3 minute read • published in partnership with KUKA
Insight: Robotics and automation – a measure of success
There is a misconception that we (manufacturers) don’t need to automate, a mindset that certainly exists in some of the UK’s more traditional manufacturing districts. We are now operating in an era that has turned manufacturing as we know it on its head and it’s time that tradition meets with innovation, as we continue to see a shift in production trends, that will best position the UK to compete.
More and more robotics and automation are featuring in upstream processing applications that might traditionally have been undertaken manually. The reasons? There are many. Though if we focus upon those considerations that a manufacturer must factor into a production facility, so that they might meet demand, address health and safety considerations, attain a consistent level of product quality expected by their customer and the consumer and remain competitive, there is a lot to consider.
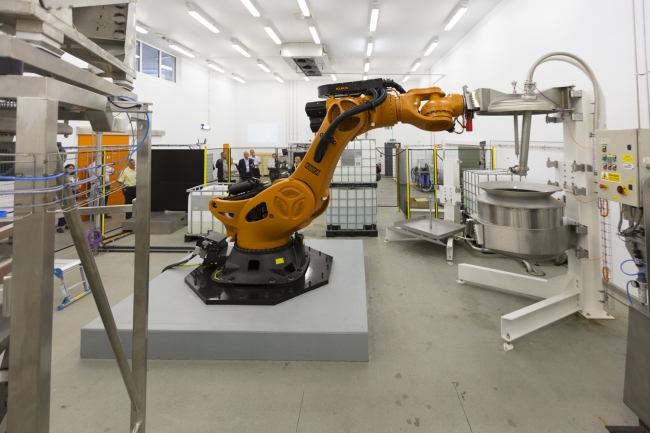
KUKA & OAL are hosting a webinar on 23rd March to explain how robotic applications are diversifying material handling and processing in the manufacturing sector / Picture: OAL/National Centre for Food Manufacturing
There exists a plethora of benefits that can be achieved through the adoption of robotics, some aligned with the aforementioned considerations, the question is how we factor that technology into an existing operational footprint. Is it easy to do?
The FMCG and food and beverage sectors are synonymous with materials handling functionalities, that include weighing, measuring and batch processing. All require a consistent level of accuracy and repeatability. The quality of this type of handling exercise is paramount to the integrity of the finished product. If anything were to go wrong, costly recalls, expensive periods of downtime, even operator health can be compromised, certainly so when those materials include powders and chemicals, both of which exist within production facilities that make bread, or personal care products such as shampoo and conditioner. Though these risks can all be mitigated, through robotic process automation.
As the skilled labour pool shrinks, and the cost of both training and retaining entry level personnel within such applications becomes increasingly challenging, manufacturers are recognising and benefitting from the advantages that automation affords; productivity gains, enhanced and consistent product quality, health and safety benefits and cost savings. That’s not to say for one moment that robots shall eventually attend all manual tasks within a production facility. Let the robots undertake the tedious, unergonomic tasks commonly associated with work-related illness and injury, whilst those operatives are removed from those unergonomic working conditions and upskilled in other areas of the business, adding value, using their skills and experience.
Robotics and automation are future proofing operations across the UK as we speak, providing a means to lean manufacture according to changing consumer trends and demands. OAL and KUKA UK are hosting a webinar that will discuss just how novel robotic applications are diversifying material handling and processing, delivering a multitude of advantages as manufacturers discover the benefits of robotic automation in novel applications.
To find out more and register for the webinar visit: Robotic Applications for Material Handling & Processing