2 minute read • published in partnership with 1st MTA
Automation equipment manufacturer and metrology company join forces
Robotic machine tool tending cells manufactured by Halter CNC Automation, which are sold into the UK market by Salisbury-based 1st Machine Tool Accessories, are being offered with the integration of a coordinate measuring machine (CMM) from Mitutoyo. It follows the automation company’s philosophy of extending its robot cells with additional functionalities.
Mitutoyo CMMs are well suited for incorporation into Halter cells, although almost any make of measuring machine can be supplied to suit a customer’s preference. Alternatively it is possible to network an existing CMM on the shop floor. All installations may be configured for 100% or sample inspection.
On the Halter stand at the AMB 2022 machine tool show in Stuttgart in September, a HALTER Universal Premium 25 LoadAssistant was seen automatically loading billets into a CNC lathe and unloading turned components. Using the same Fanuc M-20iD robot with double gripper, the parts were transported to a Mitutoyo MiSTAR 555 CMM for inspection.
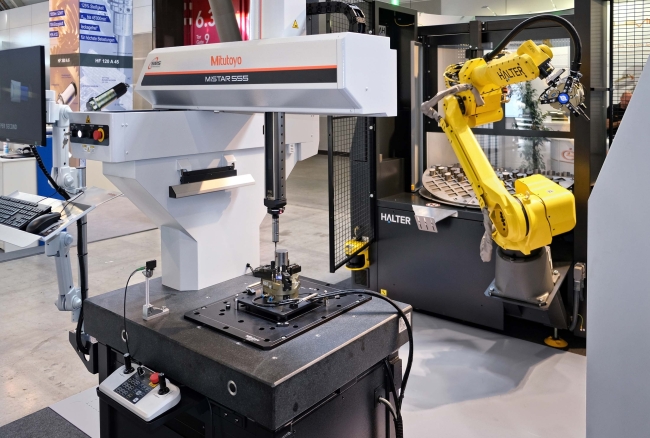
Automation equipment manufacturer Halter and metrology company Mitutoyo have joined forces to help customers improve productivity / Picture: 1st Machine Tool Accessories
Measurement data was continuously fed back to the lathe control so that offsets could be applied if component dimensions started to drift out of tolerance. If production cannot continue, the Halter equipment is instructed to stop load / unload while the problem is resolved.
Halter’s business development manager Rik Peer, said: “We have been supplying CMMs with our cells for about four years, working with a number of different sources, but the installations were specials and required bespoke integration. Cooperating with Mitutoyo means that we now deliver standard solutions for machine tending and in-cycle inspection of turned or prismatically machined parts, so we can offer integrated component measuring at lower cost.
“We already supply many peripheral items to enhance the functionality of our LoadAssistants, including conveyor handling, deburring, washing, marking and component orientation. This latest metrology option therefore fits neatly with our desire to provide maximum flexibility for our customers, helping them to manufacture more cost effectively and win new business in a competitive global market.”
Catherine Kelly, general manager at 1st MTA, added: “Halter’s compact robot cells can tend any make of lathe or machining centre, regardless of age and type of control. They are ideal for subcontractors producing a mix of small to medium-size batches, as a system can be changed over in less than five minutes. Most users worldwide, including a couple of dozen in the UK, report a return on investment of between five and 18 months. With the addition of integrated metrology, payback should be even quicker and we are very pleased to be able to offer the new CMM option.”