4 minute read • published in partnership with Forterro
Insight: How mid-market manufacturers can use ERP to drive sustained growth
It’s an exciting time to be a mid-market manufacturer in the UK. There’s more opportunity than in recent years for them to trade internationally, optimism that the UK is set for a period of economic stability and the chance to use technologies such as AI to really streamline and make the business more agile and efficient. Mikael Brodin from Forterro explores how technology can help drive sustained growth.
The need for growth is constant. This is of the highest importance for virtually any business, but for midmarket manufacturers, especially so. Escalating production costs and increased competition mean that the status quo is not an option, and not growing can threaten the business’s existence.
But what’s the best way to approach growth? There’s no silver bullet, but there are elements that manufacturers can put in place to give themselves the best chance, and selecting the right Enterprise Resource Planning (ERP) software is one of the most significant.
At Forterro, we work primarily with midmarket manufacturers, and this is what we’ve learnt from decades of working in that market.
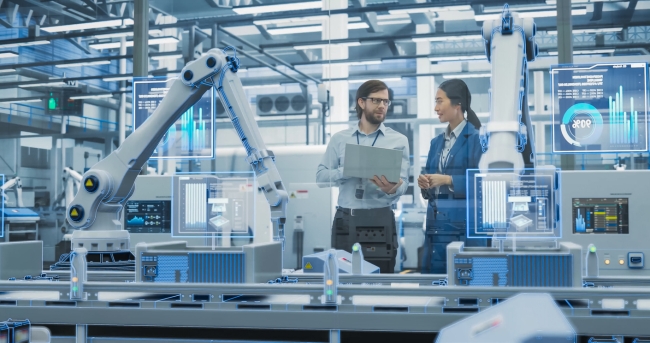
Picture: Getty/iStock
Make digital transformation a priority
Because many midmarket manufacturers began life as factories, digital transformation can feel daunting to some. But switching to more digital operations can be transformative. It makes the business leaner and more efficient, and automating manual processes frees up staff time to be better spent elsewhere. It also eliminates the potential for human error to impact the business negatively.
ERP can play a significant part in digital transformation, which is vital to business growth. However, choosing an ERP system tailored to your industry and meets your specific operational needs is imperative.
There is less value to be found in a general, one-size-fits-all option when compared to a platform that has been iteratively improved over decades, all by taking onboard feedback from customers from your sector. In manufacturing, for example, specialised software can focus on the unique challenges of managing the stock journey, amongst many other operational aspects.
It’s vital to avoid running before you can walk with this. If your business has been mostly analogue to this point, then a phased approach to ERP implementation is best. This allows gradual adaptation and integration, minimising disruption and allowing users to become accustomed to it.
Furthermore, a collaborative relationship with your ERP provider ensures continuous improvement and system adaptation to meet evolving business needs.
The importance of change management
To get the most from an ERP system, it must be integrated into your day-to-day operations and workflows. It must also connect with other technologies used in the business. This requires thorough planning and understanding of the business needs, while internal development capabilities can help customise the system without incurring costs for external services.
From here, the focus should turn to change management. People can be nervous about new technologies, and ERP is no exception. Change management is, therefore, crucial for successful ERP implementation. Engaging with employees, reassuring them and addressing their concerns helps gain their support and can pave the way for success.
Identifying and celebrating small wins early in the process can build momentum and demonstrate the new system’s benefits, especially if people had been initially sceptical.
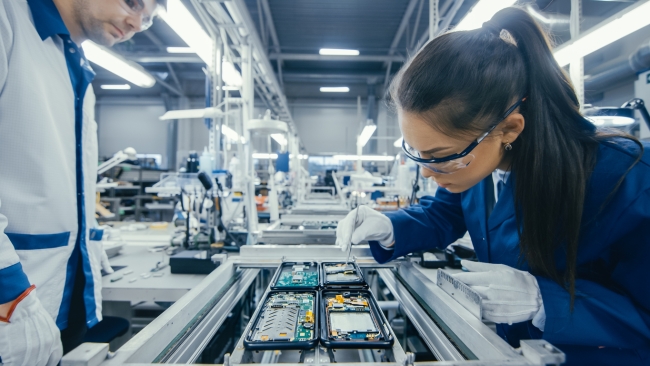
Picture: Getty/iStock
Smart and informed data-based decisions
Once your ERP system is in situ, data is one area in which it can have the greatest impact. Real-time data access and automated reporting provide crucial visibility into business operations, and mean adjustments can be made where required. Having detailed performance metrics helps identify and address issues promptly, preventing minor problems from becoming major setbacks.
It allows you to make smart and informed business decisions based on trends and themes in your data. Maintaining customer service levels is a good example.
As businesses grow, this can become challenging. An ERP system helps manage customer interactions and ensures consistent service quality. Tracking data makes it much easier to see and address service issues, preventing customer dissatisfaction and potential churn if those poor service levels continue.
ERP – agile and evolving
An ERP system should be flexible and agile enough to adapt to changing business requirements and market conditions. Continuous development and improvement of the ERP system ensure it remains relevant and beneficial as the business evolves. Furthermore, implementing a fully scalable ERP system ensures the business can grow without being constrained by outdated processes.
Growth is a primary objective for most midmarket manufacturers, and ERP can help facilitate that. It can automate many areas of your operations, help maintain and improve customer service levels and make it easy to get greater value from the data you hold.
Companies that implement and use ERP solutions can drive growth, improve efficiency, and maintain a competitive edge.