2 minute read • published in partnership with ATS
Insight: What to focus on when starting your digital manufacturing journey
The fifth industrial revolution, just when you get to grips with the fourth industrial revolution, you hear that there is a fifth. With the harsh reality that many manufacturing organisations are barely operating within the fourth industrial revolution, Mark Boulton from ATS looks at what to focus on when starting your digital manufacturing journey.
What is behind all the buzzwords? It all sounds so great on paper, no wait, I mean digital platforms, but what is it all about and how realistic is it and what are the real challenges of adoption, that we do not talk about?
“Digital twins, AI, edge, cloud, data lakes” … “I have an app on my smartphone that tells me how my boiler is operating, why can’t I ….” Whilst walking around the shopfloor, watching “Bob” write his KPI information on a bit of paper, with his years and years’ worth of knowledge and experience. Does that sound like the reality we really face? Digital adoption is achievable, it really can be. But the jump into digital transformation, technologies, processes, infrastructure, and investment required should really be more a hop, skip, then a jump.
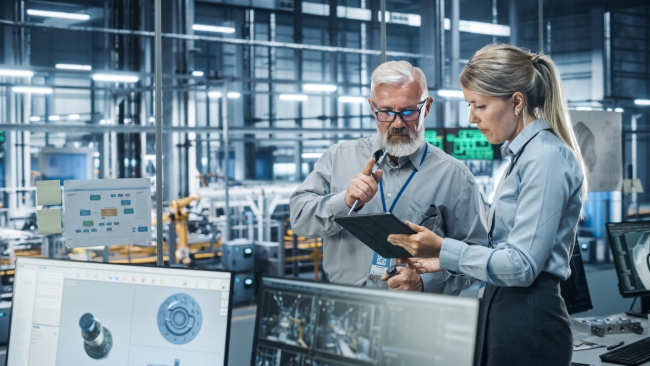
A digital manufacturing journey is not a system deployment, it is a business change / Picture: Getty/iStock
Here are some truths that I don’t think people talk enough about, when going on this digital journey.
Data connectivity, standardisation and collection is harder than you think.
Unless you have all the latest machine tools, a green field site, most of your time will be figuring out how to extract data from machine tools, that runs a critical part of your operation. It’s not just a module you turn on in software, it not like Bluetooth and the data just comes out, it’s going to take time working with the machine tool OEM and opening the machine, adding sensors, etc. to get the data you want in a standard format.
You going to need a shopfloor IT infrastructure.
That allows for flexibility but is secure (because we all know these go hand in hand). That’s going to require a level of investment. Also remember that your shopfloor changes, your infrastructure must allow for this.
The system becomes operationally critical.
The manufacturing process you have been running for years and years without fault, is now running with IT platforms that have a 3-year renewal life span. Where operating and software are continually updated. Support and downtime windows become paramount.
People might not be comfortable using technology.
There is an assumption that everyone can use technology and that they are comfortable using it. That’s not the case. Take this into consideration when thinking about the system interfaces, automation and training. Make sure your shopfloor users are part of the process.
If you’re looking to start your digital manufacturing journey, feel free to reach out to ATS, we can share our insights (and battle scars). Is it worth it? 100% it is! But just remember it’s not a system deployment, it is a business change.