5 minute read • published in partnership with CREAT3D
Case Study: How KoveDesign solved design & manufacturing problems with 3D printing
KoveDesign is a full service, high technology engineering design consultancy, established in 2011. The Kove Team has advanced engineering specialists across the automotive, motorsports, aerospace and healthcare sectors, totalling over 30 years of collective service.
KoveDesign provides design and engineering services, including end-to-end product creation. Alongside Kove’s work for racing teams and sports car manufacturers, the consultancy also works with a wide range of clients including General Electric, the NHS, Rivian (Electric Vehicles) and Formula E.
As Kove’s services are heavily focused in both design and manufacture, Kove understand the value that Additive Manufacturing brings, and has invested in multiple Markforged 3D printers to deliver robust, strong, quality parts quickly to its clients.
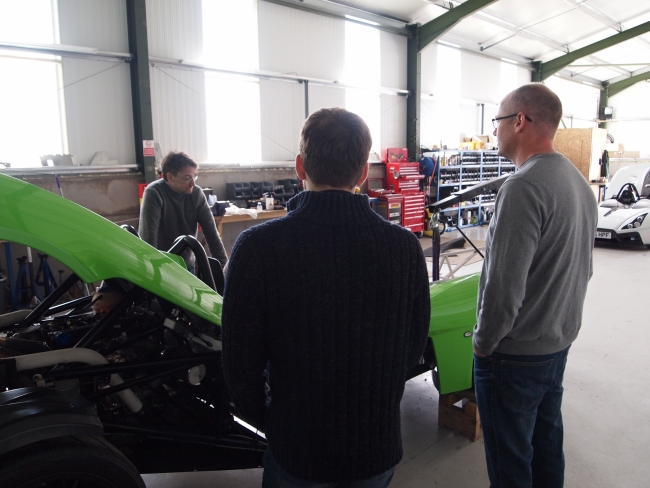
KoveDesign has invested in multiple Markforged 3D printers to deliver robust, strong, quality parts quickly to its clients / Picture: KoveDesign
The 3D printers form part of the total manufacturing and design capabilities at Kove, alongside CNC machining, composite and fabrication shops.
Quite often, a product can be designed for function, but not designed for manufacture.
This is not the case at KoveDesign. One of Kove’s key differentiator’s is designing with manufacturing methods in mind.
Rachel Mackintosh, Product Engineer, says: “Designing a functional part with the intention of it being manufactured is core to the work we do for our clients. Where suitable, we incorporate Additive Manufacturing into the project as much as possible because of the benefits it brings. From the first stages of design, right the way through to considerations in production, it is beneficial to not only shorten time lines, but generate cost savings and ensure we can meet our clients (often very short!) turn around requirements”
Working in close consultation with CREAT3D, KoveDesign invested £20,000 in its first Markforged Composite 3D Printer, with a full installation, training and support package. The printer was integrated quickly into the design workflow, right from initial briefing stage, and used predominately for rapid prototyping, design iteration and functional testing.
In quick succession (at 3 and 9 months), based on the fast return on investment that Kove saw from the first 3D printer, came additional investment in two further machines from the Markforged Onyx desktop series (2x Onyx One 3D printers). These machines were needed to provide extra production capacity, as the applications had deepened into end-use parts and components, not just prototyping.
Single technology, multiple value generating applications
The first applications for the Markforged 3D printer were design-led, with prototyping and product testing the main focus points. However, very soon after integrating the technology, Kove realised further potentials of the equipment, and now a farm of Markforged Additive equipment is used for multiple applications, generating new revenue streams for Kove, as well as cost and time savings for its clients:
Today’s uses of Additive Manufacturing at KoveDesign include:
• Proving and testing prototypes
• Proving new design with product iteration
• Rapid prototyping for clients to test products
• Validating prototypes without the expensive step of machining or tooling
Producing low volume, supply-ready components
Clients now request 3D printed parts
A further positive change that this high use of Additive Manufacturing has seen, is that clients are now requesting 3D printed parts, or request that their design incorporates 3D printing. Clients are changing drawings to reflect the requirements for Onyx (the Markforged Nylon based material), and they are adapting designs to be 3D printed. Rachel adds: “The most consistently supplied parts in particular within our Automotive clients are now 3D printed”.
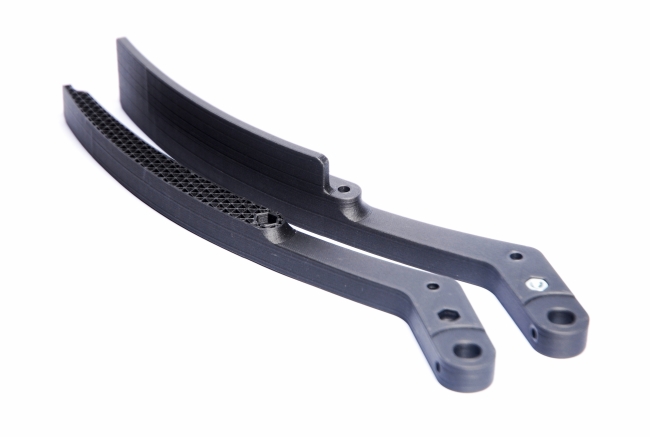
Additive Manufacturing is now deeply embedded at KoveDesign, helping to enhance its service, agility and design capabilities / Picture: KoveDesign
Fast turnaround times with enhanced part performance
Using 3D printing has enabled fast turnaround for Kove’s clients. Rachel concludes: “We can quickly solve our client’s design or manufacturing problems with a workable solution. By using Additive Manufacturing, we are able to produce high tolerance pieces, fast.”
Furthermore, the technology lends itself to more complex designs, single parts instead of assemblies and enhanced functionality “Two of the best features of the Markforged 3D printers is the excellent surface finish that the material (Onyx – Nylon with micro Carbon Fibres) produces, which is essential for our clients, as well as the ability to encapsulate inserts during the print process. It’s a very powerful tool” highlights Peter Kent, Composites Director at Kove.
Elemental Throttle Pedal
Peter Kent, Composites Director at Kove explains the reasons for, and benefits of, 3D printing this end-use component. “The throttle pedal we have produced for the Elemental car by using the 3D printer has a number of benefits. It is lighter – about a third of the weight of the previous pedal – which was made of aluminium.
“A further benefit is the speed and part count. We have removed processes and simplified production by making the component into a single part. This, therefore, removes the risk, making part production easier and simpler. We have taken the complexity out of the part and encapsulated the nut, removing the need to tap in a thread.
“What is exciting about the part is that you can encapsulate the nut. By stopping the printer during the production of the throttle pedal, the nut can be placed in position and the printer restarted in less than a minute. This can be all be done at the same time as creating a part which is as stiff as the previous part.”
Elemental Throttle Pedal
Traditional fabrication
Material: Laser-cut, weld and anodise, Aluminium
Lead time: 2 days +
Cost: Approx. £100
3D Printed Elemental Throttle Pedal
3D Printed
Production method: 3D Printed in Onyx (Nylon with micro Carbon Fibre). Nut embedded into pedal during the printing process
Lead time: 8 hours. Lead time saving 83%
Cost: Approx. £100. Similar cost to the traditional form
Additive delivers Kove its competitive advantage
Additive Manufacturing is now deeply embedded in KoveDesign’s capabilities and this is what creates its leading service, agility and design capabilities, standing Kove out from other engineering consultancies.
Speed to respond to client design and manufacturing issues, providing a functional design that can be produced, at low cost and quickly, sees Additive Manufacturing continuing to expand as a service and capability at Kove.