4 minute read • published in partnership with igus
Recovering crude oil from plastic: recycling project by igus partner Mura Technology takes next step
Recycling pioneer Mura Technology is making great strides in building the world’s first HydroPRS plant, scheduled to go into operation in early 2023
British company Mura Technology aims to recover crude oil from plastic with the HydroPRS chemical process to accelerate the circular economy of plastics. Since 2020, motion plastics specialist igus has supported Mura Technology as an investor. The first HydroPRS plant for the chemical recycling of plastic waste is currently being built by Mura’s subsidiary ReNew ELP in Teesside. The recycling pioneer is making good progress on the build and expects the plant to be operating at the beginning of 2023.
In April 2021, the construction of the first HydroPRS plant to chemically recycle end-of-life plastic waste began at the Wilton International site in Teesside. The process enables the recycling of unsorted plastic waste with a low CO2 footprint. HydroPRS is insensitive to organic contaminants such as paper and food scraps, making a wide range of plastic waste suitable as a starting material. The plastic waste material is shredded in Mura’s own material processing plant and separated from impurities such as glass, stones and metals.
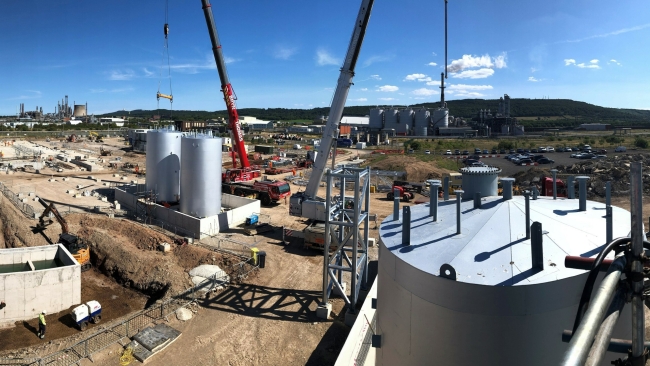
Mura Technology is making major progress in the construction of the world’s first HydroPRS plant for the chemical recycling of plastic waste / Picture: Mura Technology
ReNew ELP continues to make good progress in the construction of the plant, although the covid pandemic and raw material shortages, as in other industries, have affected the project. After the excavation and civil engineering work, earlier this year concrete was finally poured to build the foundations and substructures for the buildings and facilities. In July, the first plant items such as storage tanks for distillate were delivered to the construction site. Some equipment is also stored in local warehouses or at the suppliers’ premises, which helps with assembly planning, as the equipment is available at short notice and can be installed efficiently. The next major steps are the material processing plant and the main processing plant. In July, Mura began programming the control software for the HydroPRS plant, which is likely to be completed soon.
Ambitious global expansion plans
The company aims to put the ReNew ELP site into operation at the beginning of 2023. In the first phase, the capacity of the plant is 20,000 tons, which will be increased to 80,000 tons after the first 12-months. By comparison, the world’s largest rubbish vortex, the Great Pacific Garbage Patch, which floats in the Pacific Ocean between Hawaii and California, currently consists of about 80,000 tons of plastic waste, according to researchers’ estimates.
More HydroPRS plants are expected to be built in Germany and worldwide. Several possible locations have already been identified, and one is currently in the development phase, expected to go into operation by 2025. The planned plants in Germany have a processing capacity of 50,000 to 100,000 tons per site. Mura Technology’s business model includes its own locations in the UK, Europe and the US as well as worldwide licensing opportunities through Mura’s partner KBR. In the meantime, other partners such as Dow, Chevron Phillips Chemical and Mitsubishi Chemical have been added. igus has been a partner of Mura since 2020 and has invested €5 million in the project.
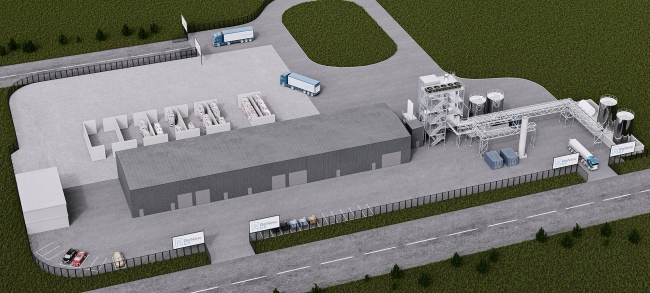
100 new permanent jobs are expected to be created once the plant is operational / Picture: Mura Technology
Working together for more sustainability
Mura is already working with suppliers to supply the HydroPRS plant in Wilton with plastic waste, companies that will collect plastic waste from households and towns and deliver it to the site. But Mura is going one step further and is actively driving the development of this new industry by working with policymakers and other stakeholders to promote plastic waste recycling. To illustrate the positive environmental impact of its own HydroPRS plant at the Wilton site, Mura is also working with independent partner Warwick Manufacturing Group (part of the University of Warwick) on a life cycle analysis of the plant, due to be published in autumn 2022.
“We understand the great potential of this breakthrough technology and support Mura Technology to help chemical recycling make a breakthrough,” says Frank Blase, Managing Director of igus Group. “Together, we want to promote the circular economy of plastics in order to conserve precious resources and raw materials.”
igus has invested heavily in a range of recycling and carbon reduction activities. For more than 50 years, igus has been regranulating 99% of the plastic waste generated in its own production facilities and in 2019 the company launched its own recycling program for end-of-life energy chains, called “Chainge”. igus’ first products made of up to 100% recycled material were also launched this year: the cradle-chain and iglidur ECO plain bearings. In addition, igus launched the igus:bike project for sustainable, urban mobility. This concept is an all-plastic bicycle that is completely lubrication- and rust-free and whose frames and wheels can also be made from post-consumer plastic waste. With the igus:bike platform, igus also wants to promote knowledge about plastics in the global bicycle industry and promote this circular economy internationally.