3 minute read • published in partnership with KUKA
Insight: The rise of the collaborative robot
Recent events have highlighted just how fragile our operations are when the key component within a supply chain is compromised: our workforce. And, it appears that the impact of C-19 shall be felt within the manufacturing sector for the foreseeable future, as businesses try to cover lost ground and, identify ways in which they are able to continue to operate, safely and efficiently whilst adhering to stringent safeguarding measures that shall have to be implemented within our manufacturing environments, primarily social distancing. KUKA highlights how cobots provide a multi-purpose operational value-add to manufacturers.
Manual production lines and complex manual production applications incorporating conveyor systems shall need to be re-evaluated. Co-workers stood shoulder to shoulder shall soon become a thing of the past. Two-meter social distancing legislation shall have to be incorporated into business plans and regulatory agendas established, to safeguard employees whilst successfully maintaining operational efficiencies.
This poses a significant conundrum for many businesses whom rely upon manual methods to ensure the supply versus demand balance is maintained. Realigning operating models, especially for SME’s, can be costly. Consider having to make changes to infrastructure and operational footprints, to allow for the increase in space needed for operators to continue to work safely. This can not only be costly, but disruptive. So how do we approach the dilemma of safe working practices when, for some businesses, it’s almost impossible without detriment to their productivity? The solution is to employ a lightweight, sensitive robot. Sometimes referred to as collaborative robots or, cobots.
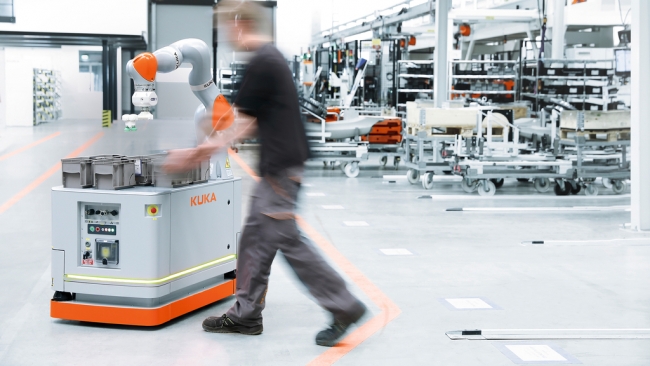
Cobots offer a flexible, efficient and multi-purpose operational value-add to manufacturers / Picture: KUKA
These sensitive robots are very different to conventional industrial robots widely used within the manufacturing sector, as they are HRC compatible (human robot collaboration) and can work safely alongside human operators without external safety devices, such as fencing/guarding, sensors or light curtains.
In human-robot collaboration, the robot assists the human operator. The machine does not replace the human but complements their capabilities and can relieve them of non-ergonomic tasks; mundane, repetitive, strenuous tasks. Human and robot can work in close cooperation, sharing tasks within any given application. But how does the adoption of collaborative robotics assist in addressing safe, social distancing working practices that shall soon become the norm within many manufacturing environments?
Business owners within the manufacturing sector will have to adjust if they are to survive. An increased focus upon reducing the concentrations of workers near to one another is needed, whilst maintaining continuity of production. Especially so to future proof against another major interruption to their manufacturing and supply chain.
When introducing a sensitive robot within an application or process, there exists no significant downtime. Adjustments to the immediate production landscape are not required. Cobot footprints are significantly smaller than larger industrial robot models and can be introduced to an existing application by way of static or mobile means. Various methods of programming also allow for easy integration, with some sensitive cobot models possessing teach and learn software, that enables an operator to move the robot arm, whilst in compliance mode, through a series of movements and/or tasks that are then repeated. If paired with a mobile platform, controlled by software that utilises sensors to identify its immediate surroundings and move about an environment, a cobot affords a whole host of benefits, not only being able to move between work stations but supporting multiple applications/programmes aligned with several individual tasks within a supply chain.

Cobots do not replace human operators but complement their capabilities and can relieve them of non-ergonomic tasks / Picture: KUKA
The key advantage of the cobot, whether static or mobile is that it does not need to adhere to stringent health and safety measures that are applicable to social distancing currently being adopted across the manufacturing sector – business owners can retain their established production footprint, but re-position key, skilled personnel and supplement production with sensitive robots.
Social distancing is a workplace reality and, cobots will offer a flexible, efficient and multi-purpose operational value-add to manufacturers whom want to achieve operational continuity throughout these testing times.