3 minute read • published in partnership with Mazak
Mazak launches new British-built machining centre
Yamazaki Mazak has underlined its commitment to the British machine tool industry with the launch of its newest fully simultaneous 5-axis machining centre – the CV5-500 – which will be the only machine in its class to have been completely conceived, designed and built in the UK.
The CV5-500, which is currently being manufactured at Mazak’s European Manufacturing Plant in Worcester, is being marketed with a highly competitive price point making it ideally suited to subcontractors, start-ups and job shops.
The versatile 5-axis machine is unique in its category due to its high-rigidity bridge construction with a fully supported trunnion table that travels in the Y-axis direction under the bridge, ultimately delivering an extremely accurate and compact machining solution.
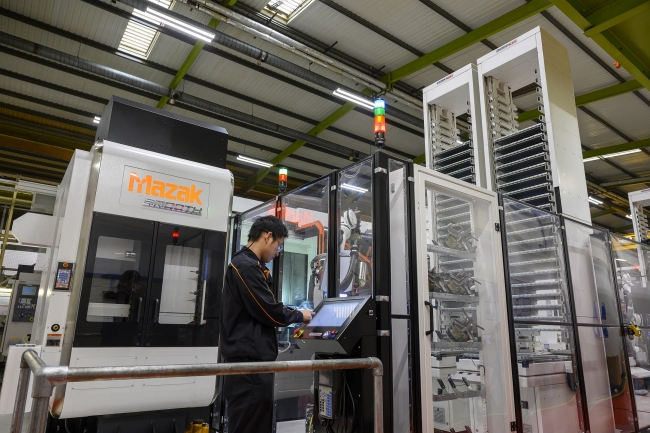
The new 5-axis machining centre will be built in Britain at Mazak’s Worcester factory / Picture: Mazak
Alan Mucklow, Managing Director UK & Ireland Sales & Service Division at Yamazaki Mazak, said: “While the numbers of British machine tool builders have dwindled over time, Mazak has consistently continued to invest in its UK R&D and production facilities. The CV5-500 is the latest in a long line of Mazak machines to have been fully designed and built in Britain. Not only does it set a new benchmark in British machine tool building, but it breaks the mould for the compact, fully simultaneous 5-axis machining category as a whole.”
“The CV5-500 can deliver a step-change in productivity for both seasoned 5-axis users, as well as those looking to take their first steps in the technology. From its high-rigidity bridge construction and newly designed constant overhang headstock, to its ergonomic design and easy integration with ancillary automation systems, the CV5-500 is every inch the modern machining centre.”
The CV5-500 features a newly designed constant overhang headstock to maintain machining rigidity even at the full extent of the Z-axis stroke. It is equipped with a 12,000 rpm spindle, capable of a peak performance of 18.5 kW and 119.4 Nm, making it suitable for a wide range of materials. An optional 18,000 rpm spindle, which includes core cooling through the X-, Y- and Z-axes ballscrews for thermal stability, is available for high-speed applications.
The machine is equipped with a high-rigidity Sankyo table, driven with roller gear cam, that provides a wide angle of rotation, specifically 220o in the B-axis and 360o in the C-axis. The CV5-500 delivers agile performance, with rapid traverse rates of 36 m/min in the X-, Y- and Z-axes, and can process work pieces up to Ø500 mm x H320 mm, and up to 200 kg in weight. Additionally, the Thermal Shield system maintains stable cutting accuracy by applying automatic compensation to combat temperature fluctuations.
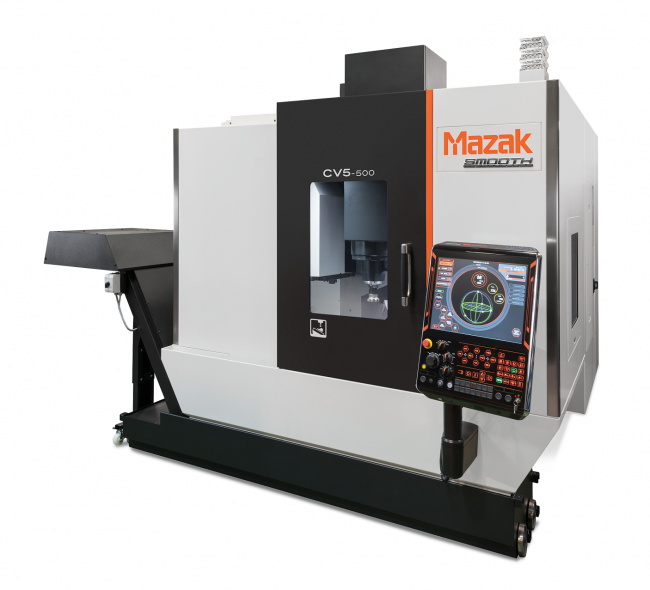
The new compact CV5-500 is ideally suited to subcontractors, start-ups and job shops / Picture: Mazak
As well as offering high performance, the CV5-500 design prioritises operator access and ergonomics without compromising the potential to integrate automation systems. The machine can be easily supported with a variety of automation solutions due to the addition of a side-loading door, robot interface and hydraulic and pneumatic fixture interface options. Crucially, access to the front of the machine remains uninhibited from automation equipment, meaning operators retain convenient access for setups with full visibility of the machining operation at all times.
At just 2,300 mm x 2,790 mm, the machine is the most compact 5-axis machine in its class, making it ideal for general subcontract and job shops where floor space is at a premium. Careful attention has been paid to minimise the surrounding maintenance area, specifically with the coolant tank with side exit chip conveyor, that can be pulled out from the front of the machine to provide convenient access to key maintenance areas. In addition, the rear of the machine can be sited close to a factory wall to minimise floorspace.
The tool magazine comes with a 30-tool capacity as standard and an option for 48 tools if required, while the double arm ATC offers a fast tool-to-tool time of just 1.3 seconds. A side loading door to the magazine is standard which conveniently allows tools to be replaced even in automatic cycle.
The new machine is equipped with SmoothX CNC, Mazak’s specialist 5-axis version of its SMOOTH Technology.