8 minute read • published in partnership with Evocon
Insight: How to set OEE targets that work
As Peter Drucker famously wrote, “what gets measured, gets managed”. Furthermore, to manage and begin improving manufacturing performance, a baseline is needed as well as an OEE target. Without these tools, it may not be entirely clear when, where, and why improvements occur. Moreover, a manufacturer may not fully understand the relative difficulty of its goals or the work required to reach them. Evocon explores how to set OEE targets that work.
Establishing baselines, OEE performance goals, and benchmarking are all essential aspects of deploying OEE successfully. It’s about coming up with clear, well-defined, and attainable goals that are driven by data and aligned with strategic objectives. But where should you start, and what are the steps you need to follow? To maximise the value of an OEE implementation, your company should seek to understand the methods for setting OEE targets.
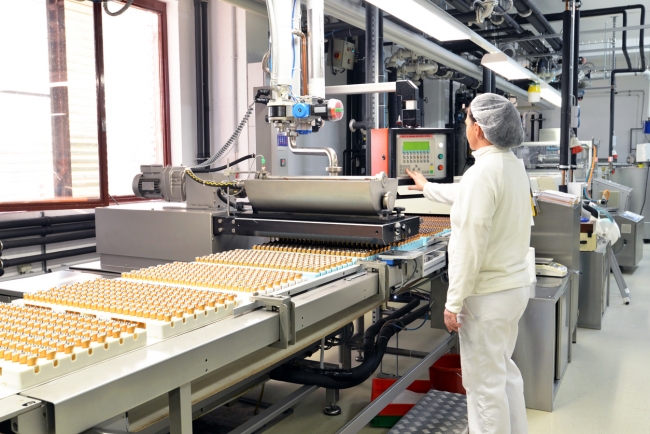
Successful OEE performance needs clear, well-defined, and attainable goals that are driven by data and aligned with strategic objectives / Picture: Getty/iStock
Paying close attention to the process is essential because poor goals are problematic. When the target is too difficult, it can demoralise teams responsible for meeting these unrealistic goals. Or, if the target is too easy, it makes the attainment of the goal meaningless. Here at Evocon, we believe that the best performance targets are clear, challenging and attainable.
When goals have these characteristics, they enjoy widespread support, are easy to comprehend and garner more participation by your workforce. Further, they tend to lead to higher levels of achievement, and the rate at which improvements occur is far faster.
Collect and Analyse Current State Performance Data.
Each manufacturing company is unique but to set OEE targets, the first step is the same: begin collecting live OEE data.
However, it is essential to realise that this is only a rule of thumb. You will need to use your best judgement for your unique situation.
The time required can vary depending on an organisation’s exposure to OEE, among other things. For example, those new to OEE should expect the implementation learning curve to temporarily lower OEE scores. In that case, you might consider spending more time on this step. This allows you to ensure the data is free from gaps in reporting and significant performance outliers.
The data you are collecting requires stability and accuracy to form a meaningful OEE baseline. Develop your baseline by analysing the current state data you collected on availability, performance, and quality. These are, as you may recall, the 3 major building blocks of the OEE score.
Focusing on the three main components of OEE.
By analysing each element of your organisation’s OEE score, you can begin to determine the reasons behind the losses in each category. This knowledge will give you some indication of the improvement opportunity that exists and what results can realistically be achieved. Moreover, you will begin to understand the interplay between the three components.
As an example, even if availability, performance, and quality perform at 90%, the OEE score would still be 73%. This indicates that 27% of the scheduled work time is non-productive due to different losses.
For instance, acceptance of poor-quality levels can increase availability. But would this be wise? As it turns out, no it wouldn’t. Defects lower quality, and poor quality increases the cost. Thus, earnings will not improve.
Baseline data is the starting point you will use to measure and compare future performance. So, it is worth your time to ensure it is as accurate as possible. Considering the interlinkage between these three components, what methods can be utilised to set the right OEE target?
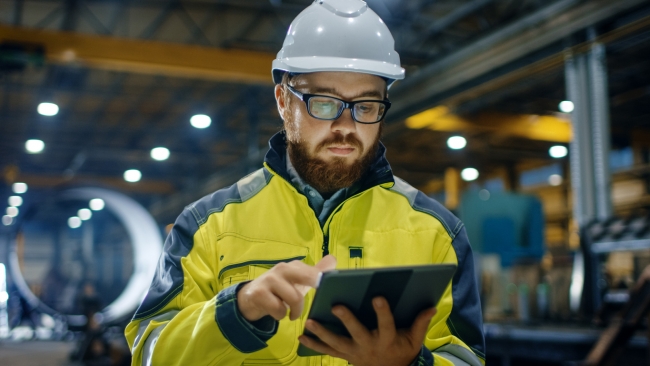
An OEE target should be challenging and involve the whole team. At the same time, it needs to be achievable, realistic, and clear / Picture: Getty/iStock
Methods for Setting OEE Targets
As is the case with most performance measurement goals, there are many methods for setting your target for OEE. But there is no silver bullet that is best to use in all cases. In fact, if you roll a dice to set a goal, and the target motivates you to improve gains, it would be difficult to say the method was wrong. Be that as it may, we will briefly discuss two common methods popular among Evocon clients.
1 – Set your daily OEE target to equal the best OEE score recorded in your baseline data.
This method is straightforward to put into practice. Let’s refer to it as “the collective best” (TCB) method. TCB only requires you to simply review your baseline data and identify the highest OEE score. This number now becomes your OEE target.
Machine operators and managers are accountable for improving the average daily performance to this point. When you reach this milestone, rewards may be in order before you begin the process to set the next target.
The idea here is as simple as it is powerful: a relentless journey to continually improve by cycling from setting a new target, working to reach it, and then, repeating the process. In theory, at least, this cycle could continue without end. Indeed, this is the mantra of continuous improvement – the goal is to take the journey, not to reach a destination.
2 – Set your daily OEE target to allow a small number of daily “misses”.
This method is about setting a target that the plant can “pass” on most days. Or put another way, to make sure that you cannot hit the target all the time.
Though counter-intuitive, your target with this method will allow a small number of daily OEE “misses” each month. Let’s call this method “aiming for small misses” (AFSM).
It may help to think of AFSM as the opposite of the TCB. With TCB, you are setting a target that will require performance improvement before the plant will be able to reach the goal each day. With AFSM, you are setting a target that the plant will be able to achieve on most days, but not every day.
The point of this method is about turning your attention to times that your performance is lowest. To further illustrate, let’s compare the performance gap that each method will focus on.
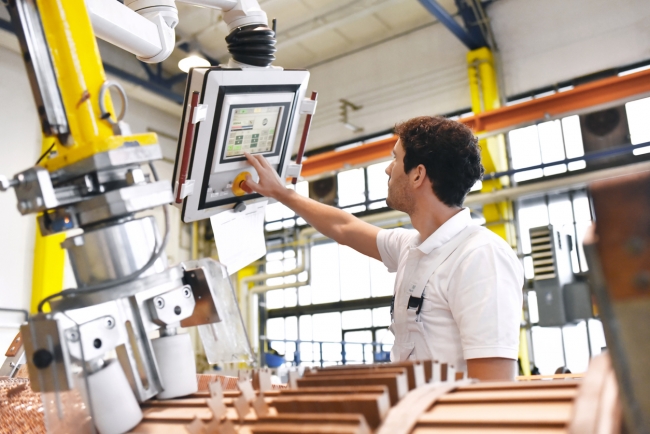
OEE targets should be ‘SMART’ – specific, measurable, attainable, realistic, and time-bound / Picture: Getty/iStock
Encourage team ownership of establishing objectives.
Regardless of the method, you take to establish your OEE goals, there are several other points to keep in mind. First among them is that OEE targets should begin and end with your team. The aim is for them to take ownership for establishing the performance target as this will ensure the goal is achievable.
Discussing the current situation with the team, analysing the pros and cons, and exchanging ideas on performance targets creates a sense of ownership and pride in the results. During this evaluation process, even opposition can lead to the team gaining different perspectives and improving communication. We encourage this healthy debate as it furthers engagement and improves the overall quality of targets.
Keep your goals realistic and attainable when you set an OEE target.
The OEE target should be challenging and involve the whole team. At the same time, it needs to be achievable, realistic, and clear.
Targets should only cover aspects that the operators can affect. The more you educate your operators about the importance of setting goals and how they benefit from it, the more likely they are to collaborate in this process and embrace the goals.
Take action to shape the internal culture.
Once you clearly define your production goals, you need to take steps to shape the internal culture within your organisation. You need everyone in the company, from the line operator to the CEO, to understand the targets and to monitor the progress. Success comes to teams that easily collaborate cross-functionally and then work together towards the shared goal they defined.
OEE alone is insufficient to make a complete analysis that supports all production decisions. However, it can be useful to motivate teams by incorporating it into your performance management processes. The measure is objective and is well suited to serve the basis for bonus decisions.
Make your OEE goals SMART.
Goal setting is a continuous process that requires updates according to the results. The same applies to the OEE target setting process. Therefore, it is crucial to have specific criteria, strategies, and principles as a framework when establishing useful targets. This not only makes the process smoother but also provides the production team with the motivation they need.
In general, the well-known acronym for goal setting, S.M.A.R.T, will benefit OEE goals. That is to say, your OEE targets should be specific, measurable, attainable, realistic, and time-bound.
How to set OEE targets on a larger scale.
What about setting OEE targets for large multinational companies like we find in the Fortune 500? Do the larger scale and increased complexity change the way we set OEE targets? The short answer is no, but there are other considerations to keep in mind.
As the scale and complexity of operations increase, so do opportunities to benefit from the synergies of utilizing one system across the enterprise. For this reason, we recommend that management plan OEE deployment across all operations and avoid each plant developing a custom solution.
One solution for all locations allows for data standardisation. Data standardisation can undoubtedly be beneficial in any organisation; but for large, multi-plant operators, it is essential. Standardised OEE systems, methods, processes, and data all come together to enhance internal communication and the sharing of best practices and benchmarking.