See Inside: The Ford engine factory in Dagenham
2019 marked 90 years since work started on constructing the Ford plant in Dagenham. We take a look inside and explore some of the facts & figures behind the site.
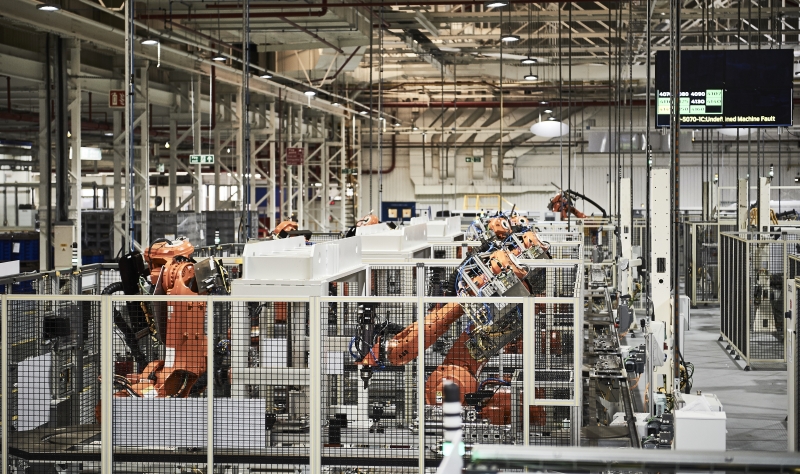
Picture: Ford of Britain
Ford built 11,000,000 cars in the UK before shifting its focus to engine production. Since 1984, more than 44,000,000 engines have been built by Ford in the UK.
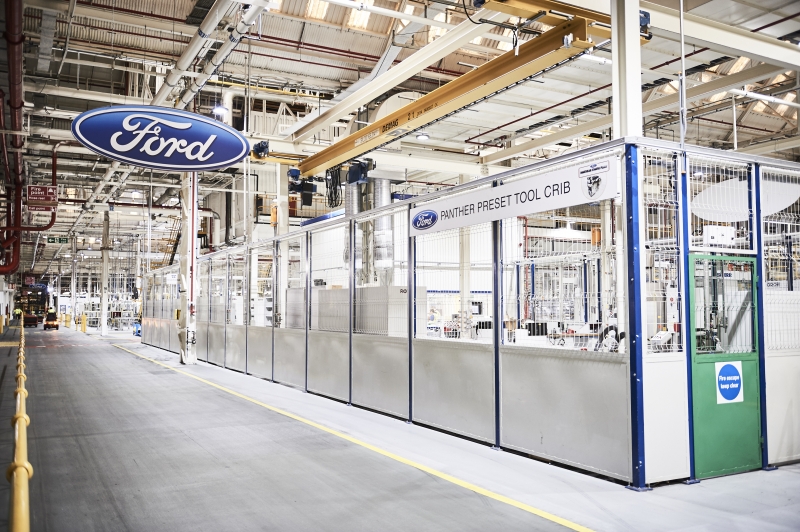
Picture: Ford of Britain
It takes about an hour and a half for an engine to be manufactured and every 28 seconds, a finished unit reaches the end of the line.
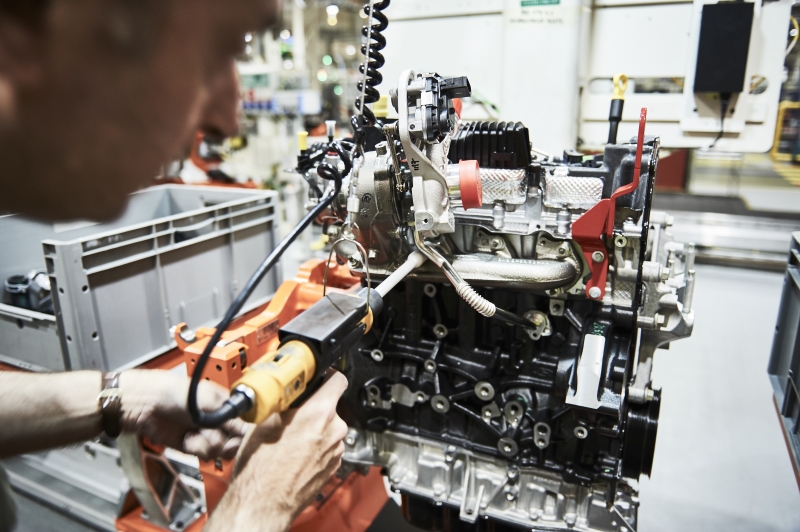
Picture: Ford of Britain
The ‘Panther line,’ produces the EcoBlue engines that go on to power vehicles including the Ford Transit, the best-selling commercial vehicle in Europe since its launch in 1965.
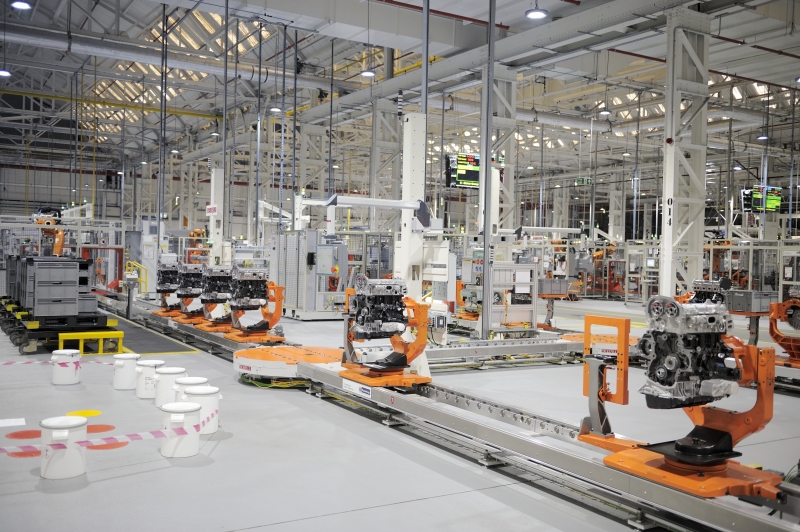
Picture: Ford of Britain
LED lighting is used throughout Dagenham, reducing energy consumption by 750,000kWh a year – enough to power 7500 houses for a week.
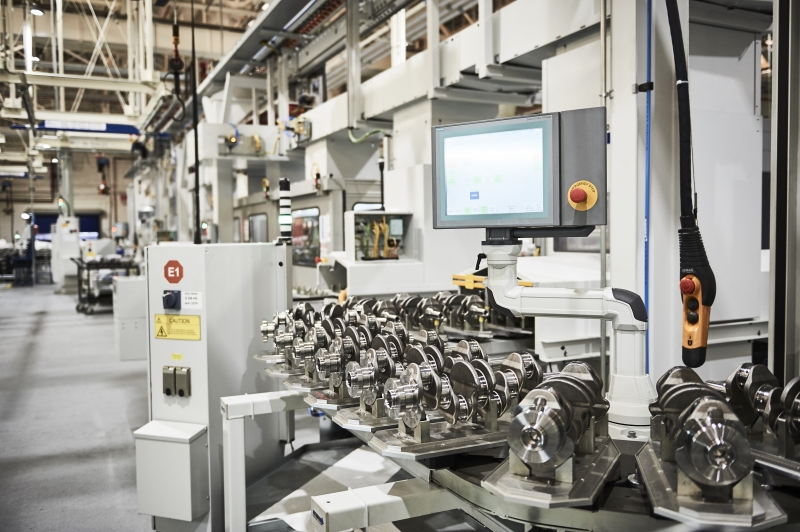
Picture: Ford of Britain
Crankshafts wait to be fitted to the EcoBlue engine. Each component is analysed both digitally and by human hand to ensure quality consistency.
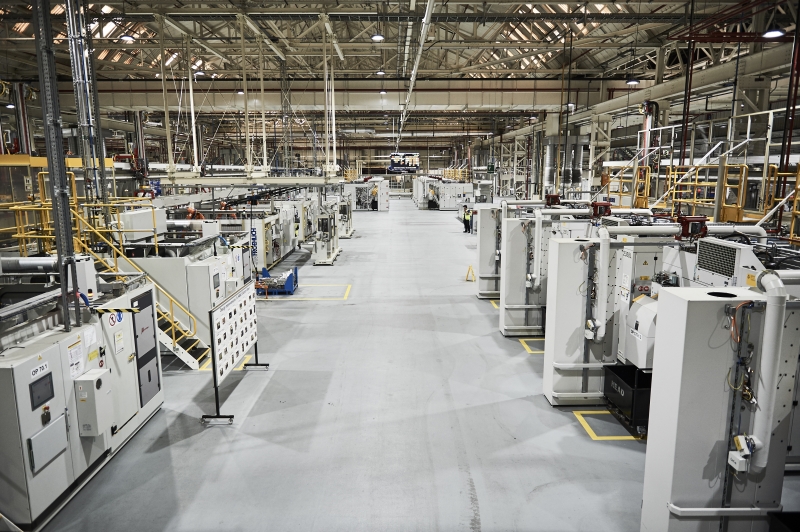
Picture: Ford of Britain
The Dagenham plant has modernised at a rapid pace since it was founded in the 1930s. The lines are clean, efficient, safe and optimised for collaboration between the dextrous human hand and infallible digital systems.
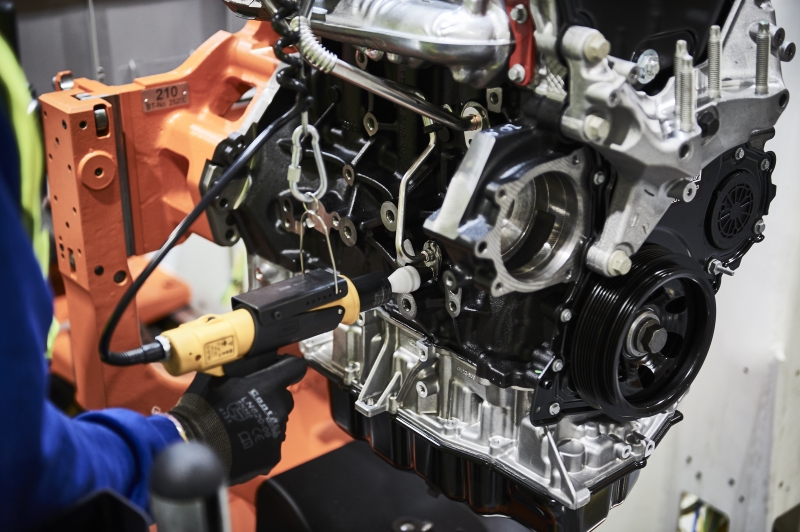
Picture: Ford of Britain
The Ford Apprentice scheme has the widest range of roles on offer from any major manufacturer. Many managers at Dagenham started at Ford as apprentices, including current manufacturing manager, Chris Woolacott.
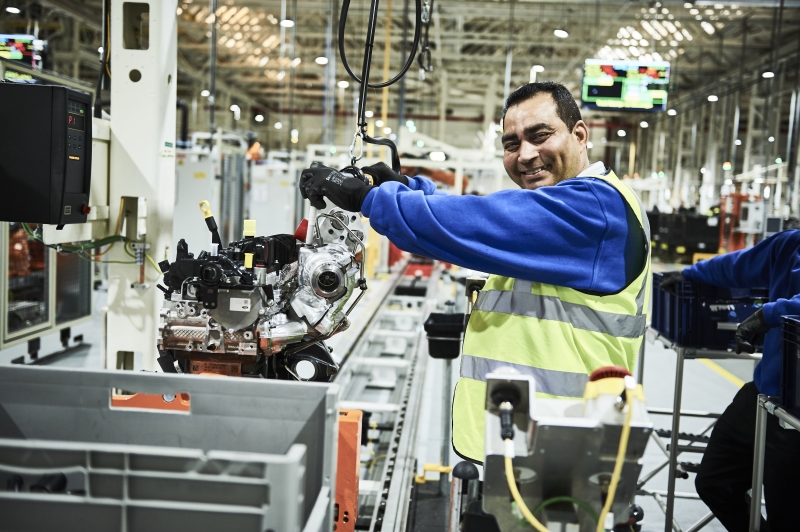
Picture: Ford of Britain
CEME is the Centre of Engineering and Manufacturing Excellence, and it is located on the Dagenham estate. It is a vocational university covering 25,000m2 and has education facilities for two thousand students. Most apprentices undertake an 18-month course at CEME before moving to their dealership, technological centre or plant to continue their training.
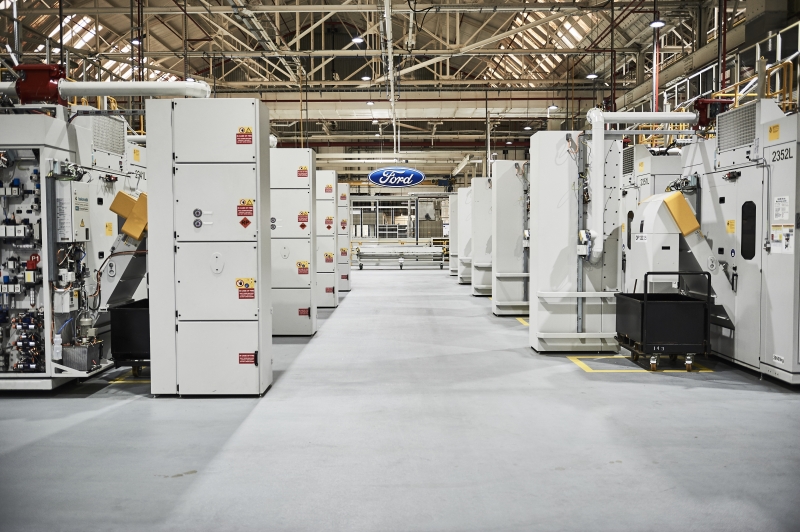
Picture: Ford of Britain
Drones in the factory? Well, yes – Ford employees are now using cameras mounted on drones to safely and efficiently inspect high-rise gantries, pipework and roof areas at the Dagenham Engine Plant. Maintenance staff can thoroughly inspect each area in just 12 minutes.
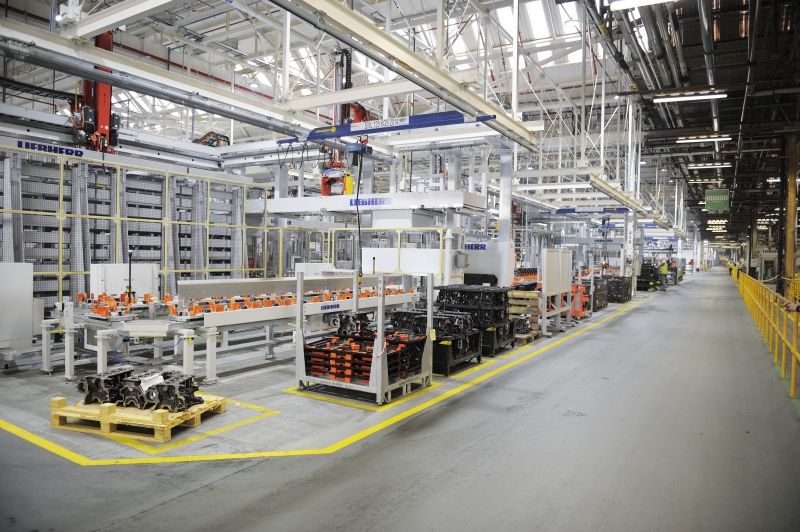
Picture: Ford of Britain
The Dagenham Diesel Centre was opened in 2003 by former Prime Minister Tony Blair. It still produces nearly 1,000,000 engines a year and is 100% wind powered, thanks to its three wind turbines – each turbine produces enough energy to power 1,000 homes.
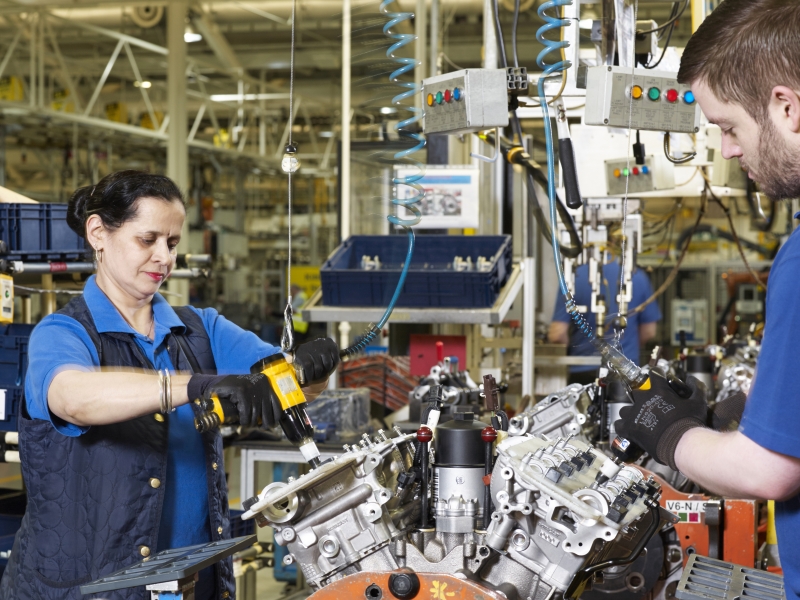
Picture: Ford of Britain
Ford runs various projects that encourage more young people, particularly girls, to consider careers in STEM subjects. This includes supporting engineering challenges, such as Greenpower Trust, Formula Goblins and Formula24, to Primary Engineer and First Lego League events.
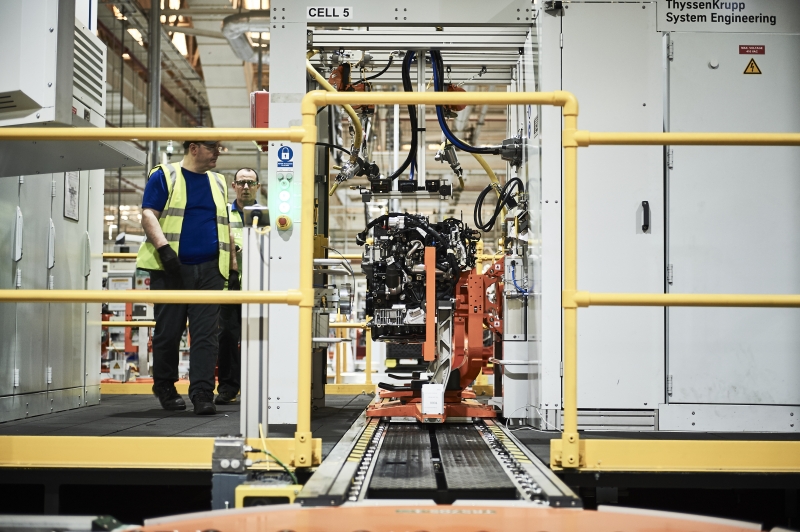
Picture: Ford of Britain
Ford directly supports the Primary Engineer programme, which aims to encourage primary-school-age children into engineering careers. This includes hosting events at its Technical Centre where students from local schools take part in a competition to showcase electric vehicle projects they had worked on for the previous eight months of the academic year.
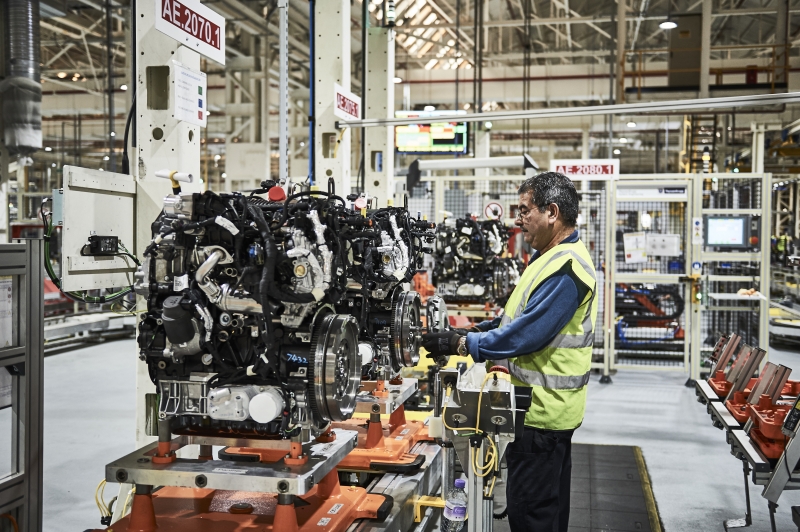
Picture: Ford of Britain
Engines manufactured at Dagenham are exported around the world and shipped to Belgium, Germany, France, Italy, Turkey, Australia, Argentina and Japan.
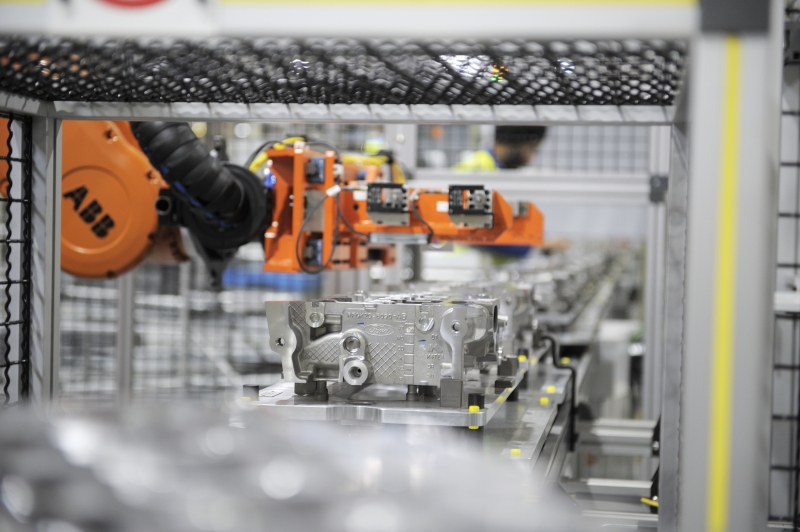
Picture: Ford of Britain
Ford is one of the few manufacturers to have a positive gender pay gap – women earn on average 2% more than male colleagues. Ford Motor Company is one of only 230 companies across the world to be listed in Bloomberg’s 2019 Gender Equality Index, which recognises companies that demonstrate their commitment to female advancement and workplace equality.
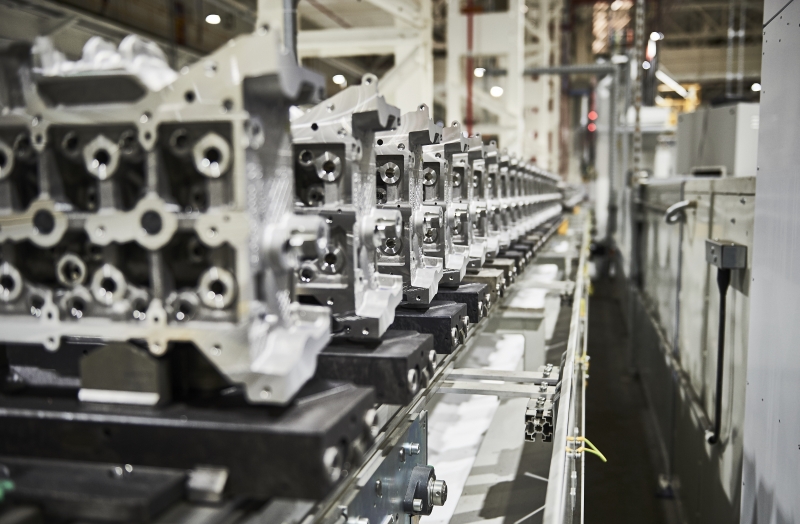
Picture: Ford of Britain
The Panther engine plant at Dagenham is more than a mile long if you trace it from start to finish.
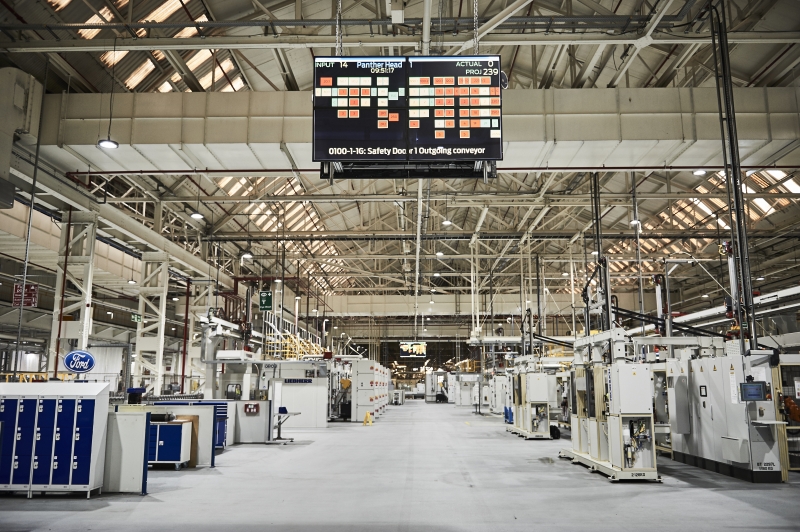
Picture: Ford of Britain
In 2018 Ford announced it had hit its global manufacturing CO2 emissions reduction target eight years early, a reduction of more than 3.4 million metric tons. Ford’s energy conservation programme played a major role in achieving the goal, including paint and other process improvements, LED lighting, plant consolidations and new energy-efficient facilities.
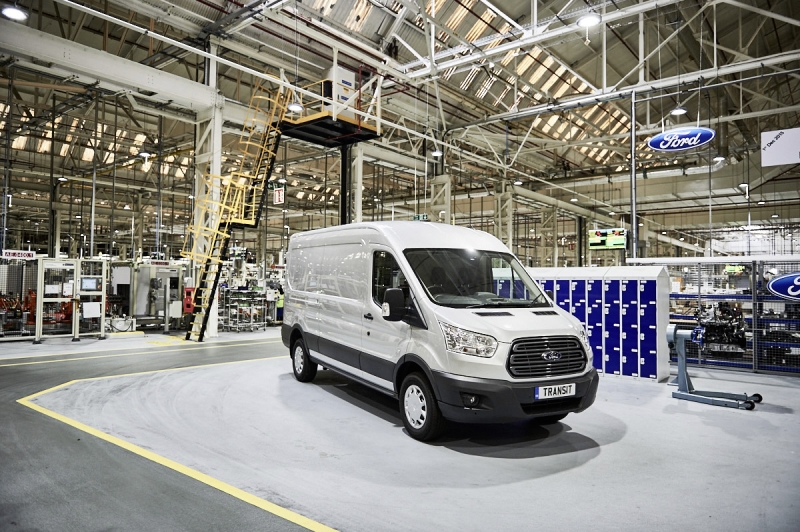
Picture: Ford of Britain
We would like to ‘See Inside’ your factory and share some insight about the investment, growth and future plans you have – if you wish to be featured, please get in touch on hello@zenoot.com