and effectively. By providing real-time data and analysis, manufacturers can quickly identify and respond to issues such as supplier delays, production issues, or transportation disruptions.
Improved Customer Satisfaction: Finally, an APS system can help improve customer satisfaction by ensuring on-time-in-full deliveries. This helps to build trust and loyalty with customers, leading to repeat business and positive word-of-mouth recommendations.
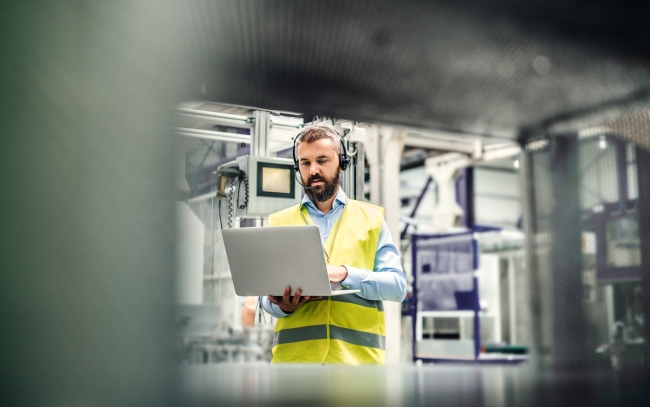
An APS system provides greater visibility and control over the entire production process / Picture: Getty/iStock
Overall, investing in an APS system can help manufacturing facilities, particularly injection moulding factories, improve their supply chain resilience, reduce lead times, and improve on-time-in-full deliveries. This can ultimately lead to improved profitability, customer satisfaction, and competitive advantage.
In Advanced Planning & Scheduling (APS), secondary constraints refer to the non-production constraints that can impact the manufacturing process, such as labour, machine availability, and material availability. Incorporating secondary constraints into the APS system can offer several benefits, including:
Improved Production Planning: Incorporating secondary constraints can help ensure that the production schedule is realistic and achievable, considering all the factors that can impact the process. This helps to prevent overloading of resources, which can cause delays, reduce efficiency, and increase costs.
Better Resource Utilization: By considering secondary constraints in the production planning process, an APS system can help optimize resource utilization, ensuring that labour, machines, and materials are used effectively. This can help reduce waste, minimize downtime, and increase overall productivity.
Enhanced Flexibility: An APS system that incorporates secondary constraints can also provide greater flexibility in the production process. By considering the availability of resources, the system can adjust production schedules and allocate resources as needed to address unexpected changes or issues that arise during production.
Increased Cost Savings: By optimizing resource utilization and reducing waste, incorporating secondary constraints into the APS system can help reduce costs associated with labour, machine usage, and materials. This can ultimately lead to significant cost savings for the manufacturing facility.
Improved Customer Satisfaction: Incorporating secondary constraints into the APS system can also help improve on-time-in-full deliveries, which can increase customer satisfaction and build loyalty. By ensuring that the right products are delivered at the right time, manufacturers can build a reputation for reliability and quality, which can lead to repeat business and positive word-of-mouth recommendations.
In summary, incorporating secondary constraints into an APS system can offer several benefits for manufacturing facilities, including improved production planning, better resource utilization, enhanced flexibility, cost savings, and improved customer satisfaction. By considering all the factors that can impact the manufacturing process, an APS system can help manufacturers achieve optimal efficiency, productivity, and profitability.