4 minute read • published in partnership with Atlas Copco
Insight: Keeping air compressors running smoothly and efficiently
Air compressors supply industrial plants with compressed air for use in pneumatic systems. These could include everything from air motors and valves to diverters in materials handling systems. Many emergency shutoff valves in the oil and gas industry and other facilities also operate using pneumatics. Andy Lill from Atlas Copco looks at how the compressed air system, therefore, plays a vital role in the production and safety of a facility.
Given their role on an industrial site, it is important to keep air compressors and associated equipment running smoothly and efficiently. Removing condensate is one key factor in achieving this goal.
Where does the condensate come from?
All air contains moisture, and the higher the ambient temperature and humidity, the more moisture it will contain. Inlet air conditions for a compressor therefore have a direct impact on the amount of water in the compressor discharge.
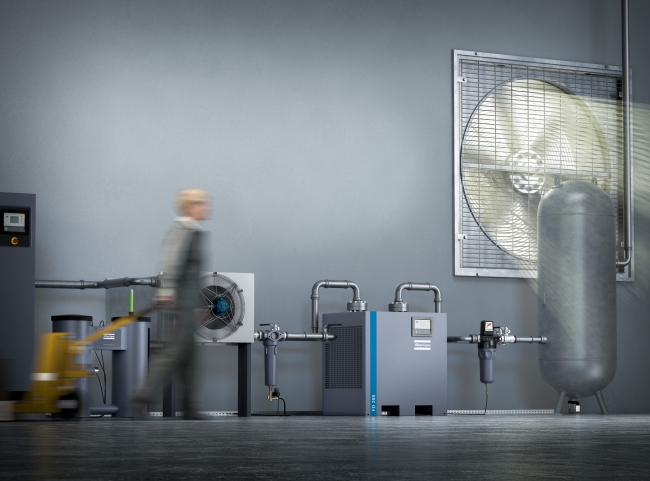
Given their role on an industrial site, it is important to keep air compressors and associated equipment running smoothly and efficiently / Picture: Atlas Copco
Compressor outlet conditions also impact on the amount of water present in the compressed air. The higher the outlet pressure, the less moisture the air can contain causing some water to condense out as liquid. For example, a 100-kW compressor, drawing in ambient air at 20°C and 60% relative humidity, will produce approximately 85 litres of water during an eight-hour shift. This can be compared with a 55-kW rotary screw air compressor, operating at 24°C ambient temperature with 75% relative humidity, which will produce 93 litres of water in the same time.
An important measurement in terms of water condensate in compressed air is the Pressure Dew Point (PDP). This is the temperature at which the air is saturated with water and will begin condensing moisture into the liquid state.
Why must condensate be removed?
The build-up of condensate in compressed air systems causes damage to equipment and potential process problems. Some typical symptoms of this are as follows:
• Condensate washes out lubricating oil increasing the wear on equipment and resulting in higher maintenance costs and more equipment downtime.
• Moisture leads to corrosion in piping and equipment. Rust particles get stuck in air tubing or orifices causing blockages and affecting their operation.
• Condensate in instrument air systems affects air pressure and therefore instrument reliability. Incorrect signals can mislead process automation systems leading to product quality issues, inefficiencies or even unplanned shutdowns.
• In the specialised case of painting, wet compressed air negatively impacts the quality of paint finish. This may result in rework.
The bottom line is that condensate in compressed air systems is bad news for equipment reliability, product quality and costs.
What contaminants may condensate contain?
The problem with condensate in the compressed air system is that you cannot dispose of it directly to a drain. It contains contaminants that are harmful to the environment and regulated by the authorities.
Small amounts of lubricating oil migrate into the discharge of an air compressor. This oil will accumulate in the condensate and exit the air system through condensate drains. For this reason, condensate from compressed air systems must be tightly controlled and treated before disposal.
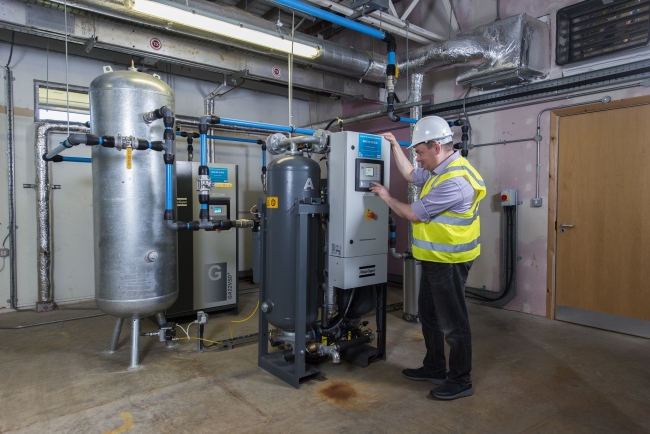
Condensate has the potential to cause major issues in a facility through corrosion, equipment damage and false instrumentation readings / Picture: Atlas Copco
Regulations governing condensate disposal
The Environment Agency in the UK is responsible for issuing environmental permits for discharging liquid effluent or wastewater. These permits specify limits for contaminants like oil depending on the volume of wastewater discharged from a facility.
The agency also monitors compliance with your permit conditions. They can conduct assessments and inspections, which result in a Compliance Assessment Report. Sanctions for non-compliance include advice for improving environmental performance, enforcement notices and even suspension notices where the risk of pollution is high. You could also incur a fine of up to £20,000, and damage to your reputation as a responsible organisation.
How to dispose of compressor condensate safely
Firstly, you have to remove the condensate from the compressed air system itself. After coolers and water separators remove 80 to 90 % of water directly after the discharge of the compressor. The remaining water can be drained from the air receiver where it condenses due to the drop in temperature as the air enters the tank.
Condensate from every drain point must be collected and directed to an oil-water separator. Allowing this water to escape directly into sewers will result in oil content spikes and potential violation of your permit conditions. Oil water separators are easy to operate and ensure that wastewater leaving your facility remains within your permit conditions.
Conclusion
The build-up of condensate in a compressed air system is normal and is a direct function of compressing the air into a smaller volume leaving less space for water molecules. However, this condensate has the potential to cause major issues in your facility through corrosion, equipment damage and false instrumentation readings. In addition, the condensate may contain traces of oil which must be removed before the wastewater is discharged to a sewer.
Keeping control of these factors will improve your plant reliability and ensure compliance with environmental authorities.