4 minute read • published in partnership with KUKA
Insight: The evolution of robotics in the food industry
The adoption of automated robotic processes is on the increase in almost every step of the food supply chain. KUKA Robotics explores, that whilst the industry has been relatively slow in realising the benefits that can be afforded, there is now a significant demand for food grade robotics as changing consumer behaviours and population growth dictate manufacturers must improve process efficiency, to remain competitive in what is becoming an increasingly diverse market.
The variable nature of food items today, their fragile and perishable characteristics, the hygienic and health and safety constraints that exist; consider cross-contamination, dietary restrictions, allergy considerations. Greater attention must be given to how our food is produced, how it is processed, packaged, stored and eventually distributed. Add to the equation the fluctuation in volumes, driven by changing market trends and it is easy to see just why robotic food manufacturing is a growing trend in the food industry.
A recent study by the Packaging Machinery Manufacturers Institute suggests that as many as nine out of 10 food manufacturers are now using automation, in one form or another, as a means to manage the diversity of food products that are now being produced. If we consider the vast array and volume of food items that the UK consumes, the reliance on human workers alone is not enough, especially so when we consider product quality and consistency.
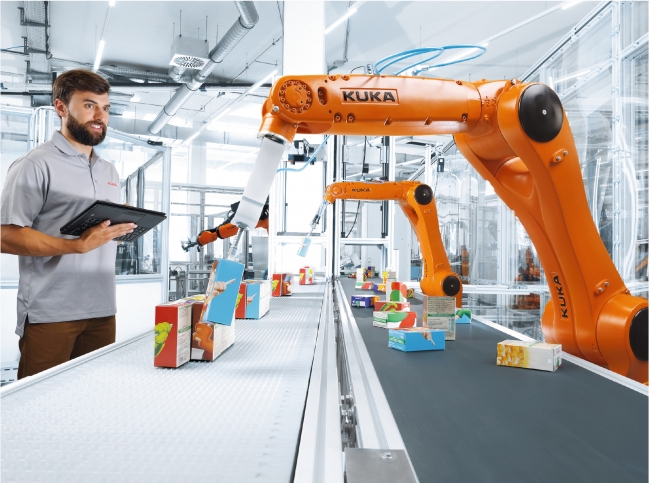
Manufacturers should position themselves to react to changes and diversify their operational processes with robotics to remain competitive / Picture: KUKA
Human workers can taint food with bacteria or a virus, which can mean costly downtime and product recalls which can have a negative impact upon a manufacturer’s brand, thus affecting future sales. Robots designed specifically for use within the food industry are sanitised and variants exist intended for use involving direct contact with foodstuffs with features such as stainless-steel parts, corrosion-resistant surfaces, and food-compatible lubricants.
There is also the environment in which the processes exist that should be considered. Some of the food processing procedures that feature within the food industry can be considered both dangerous and non-ergonomic for humans to undertake. Therefore, the need to automate is driven by improved safety and product throughput. Some storage facilities within the industry exist within deep-freeze stores. Humans can only occupy these facilities for short amounts of time, though manufacturers still need to ensure consistency of product throughput. Industrial robot variants have been designed specifically for this purpose, to manage the picking and packing of food items in extreme environments, both hot and cold.
Cutting and slicing is also a common, yet risky application within the food production and processing market. Historically attended by humans, it is now more often being managed by automated robotics. Repeatability and accuracy are just two factors that make automated processes more favourable, especially so when taking waste management into consideration. Whilst a human might be able to attend a cutting or slicing task, the accuracy of execution is always going to be an issue. The less waste that is generated, the more cost savings can be achieved.
Picking and placing of foodstuffs, such as fruit and vegetables (perishables) is one particular process that does still benefit from some human interaction, though there are automated applications in operation today that are able to attend the picking and placing of uniform fresh fruit and vegetable products. High-speed delta robots, utilising vision-guided software, can sort products within a conveyor system. Robotic arms with specially designed grippers can also be utilised to undertake picking and placing tasks. Though when we consider the quality of a product being distributed, can a robot really tell if a food product is overripe or substandard? Developed to pick based upon shape, automation certainly addresses the issue of throughput, though quality output could be questioned, simply because robotics does not yet have an eye for detail. Gripper technology, however, is evolving, aligned with the demands of the industry. End effectors have become sophisticated enough to pick up fragile food items such as tomatoes, eggs, and loaves of bread without damaging them.
New applications are emerging all the time and the evolution of robotics within the food industry is exciting. Control systems are becoming ever more sophisticated. Label and date code verification systems as an example, ensuring compliance with stringent codes of practice, supporting food safety and traceability.
Automated robotic ingredient handling and preparation downstream can return cost savings to manufacturers through the reduction in waste product and the delivery of accuracy of input not possible through manual means, producing superior quality, finished product.
Whatever the reasons to automate within the food industry, one thing is clear. The consumer is king and, as tastes change – consider the recent trends in eating habits as people consider the environment, sustainability and ethical farming practices and adopt vegetarian and vegan principles, manufacturers should position themselves to react to such changes and diversify their operational processes to maintain market share and remain competitive.