4 minute read • published in partnership with Evocon
Insight: The benefits of root cause analysis in manufacturing
Evocon’s experience of working with manufacturers all around the world continues to demonstrate the importance of two key ideas. First, real-time visibility into the performance of your production process, whether you call it live OEE data or simply production monitoring, is a tool that substantially benefits continuous improvement efforts. Second, real-time production data and visibility by themselves are not enough. To fully leverage the opportunities presented by this new technology, manufacturers must empower more people on the shop floor with the knowledge of how to systematically solve issues which the data bring to light.
What is Root Cause Analysis?
Root Cause Analysis (RCA) has found a place in a wide range of industries and applications. This lead to many different understandings of what it actually is. Even within manufacturing, we see a variety of definitions. For example, RCA can be a form-driven bureaucratic process that is required when a problem is investigated. In other companies, RCA may be a creative and motivational process. One that began organically after a manager formed a team to investigate problems on the shop floor. The point is that root cause analysis can take many forms and does not have a universal definition.
However, this wide range does not mean that we cannot find some common ground to put forward a definition.
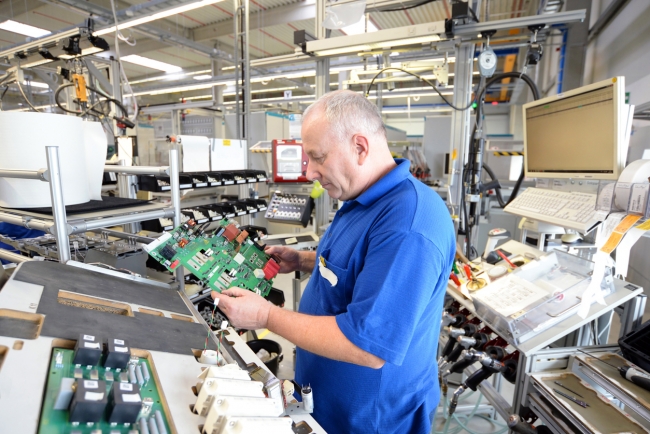
RCA addresses root causes directly instead of reactive fire fighting to help manufacturers improve productivity / Picture: Getty/iStock
How Root Cause Analysis Benefits Manufacturers
In today’s competitive manufacturing landscape, it is as critical as ever to utilize one’s resources as efficiently and effectively as possible. This naturally applies to activities on the shop floor, such as problem solving. As we will see, RCA is the best and possibly only method to find and eliminate long-term recurring problems. As such, it is the most efficient mean available to manufacturers, and this is the primary reason why they use it.
It is common for companies that do not have a working knowledge of Total Quality Management, Six Sigma, or Continuous Process Improvement to find themselves in an unending reactive state. You may have heard this situation referred to as “firefighting”. It can appear useful in the short term because the fire is put out. Though it is highly ineffective when it comes to preventing the fire from occurring again. Thus, the time and effort spent putting out the flames, or symptoms, is ultimately a waste as the effect is only temporary. The source of the fire still requires elimination.
For example, a typical production loss among Evocon clients is “Waiting on parts/Material missing”. The loss itself is self-explanatory and is an easy fire to fight by providing missing material. However, the underlying reason for why the material is missing isn’t as easily identifiable. Further, by putting out the fire without understanding or addressing its root cause, we fail to learn how to improve our processes. Moreover, we are likely to continue to experience the same loss in the future.
If you have worn the fireman’s hat day after day on the shop floor, you may notice two things.
First, the recurring problems that we couldn’t seem to stop stuck out like sore thumbs. Everyone knew what they were. Second, the reactive state that our organization operated in forced us to address symptoms. Further, everyone knew that the daily effort we expended did not improve operational performance over time. This does more than merely lower morale and waste people’s time. It can go so far as to erode the feeling that your work is meaningful.
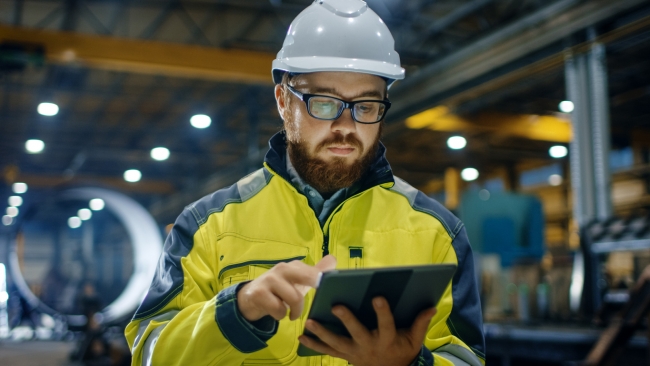
Once the root cause is eliminated the problem is removed for good / Picture: Getty/iStock
Efficiency and effectiveness are gained by manufacturers who target root causes rather than the symptoms of problems. Beyond this though, there are several other benefits to root cause analysis that can be identified. First among them is that it is logical, straightforward to learn and easy to use. Further, because RCA relies on facts and data rather than opinions or assumptions to be effective, the quality of solutions improves, as does the participation of most team members.
More benefits are possible by making RCA a daily exercise such that people say “this is the way we problem-solve”. The biggest is that RCA can transform an old reactionary culture into one of proactive problem solvers. This, in turn, reduces variability in processes and counteracts a risk-avoidance mindset.
Simply stated, solving the problem once is clearly the more cost-effective solution versus continual firefighting. Manufacturers do not have the luxury to waste precious resources this way. RCA helps them prevent this, and this is precisely why manufacturing companies use it.
Using root cause analysis in manufacturing to improve OEE
Overall Equipment Effectiveness (OEE) on the other hand, is the definitive metric used across industries for tracking production line performance. This is because OEE helps us to visualize, quantify and systematically eliminate sources of production loss.
Bringing the two ideas together then; we have OEE, which allows us to understand the problems causing our production losses. And we have RCA, a systematic problem-solving methodology used by manufacturers to prevent future recurrence of problems in the most efficient way possible. It follows then that this metric and problem-solving methodology fit perfectly together. Indeed, we find this to be true of our experience.
Can you use RCA without OEE? Absolutely, but to maximize the benefits of production monitoring to improve OEE, we recommend using them together. Our experience has demonstrated that the combination saves clients time in project identification and problem elimination. It follows that this increases the value generated by process improvement function overall.