3 minute read • published in partnership with KUKA
Insight: The rise of warehouse automation
Automation in the materials handling industry covers a plethora of technologies encompassing sortation systems, ancillary equipment and warehouse management systems, to name but a few. All support improved operational efficiency, though when we consider the need to improve process quality as a means to maintain those efficiencies, we should examine just how automated robotic applications are diversifying supply chains and enabling business owners to gain a competitive advantage in what is a fast moving and ever evolving industry.
The IoT (internet of things) and online market places (ecommerce) have made it possible for the consumer to order and receive goods within a matter of hours and the time-sensitive demands of today’s online shopper means that our supply chains have to utilise automated tooling, robotics, as a means to satisfy the huge demand for goods.
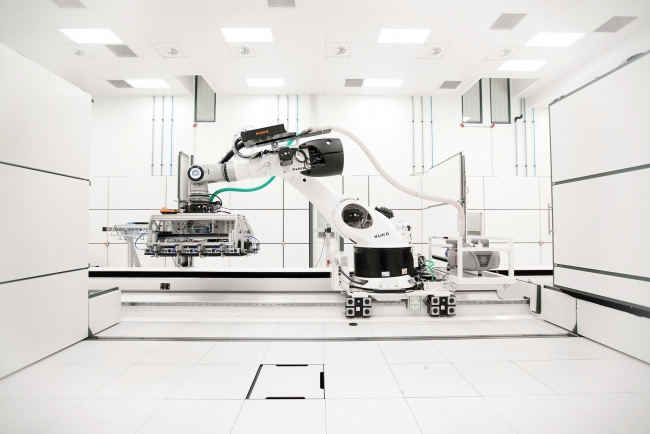
A highly automated logistics facility can support operational throughput and profitability whilst delivering value and saving costs / Picture: KUKA
Manufacturers today face a huge variety of materials handling challenges. Some handling tasks simply can’t be undertaken by manual means or human intervention. Environment and application ergonomics within a logistics and supply chain facility mean some tasks are simply too dangerous for humans to execute. Consider upstream activities such as palletising and/or storage and retrieval. From a health and safety perspective automation is the only viable option, though we should also explore the cost impact of a manual application versus an automated application.
Lifting, moving and sorting are the primary objectives within a warehouse environment, though these actions are considered non-ergonomic; inefficient and uncomfortable for humans to undertake on a repetitive basis over a long period of time. Product throughput is the lifeblood of any successful operation. This success relies upon how much can be distributed quickly and efficiently. A highly automated logistics facility can support operational throughput and profitability whilst delivering value and saving costs.
But how?
1 – Improved speed and precision of routine operations.
The repeatability and accuracy of an industrial robot arm is far superior to that of a human. Direction, acceleration and velocity, determined by a series of pre-programmed motions, means that the robot can continue to operate 24/7 without deviating from a predefined path. Humans can tire and thus, must take breaks. Concentration levels can wane, leading to picking and placing errors.
2 – Improved warehouse management.
The need for regular inventory checks is also reduced as error rates are reduced as picking and packing applications are optimised, such as picking, sorting and storing. The ability for autonomous systems to harvest data, critical for forecasting and identifying fluctuations in market trends also supports sustainable practices.
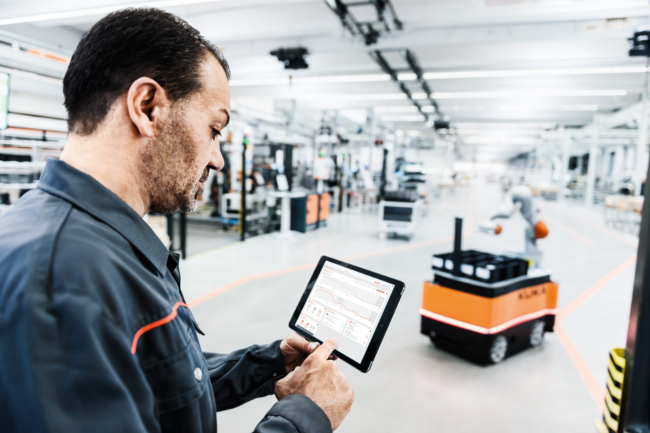
In the age of IoT, automation improves efficiency and enables business owners to gain a competitive advantage / Picture: KUKA
3 – Support around the clock operations.
Robotic technology is evolving and there exists a broad spectrum of both static and mobile robotic solutions. AGV’s (automated guided vehicle) or mobile robots can operate both night and day, at the same cost. Finding skilled operatives to work unsociable hours can be difficult, though in order to remain competitive and maintain the supply versus demand balance, operations must continue into the night. A fully connected factory, aligned with the smart factory concept, enables warehouse systems to connect to the technology (robots) on the shop floor; a complete digital supply network, flexible, adaptive and proactive.
4 – Provide an attractive USP to customers.
Efficiency and value are just two factors that draw a customer. An automated warehouse/supply chain environment is competitive in its offering, both from a performance and cost perspective. If a customer is able to achieve a level of product throughput that supports their business goals, but also makes them attractive to their customers, it’s a win-win. We should also be considering how we intend to future proof our operations. Investing in technology such as automated robotics sends a clear signal that we are looking forwards and setting ourselves apart from our competitors.
5 – Automation will pay for itself.
There is a significant investment when automating within an existing operation that is clear, though that initial investment will eventually pay for itself. Consider an operative who is employed on an annual salary. Consider weekends, holidays, sickness, and breaks. None of these apply to an automated robot. That investment supports a ‘worker’ that can operate 24 hours a day, seven days a week, 365 days a year. And you only make that one initial investment, there is no annual salary, per se, no sick leave or holiday leave. And as your investment starts to pay for itself and your operations evolve, you are able to upscale and invest again.
The future of robotics and automation within the materials handling industry; warehousing, logistics and supply chain, food and beverage etc. is happening now. We shouldn’t be considering whether robotic technology could be right for our right operations, but that it is.