4 minute read • published in partnership with Flowlens
Case Study: Flowlens strengthens DD Scientific’s manufacturing efficiency through data visibility
DD Scientific is a manufacturer of high-quality, high-performance sensors for the industrial sector. The sensor manufacturer produces a wide range of electrochemical gas sensors that ensures worker safety through the detection of potentially hazardous gases within industrial environments. DD Scientific produces sensors for the automotive, medical device manufacturing, heavy-duty manufacturing, and domestic industries.
Rob White, Sales Director at DD Scientific, describes the everyday operations, regularly involving receiving orders from clients with steep delivery deadlines. These deadlines require some manufacturing flexibility, stock management, and extensive production scheduling to fulfil their short lead times.
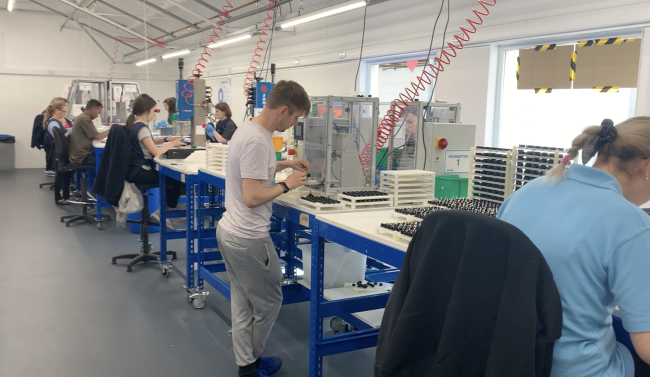
Flowlens helped DD Scientific strengthen its manufacturing efficiency through better data visibility / Picture: Flowlens
Rob and Alan Rex, Operations Director at DD Scientific identified key challenges in their existing systems and processes:
• A cumbersome, older production and stock management system that distorted the manufacturing data capturing process and couldn’t guarantee operational visibility
• Developing flexible production schedules to meet the fluctuating demand cycle and short lead times from customers
• Managing inventory and work orders, and gaining insight concerning stock-outs that affect production cycles
• Connecting the sales, marketing, and decision-making teams with shop-floor workers to enable collaboration
• Reduced productivity is caused by the entry of manual manufacturing data processes and a lack of visibility into production cycles
Choosing the right digital transformation solution
To deal with these challenges, DD Scientific (DDS) required a user-friendly material requirements planning (MRP) solution with the capability to simplify and optimise its manufacturing processes.
Rob continued by stating that the solution they required must be user-friendly, to ensure everyone from the top floor to the shop floor could take advantage of it.
The ease of the process of porting or transferring manufacturing data from DDS legacy systems to the new platform was also key. The chosen solution needed to include extensive support from the service provider to ease the transition process.
Finally, the solution needed to be capable of delivering comprehensive data-driven analytics and data visibility to optimise sales, stock management and the production process.
Rob White commented: ‘If we don’t get our production scheduling right, then we miss orders and that leads to unsatisfied customers. If we haven’t got our stock right, and we don’t get our stock right then we would not have enough parts to manufacture products on time, or in some cases, we’d have too much and therefore working capital will be affected. We found a great deal of limitations with our previous system. So, we looked for something that could solve many of our operational challenges.’
Optimising DD Scientific stock management strategies and improving manufacturing efficiency with Flowlens
After researching their MRP software options, DD Scientific chose Flowlens due to the production scheduling, data aggregation, and high-performing dashboard systems the MRP solution provides. Flowlens also offered the services of their own onboarding team, to support DD Scientific through the implementation and training process, eliminating risks and shortening the time to value.
By choosing an integrated inventory, production, sales and management solution, DD Scientific was able to improve stock management and material forecasting effectiveness to meet flexible customer demands.
Access to the production schedule and customer demand via its cloud-based portal regardless of location gave visibility across the entire production cycle to improve planning and scheduling processes.
By connecting sales and operations, and everyone involved with the production cycle to one reliable source of information. They team also gained real-time insight into operations across the shop floor and connect everyone to the data-driven information.
From a management point of view, the new approach freed up the time spent analysing unstructured data to ensure DD Scientific could focus on its primary production and customer management activities and meet the specified delivery deadline attached to a customer’s order.
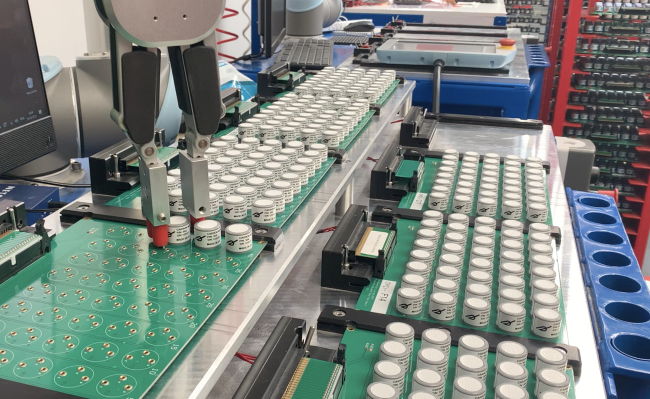
DD Scientific needed a user-friendly MRP solution with the capability to simplify and optimise its manufacturing processes / Picture: Flowlens
Alan Rex, summarised the benefits of the change: ‘The successful integration of Flowlens came with quick returns. The dashboard gave us quick and insightful visibility into our production schedules and ensured everyone was aware of the progress made for every production run.’
‘With minimal training, we’ve been able to optimise projects and job cards that take into consideration material certifications, conformity for materials, and other technicalities. Flowlens now enables us to plan a month’s production schedule in a day.’
Georgi Cojocaru, Production Supervisor added: ‘The new system helps me save time, by visualising all aspects of the production process including customer demand, material information, and production schedule. If I need anything, any information at all, I have it at my fingertips.’
Rob White concludes: ‘The biggest advantage is that it frees up my time. So if I’m not spending hours a week analysing data, and I’m spending that time following up on inquiries or phoning potential customers up, you know, that’s feeding into the growth of the business.’