See Inside: The Airbus factory in Broughton
Airbus’ Broughton factory in Flintshire, North Wales, has a proud aeronautical history and is where aviation classics such as the Vickers Wellington and Lancaster and De Havilland Comet and Mosquito aircraft were produced. Today, the site is responsible for assembling wings for the entire family of Airbus commercial aircraft, including the A320 and A330 Families, the A380 and the next generation A350XWB (extra wide body) aeroplanes. We take a look inside and explore some of the facts & figures behind the site.
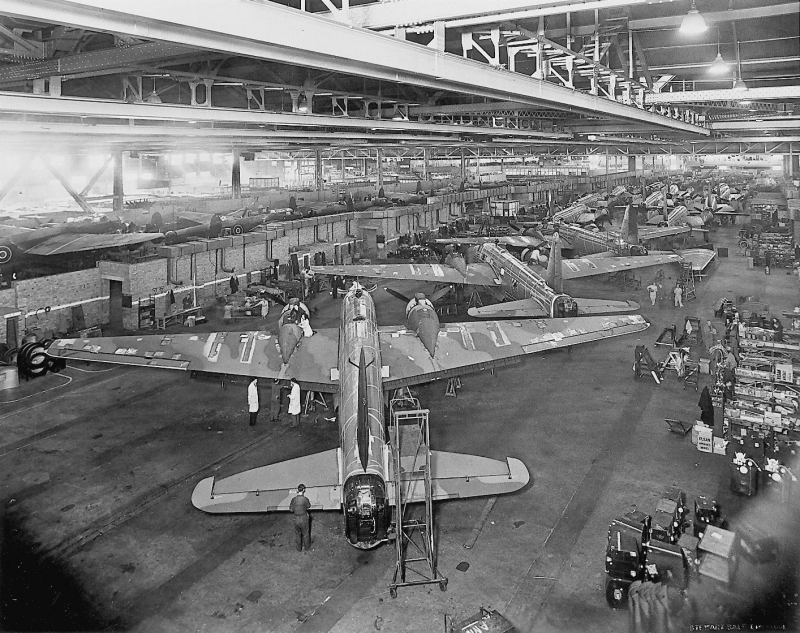
Picture: Airbus
In September this year, the aircraft manufacturing site in Broughton, North Wales, will celebrate its 80th birthday. Built as a government shadow factory to build the Wellington bomber by Vickers in preparation for war, the factory now assembles wings for all Airbus’ commercial aircraft, except for the new A220, whose wings are assembled in Belfast.
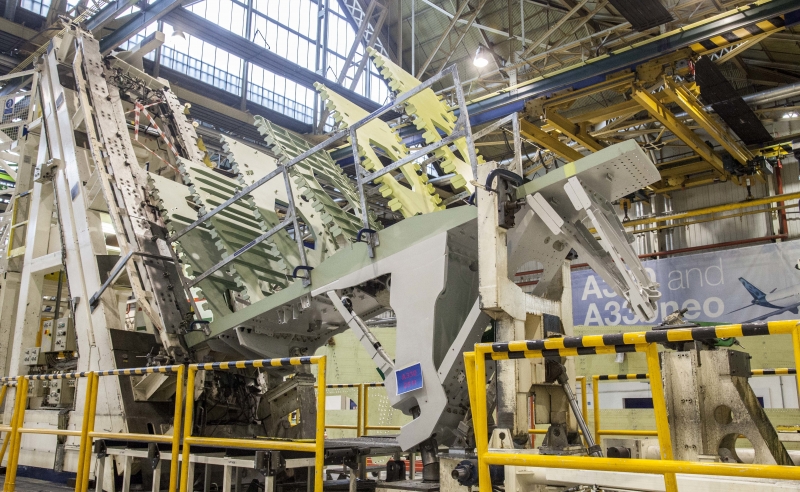
Picture: Airbus
The 700-acre Airbus Broughton site in Flintshire employs 6,000 people and features a 2,034m runway, known as the Hawarden Aerodrome, as well as 439,000 square meters of industrial floorspace
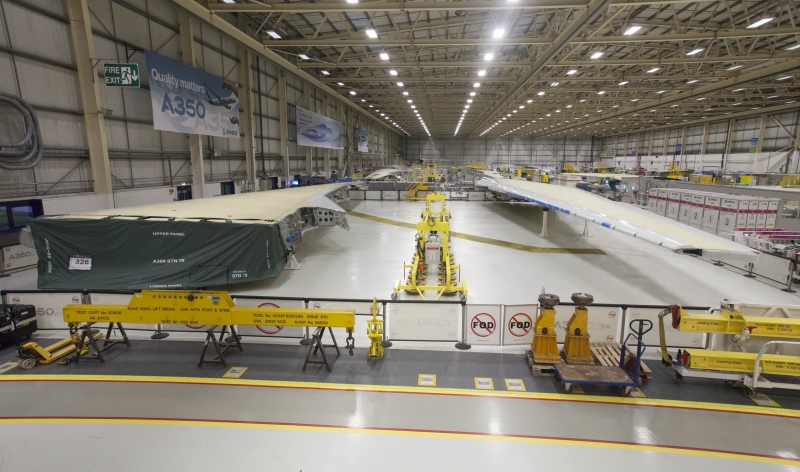
Picture: Airbus
Around 60% of Airbus Broughton’s employees live in Wales and Airbus’ first tier supply chain spend is worth about £500 million to the Welsh economy per year.
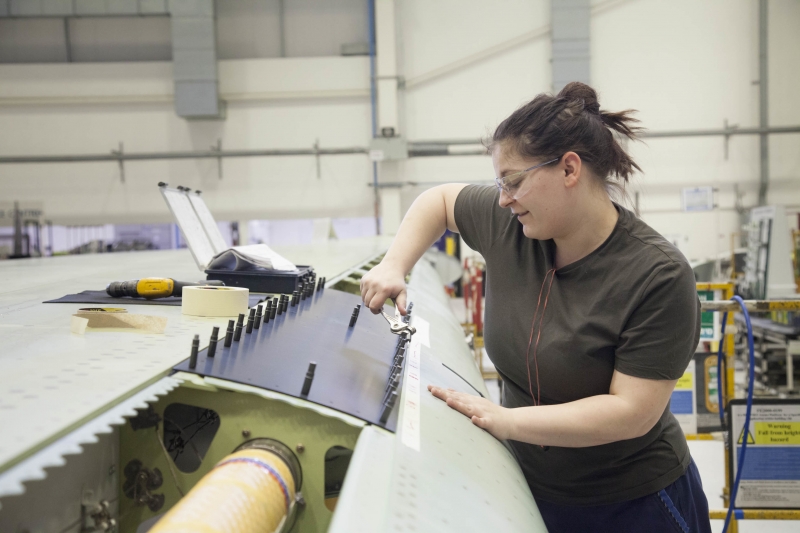
Picture: Airbus
In 2009, Airbus invested £400million in a new production facility known as the North Factory to assemble wings for the latest Airbus aircraft – the extra-wide-bodied A350 XWB. The A350 XWB programme supports more than 1,200 jobs at Airbus in the UK and 5,000 more across the wider supply chain.
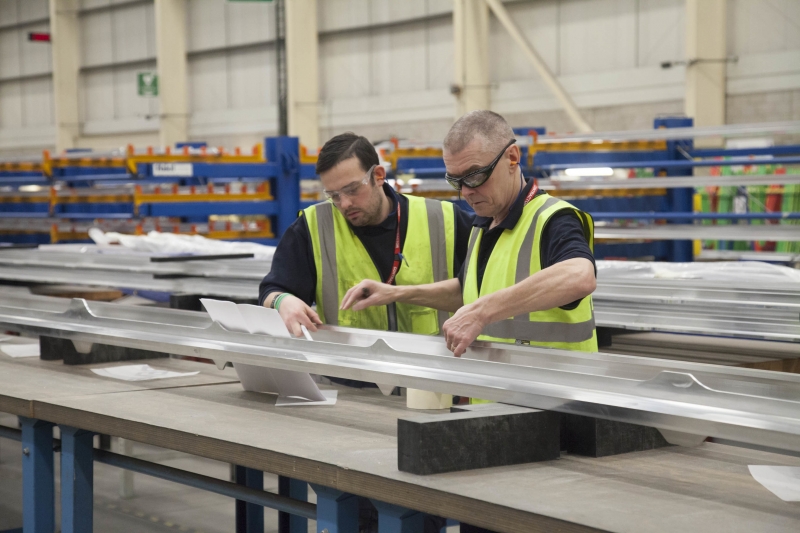
Picture: Airbus
Assembling wings for Airbus commercial aircraft starts with the long-bed machining of large-scale components, such as wing skins, or panels, and stringers which are used to fasten the skins together. The panels are then assembled in large structures called jigs to form the wingbox which is then transferred to equipping.
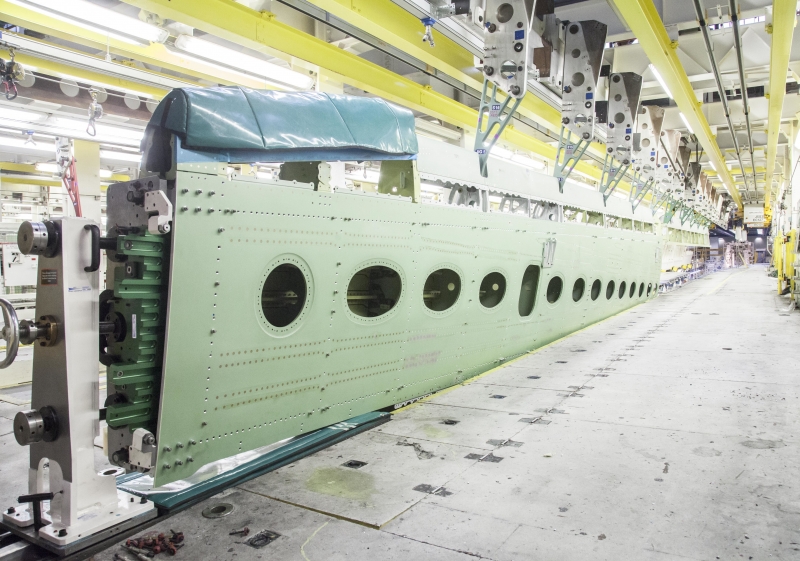
Picture: Airbus
For A380 and A320 Families, the ‘equipping’ is completed at Broughton. This is when the wingbox becomes a fully tested and functional flying wing with the electrical, hydraulic and fuel systems installed and tested. A330 and A350 XWB wings are partially equipped at Broughton but are flown by the Beluga transporter plane to Bremen, Germany, to the final wing equipping line.
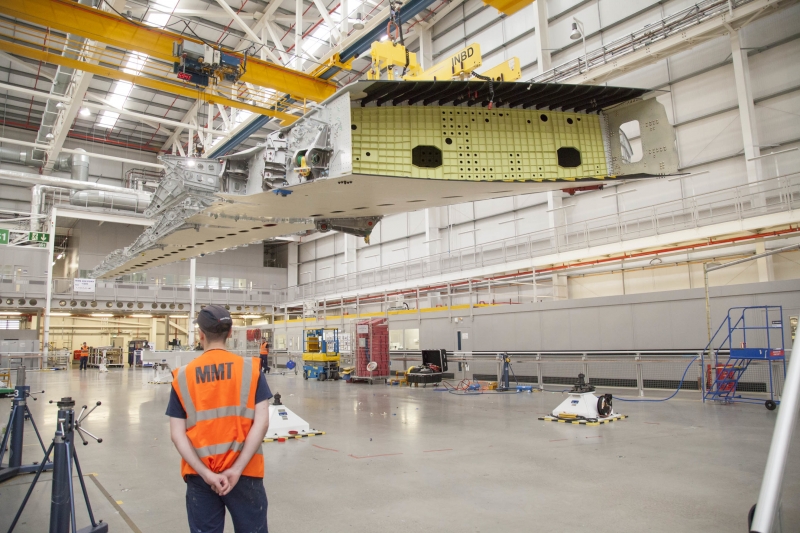
Picture: Airbus
The Broughton plant recently made its 350th pair of A350 XWB wings. Over 50% of the wing is made from new, high-strength, lightweight composite materials, rather than traditional aluminium. The wing covers are made from carbon fibre reinforced plastic, as are the front and rear main wing spars.
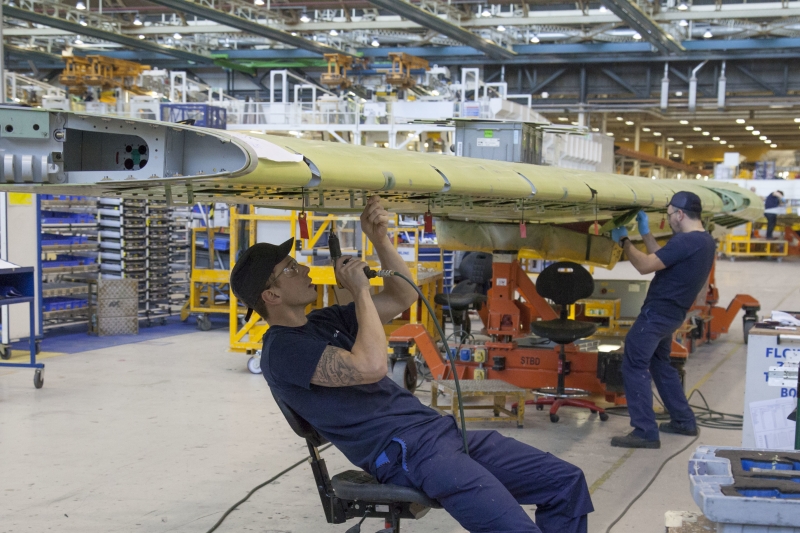
Picture: Airbus
In 2018, 739 wing sets were delivered from Broughton to final assembly lines (FALs) in Toulouse, France, and Hamburg, Germany.
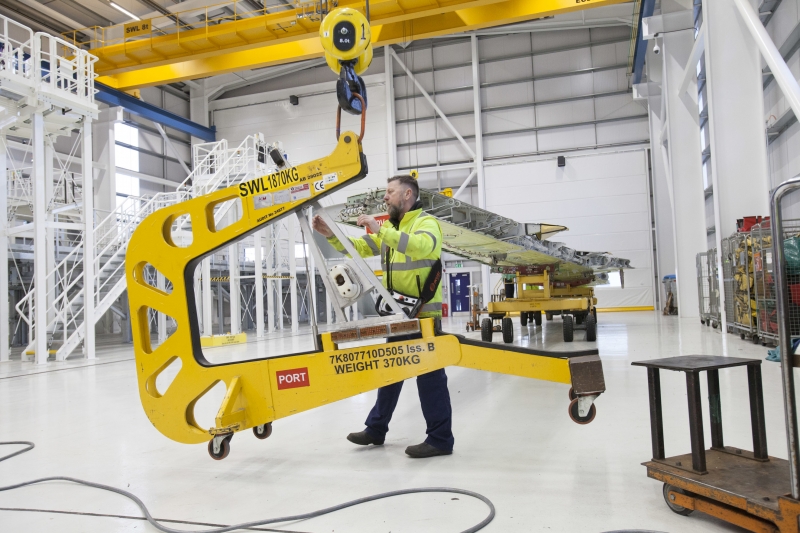
Picture: Airbus
Airbus’ Broughton site is a critical part of the company’s international operations and produces wings that enable Airbus to make more than 60 aircraft per month. In 2018, Airbus delivered a record 800 aircraft to customers and took orders for a further 747 planes.
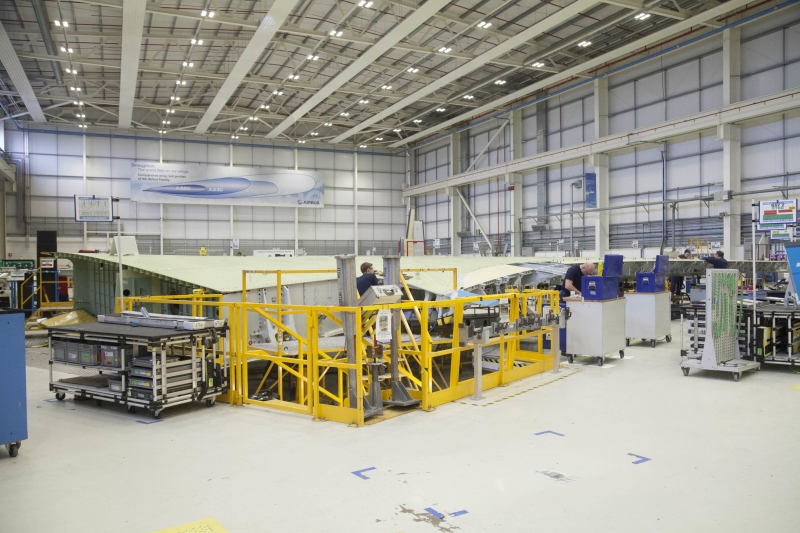
Picture: Airbus
The wings of an aircraft are one of the most technically complex parts of the plane’s structure. They define the overall aerodynamic performance and are particularly important for securing excellent ecoefficient solutions.

Picture: Airbus
Airbus’ East Factory has a long history of aviation work and part of the site dates back to 1939. The East Factory is where the wings for the best-selling A320 Family single aisle aircraft are assembled, as well as the long-range A330 wings.
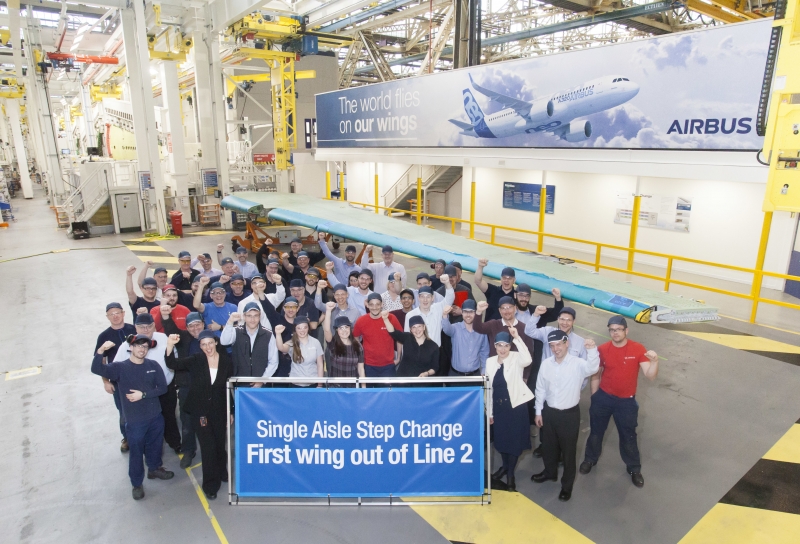
Picture: Airbus
Airbus’ ‘Step Change’ facility in the East Factory is embracing modern manufacturing methods such as automation to allow for quicker assembly of A320-Family wings to meet demand and reduce the backlog of orders. The first wing out of the Single Aisle Line 2 was produced in March 2018.
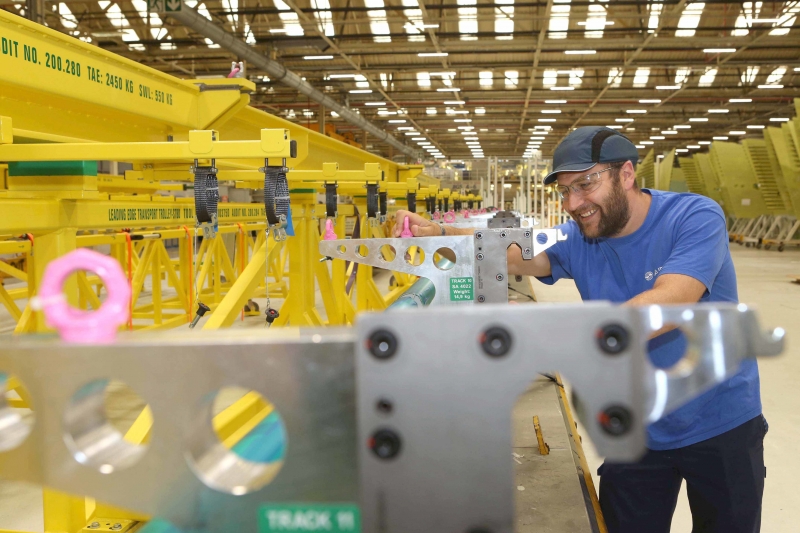
Picture: Airbus
Step Change uses the latest robotics technology in key areas of drilling to achieve the required build rates going forward. The assembly process also differs in Step Change insofar as the wings are moved to the next station, rather than the workforce moving to the next wing job.
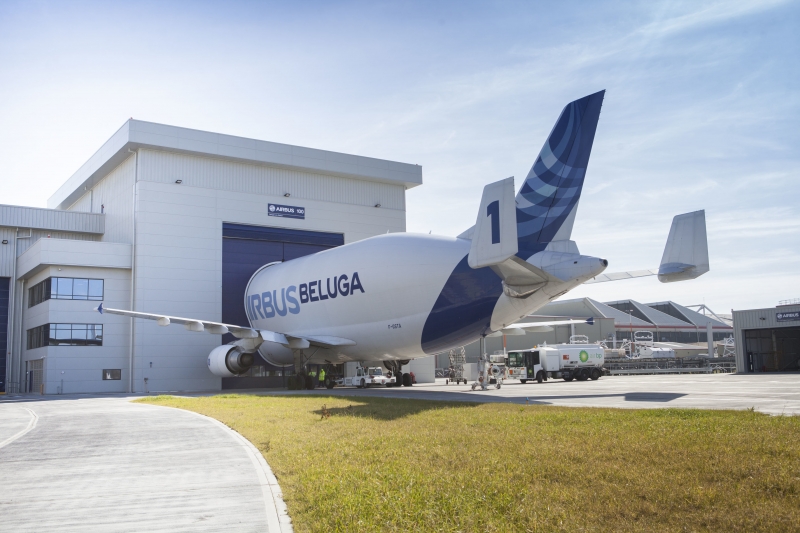
Picture: Airbus
The Beluga aircraft, so-named for its resemblance to the cute white whale, is a giant transporter plane that takes Broughton wings to the FALs in Toulouse and Hamburg. The Beluga Line station is a purpose-built facility for loading the wings on to the transporter regardless of weather conditions. It takes about 70 minutes from landing to take-off to unload and load the Beluga.
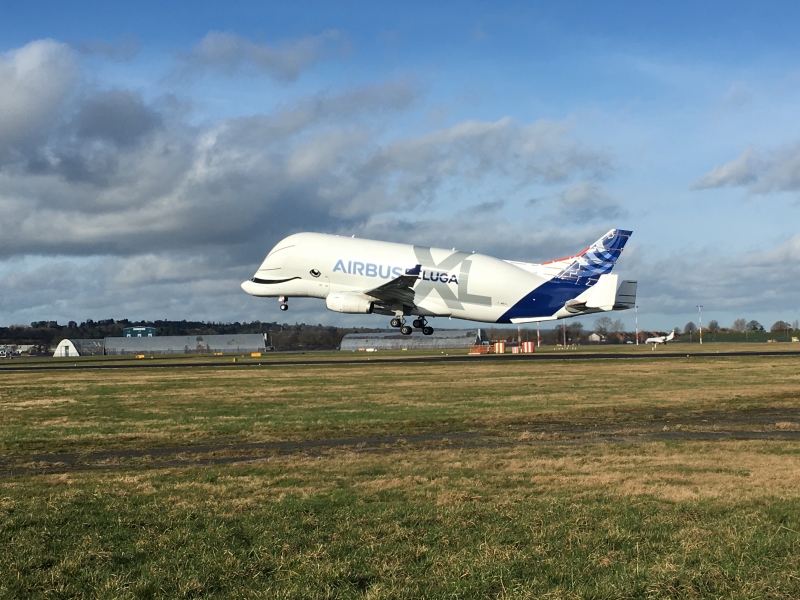
Picture: Airbus
Fully equipped A320 wing sets are delivered by Beluga to the Final Assembly Lines in Toulouse and Hamburg but the current Beluga could only carry one A350 wing at a time, so Airbus has built a replacement – the BelugaXL (extra large) – which can take a pair of A350 wings on every journey. The BelugaXL is currently being tested and will enter service later this year.
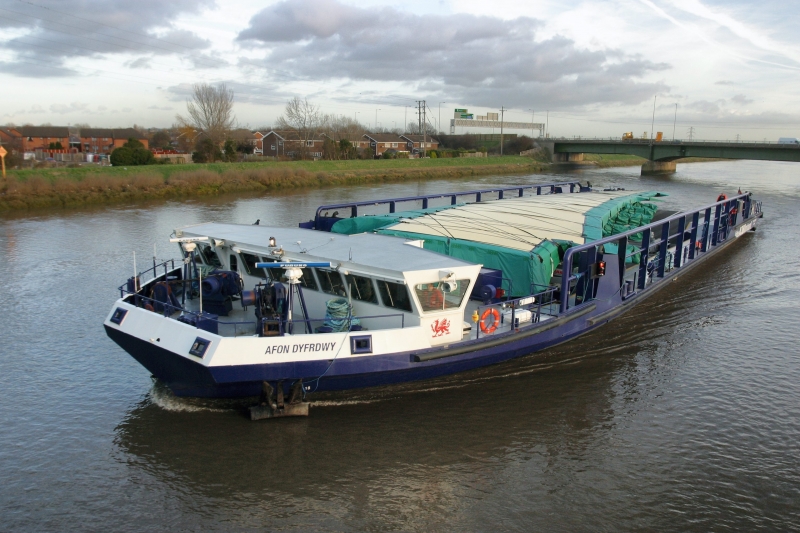
Picture: Airbus
Wings for the A380 double-decker aircraft are too large for the Beluga or even the BelugaXL and make their journey to the final assembly line in Toulouse by river, sea and road on specially designed vehicles, barges and ships.
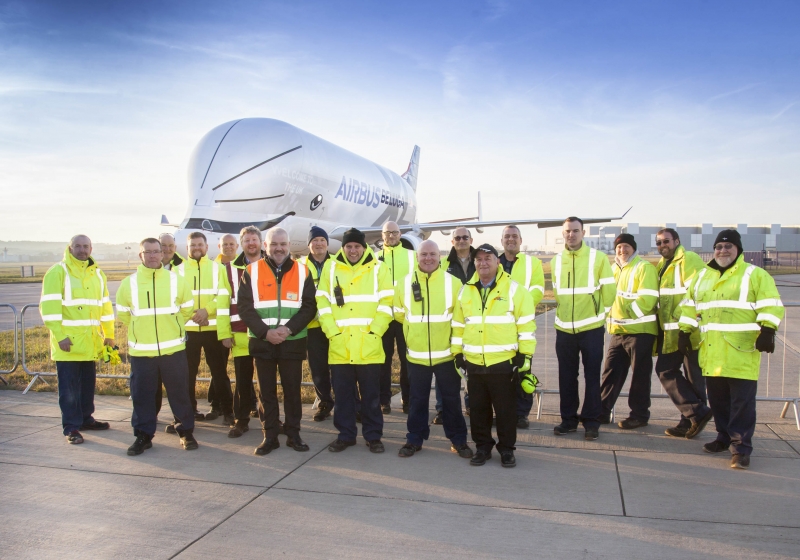
Picture: Airbus
Airbus has invested €31 million into the project to improve and streamline Beluga operations at Broughton. The new BelugaXL landed in Broughton for the first time on 14 February 2019, when it was given a true Valentine’s Day UK welcome watched by more than 40 media outlets. The livery of the BelugaXL features a smiling whale face – chosen by Airbus employees – and has become a firm favourite with plane spotters across Europe. The aircraft will feature in a BBC4 series to be aired this summer.
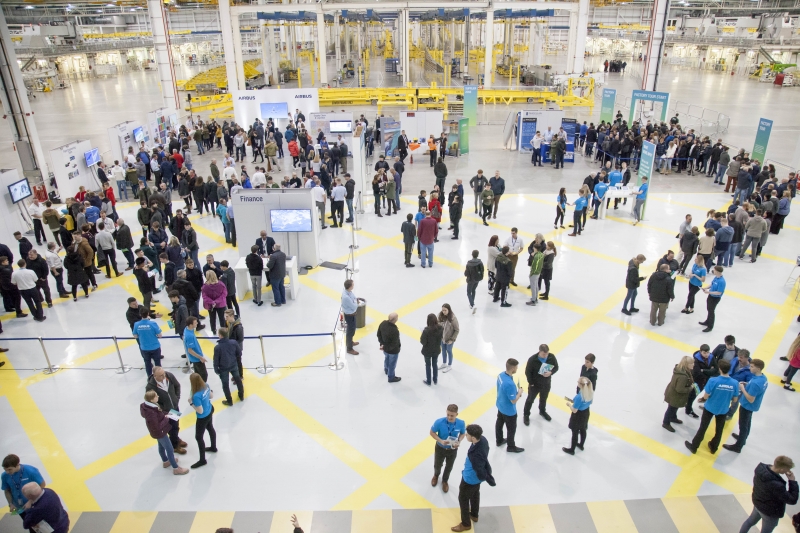
Picture: Airbus
Airbus in the UK currently has more than 420 apprentices, 100 graduates and 126 interns among its 13,500 UK employees within its commercial aircraft, helicopter and defence & space divisions. More than 140 new UK apprentices joined the company in September 2018.
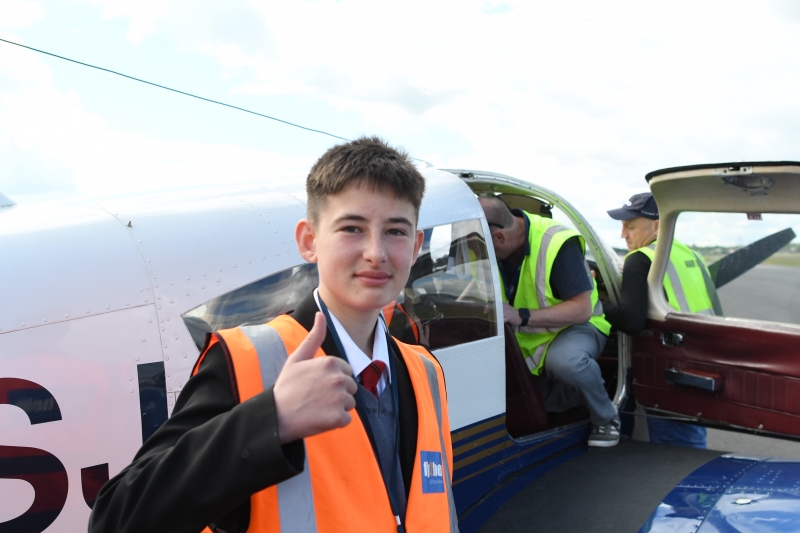
Picture: Airbus
Airbus Foundation’s Flying Challenge programme is a youth-mentoring scheme that has seen the young people from Ysgol Treffynnon school in Flintshire attend 20 weekly sessions at Airbus Broughton to gain insight into the aviation and aerospace industries. The highlight for the pupils was a flying day in June where they each took control of a light aircraft during a flying lesson at Hawarden Aerodrome. They receive their graduation certificate this summer.
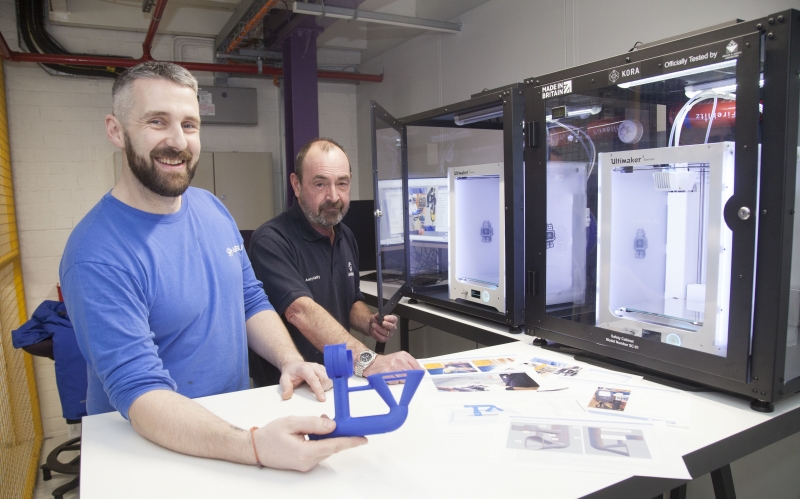
Picture: Airbus
Airbus encourages innovation from every part of the organisation and shopfloor operators in Broughton, Phil Ellis and Andy Kelly, created a 3D-printed extraction shroud for a router as the original supplied was not picking up enough swarf.
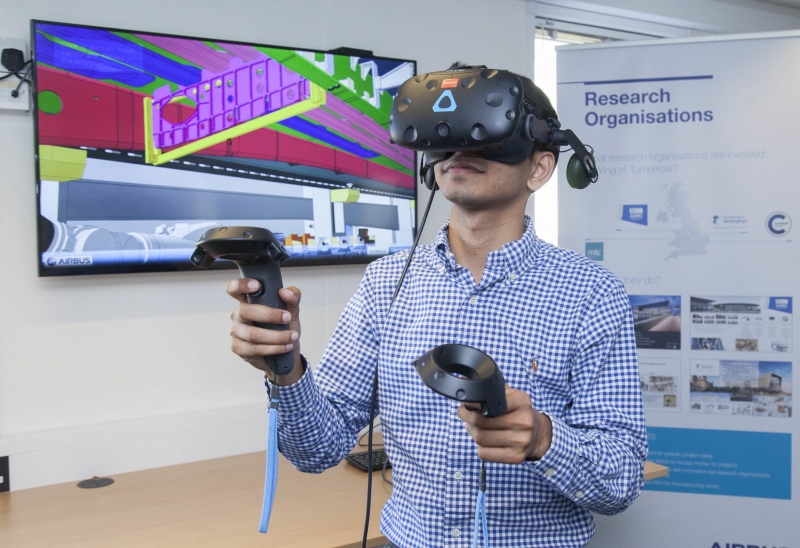
Picture: Airbus
The Welsh government has invested £20m to build the new Advanced Manufacturing Research Centre Wales facility on the Broughton plant’s site. A virtual reality suite is being used to simulate the AMRC Wales facility and show how it will be used for Airbus’ ‘Wing of Tomorrow’ project that seeks to build lighter, stronger wings.
We would like to ‘See Inside’ your factory and share some insight about the investment, growth and future plans you have – if you wish to be featured, please get in touch on hello@zenoot.com