1 minute read • published in partnership with CREAT3D
Case Study: EXTA makes significant cost saving using additive manufacturing technology
Expert Tooling and Automation (EXTA) is a prime solution provider for bespoke tooling and automation systems. Established in 1972, EXTA has earned its position as a highly respected engineering supplier to customers across the globe, working within fields of Assembly Tooling, Special Purpose Machinery and Automation Products to the automotive, aerospace, machine tool and transport industries.
EXTA requires a number of custom jigs and fixtures for in-house assembly line applications. Prior to using additive manufacturing, EXTA would have outsourced the fabrication of this assembly jig on a 3-axis CNC machine. The part would have been produced in four separate segments, assembled using screws and dowels.
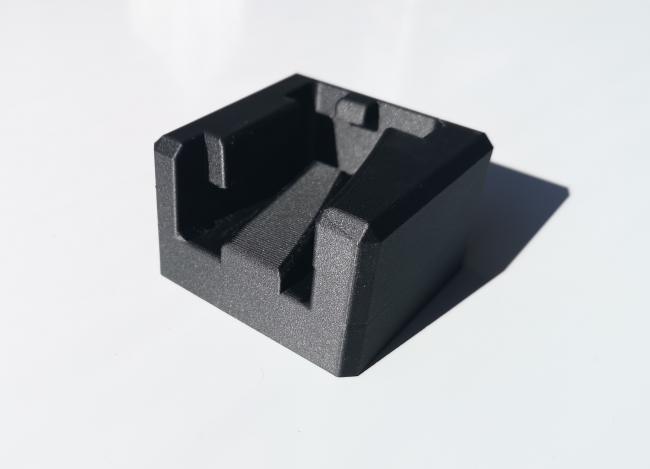
EXTA reduced lead times and made significant cost savings after embracing additive manufacturing technology / Picture: CREAT3D
Since adopting 3D printers, EXTA now design with additive manufacturing in mind. For conventional machining, the design team would have to redesign this part, as well produce technical drawings and manufacturing guidelines. They have not only saved on costs but have significantly reduced lead times.
Return on investment
Traditional fabrication – cost of £300 per part, using CNC machining
3D printing – cost of £10.07 per part
Cost saving – 96% cost saving
Time saving – lead time reduction from 3 weeks to 10 hours (98%)
Richard Gardiner, Project Manager at EXTA, said: Using 3D printing significantly reduces lead time from design to final part, minimising the need to involve internal purchasing and goods-in departments, as well as outsourced fabricators. As we design for additive manufacturing, it also allows us to produce a better fit and functioning part than required, so we save hours by not having to create 2D drawings.”