4 minute read • published in partnership with 1st MTA
Bowyer Engineering sees 3 month ROI from workholding investment
Bespoke special purpose machine manufacturer and CNC machining subcontractor Bowyer Engineering has purchased its first magnetic workholding equipment, an Italian-made component clamping system from Tecnomagnete supplied through sole UK agent 1st Machine Tool Accessories.
The £4,000 investment paid for itself within the first 12 weeks, according to the subcontractor’s production manager, John McNab. It is significantly reducing the cost of machining steel plates for vehicle exhaust welding rigs, helping the company to address the ever increasing call from its customers for savings.
Called MillTec Grip, the permanent electro-magnetic workholding arrangement for use on machining centres and milling machines uses a double circuit to generate uniform clamping force between the workpiece and the magnetic surface and at the same time between the magnetic system and the machine table. Brief application of an electrical supply is sufficient to activate and deactivate the circuit. A patented feature of the low-profile, frameless clamps is the sealed construction with a monolithic, all-metal top section into which an array of sacrificial, cylindrical pole extensions is screwed for holding down ferrous workpieces.
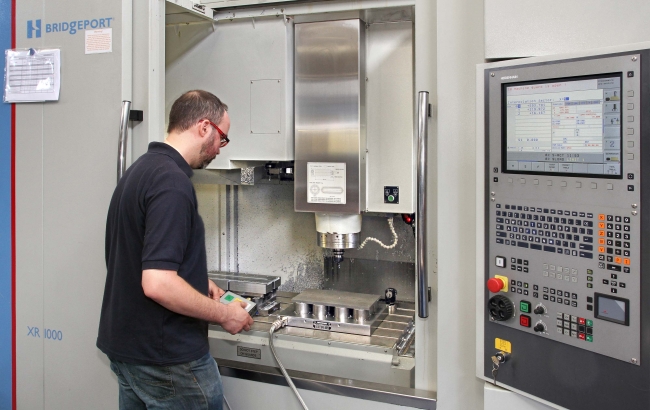
Bowyer Engineering saw a 3-month ROI from its magnetic workholding investment / Picture: 1st MTA
Andover-based Bowyer Engineering, a 35-employee company, is predominantly a supplier to the aerospace sector. It manufactures machines for manipulating and inspecting turbine blades and also mills and turns components for use in aircraft manufacture. A wide range of exotic materials is machined on an array of CNC lathes as well as on Bridgeport 3-axis vertical machining centres and a Matsuura 5-axis model.
One of the company’s other specialisms is the production of jigs for securing vehicle exhausts during automated arc welding. Until recently, the fixtures were manufactured from multi-component fabrications. They were difficult and time-consuming to mill and drill accurately due to their complexity and the need to fixture them at compound angles. Furthermore, a large variety of materials had to be stocked for their production.
So Mr McNab devised a new production route that moved away from machining entire fabrications to milling and drilling steel base plates individually before assembly. It was further decided to standardise on 12 mm thick bright bar, 200 mm wide and up to 4 metres long, which is sawn into billets as required.
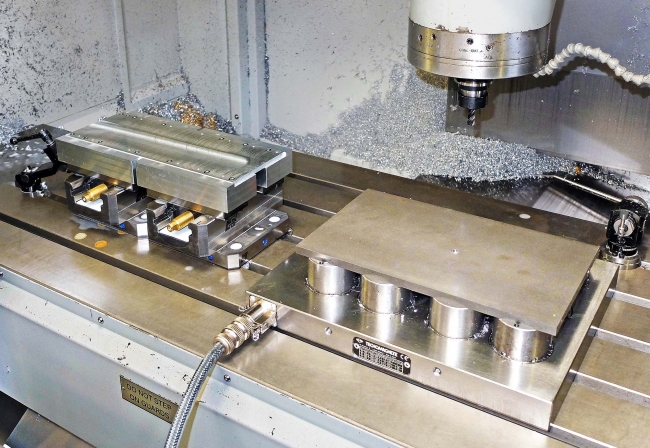
Bowyer significantly reduced the cost of machining steel plates for vehicle exhaust welding rigs / Picture: 1st MTA
Initially, the billets were cut into pieces of different sizes to suit the individual plates. Each had to be clamped on their edges in a vice for machining, which meant repositioning them for a second operation, as it was the edges that were being milled. Production cost was consequently high and it is this method that John is contrasting with the latest, more economical production technique.
It involves clamping a single billet for profiling a nest of variously-shaped base plates by milling to depth around their profiles, followed by drilling. This presented its own difficulties, however. A conventional fixture would have created a dead zone around the periphery caused by interference with the spindle, reducing the yield. Bowyer Engineering’s zero-point workholding equipment would have introduced long idle times, as it would have been necessary to attach pull studs to the underside of each billet to provide security for heavy milling.
As McNab put it, “Spindles turning means spindles earning.” So he set about finding a quicker method of clamping the billets without compromising the ability to machine components right up to the edge.
While at a Matsuura open house in Coalville, where 1st MTA had a stand in the supplier village, he remembered them making a presentation on the Tecnomagnete clamping system. He took particular note, as he learnt that the equipment was new to the UK, having only recently become readily available following the appointment of Salisbury-based 1st MTA as sole agent.
The move by Bowyer Engineering to machining individual base plates rather than complete fabrications provided the ideal opportunity to test out the system, as a billet can be clamped on one face, leaving the remaining five free. Brief consideration was given to vacuum workholding, but the many holes in the base plates made this method unworkable.
A Bridgeport XR1000 3-axis VMC with 12,000 rpm spindle, through-tool coolant and a 30-tool magazine on the shop floor in Andover has been earmarked for the project.
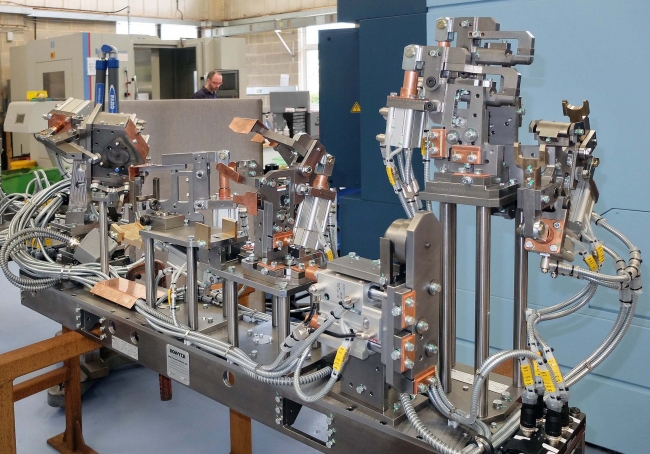
A Bowyer Engineering jig for supply to a subcontractor in the automotive supply chain. It is designed for holding vehicle exhaust components in place during fabrication in a robotic welding cell / Picture: 1st MTA
The MillTec Grip magnetic clamping system has been used exclusively on this machine so far, although it could be swapped over to other machining centres on the shop floor including the 5-axis model. Thirty exhaust welding fixtures can be in build at a time, none of which is the same and each can contain up to 100 plates, so the machine is kept busy.
John explained, “The magnetic workholding and nesting technique substantially reduces the cost of producing every base plate.
“We produce the cutter path quickly using a custom-designed template in EdgeCam that recognises recurring features.
“If the MillTec Grip does not happen to be on the Bridgeport, it is quick to fix it to the table by connecting an electric current, which is then switched off. Securing the steel billet onto the magnetic pole extensions is even faster and extremely secure.
“The magnetic workholding station is positioned at one end of the machine table, allowing another clamping arrangement to sit alongside it for machining other types of component, resulting in maximum versatility.”
Bowyer Engineering also makes welding and other fixtures for manufacturing different products such as off-road vehicle frames and boiler housings. Its new method of making such jigs will expand business opportunities in this area. Moreover, the company is already successfully using the magnetic clamping system to streamline production of a range of subcontract parts for the aerospace, oil and gas, medical and general engineering sectors.
1st MTA provided a high level of technical back-up during initial installation of the Tecnomagnete equipment, advising how best to mount the unit on the machine and position the base plates. Support and advice from the supplier is ongoing, since Bowyer Engineering frequently encounters different workholding requirements as it transfers more and more subcontract machining onto the magnetic clamping system.
Mr McNab concluded, “The whole project has been a resounding success, from concept to operation. Not only have our workholding requirements been met, but the solution has exceeded all our expectations.”