5 minute read • published in partnership with CREAT3D
Case Study: How Matter embedded 3D printing technology into its design, prototype and development workflows
Matter, the product design consultancy based in Bath, was established in 2003, with the aim of solving client’s design briefs through creativity and innovation. Matter is committed to making a difference and achieving a positive future. Its work covers industrial design, packaging design, foresight, strategy, concept visions, visualisation and prototyping for a huge range of products and experiences. From start-ups to blue-chip internationals, the inspirational team at Matter work on everything from furniture to premium chocolates, alcoholic beverages, to beauty products and consumer product packaging.
Having come from a background and culture of design, ex Dyson employees, Creative Director, Matt Wright and Senior Maker Lead, Jonathan Sturgess, place passion and creativity at the heart of every design that Matter delivers. With a wide range of clients, from different industries, Matter work on a varied range of projects and briefs, and one of their key strengths is their agility and ability to deliver high-quality results, quickly, through the use of in-house 3D printing. Combined with partnering with a wider network of engineering, manufacturers, brand gurus and digital developers, Matter delivers tangible and meticulously iterated design.
To be able to deliver excellent quality results to clients’ design briefs, Matter’s Design Team need to access a whole suite of technologies which enable them to design, iterate and produce. Whilst the team have been using 3D printing since they began their careers, the key was finding and integrating the right piece of equipment into their workflows.
Integrating Formlabs Form 3 SLA 3D printers into Matter’s workflow. The Form 3 provides an excellent design development and prototyping capability and is used as an additional design tool in the workshop, alongside CNC, laser cutters, vac-forming equipment, lathes and handmade techniques.
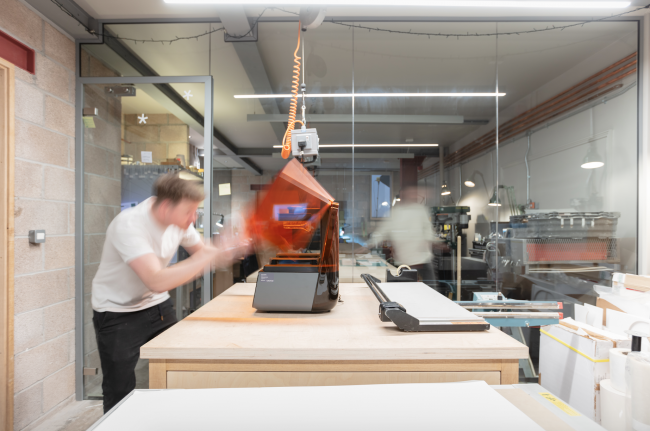
Matter’s work covers industrial design, packaging design, foresight, strategy, concept visions, visualisation and prototyping for a huge range of products and experiences / Picture: Matter
Matt Wright, creative director at Matter, said: “We are so impressed with the user experience and the results, that we plan to have a suite of Form 3s running various resins to add capacity and flexibility to our prototyping output. We’ve recently added a 2nd printer which integrated so easily to an already super busy workshop”
Versatility of uses, with very little finishing
3D printing has long been a core function to the design team at Matter. When previous older and more expensive Additive Manufacturing equipment was reaching the end of its life, and becoming cost-prohibitive to maintain and run, Matter started the process to look for a replacement. One of the key drivers was the ability to print in clear resin, with a high-quality finish. Many of their models are organic in shape and require several stages of iteration, so the 3D printed versions need to be robust enough to handle and test, as well as require little finishing.
Having worked with CREAT3D during the research phase, the Formlabs Form 3 was chosen as the best fit. The Form 3 is now used from very early design stages, to bring the product to life as soon as possible, as well as in later working methods for production. The versatility of the printer, producing high-quality detailed parts with smooth surface finishes, in a range of materials, lends itself to the flexibility needed for a wide range of clients and design briefs.
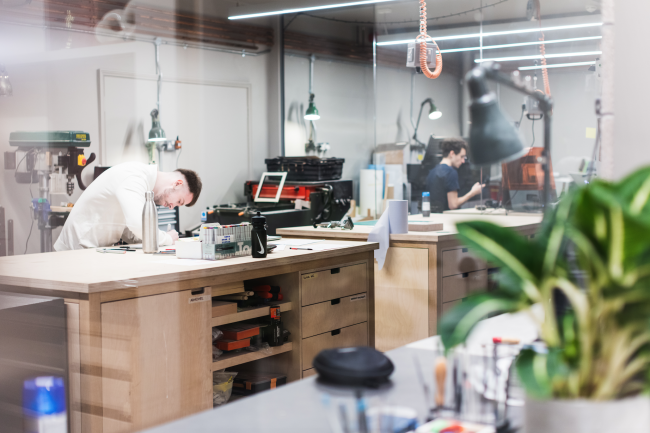
Working with CREAT3D during the research phase, Matter chose the Formlabs Form 3 as the best fit for its needs / Picture: Matter
Jonathan Sturgess, senior maker lead at Matter, explained: “The Form 3 has enabled us to make high-quality clear parts, and also patterns for silicone moulds that need far less finishing than our previous 3D printer, or any of our other rapid prototyping technology would have done. The turnaround from CAD to a finished model took around one-third of the time it would have done using the machine that the Form 3 has replaced.
Although the print times are not the quickest out there, the quality of surface finish and reduction in post-process hours, more than make up for it”
More control > quick response > better results
One of the key benefits the Form 3 has enabled, is the ability for Matter to have more control over projects. To ensure the success of designs, Matter like to understand all stages, from concept to iteration through to production. Having the Form 3 in-house enables the team to maintain a watchful eye over all stages and allows agility within a faster workflow.
Jonathan highlights: “We once set a print off, and the design team came running in, saying hold off! A last-minute client amend was made to the design file, the printer was re-started and the outcome was saving not only time, but money, and the end result was a better iteration. Having a Form 3 has made building clear parts a fraction of the cost and around twice as fast for most jobs”

Clear resin 3D prototype on the build platform of the Formlabs Form 3 3D printer / Picture: Matter
Reduced design costs
With low operating costs, the Form 3 has greatly reduced costs. Previously, parts would have been sent out to print bureaus, or been printed on the older AM technologies. With both of these options, Matter experienced both higher purchase costs, and post-processing costs, with extended lead times. The parts required a lot of finishing before they could progress to the next design phase, which meant individuals would spend more time manually preparing prints, instead of working on design projects.
Now, models are printed on the Form 3, in a matter of hours. The process is cleaner, faster and more efficient, with the product coming off the printer needing minimal attention.
Jonathan added, “For us, the difficulty has always been printing high-quality clear parts at an affordable price. The Form 3 represents amazing value and is a dream to use and maintain. It is now a regular part of our process on all sorts of briefs.”
Enhanced product development
Printing clear models on the Form 3 has been incredibly important to specific design projects, for fast and accurate design iteration and development. The Form 3 played a huge role in the development of a healthcare project.
Sukha, was a design exploration to engage more women in positive HPV screening experiences, producing end products that tackle this important element in women’s health by breaking down the barriers that prevent women from attending their cervical screening. The clear 3D printed models, allow for detailed testing and analysis, for example filling with coloured liquids to test flow and functionality.
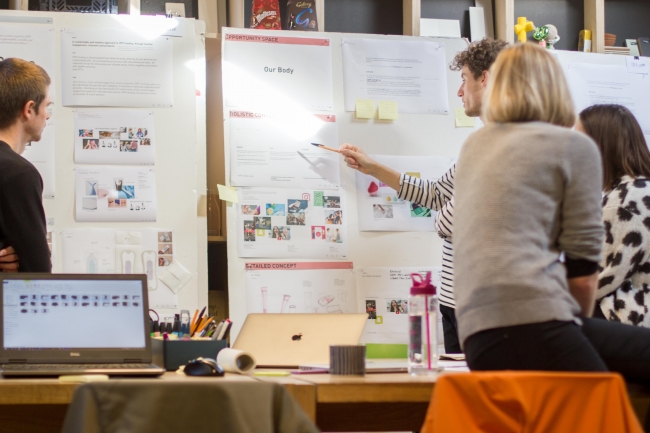
Multiple Form 3s have been embedded into the design process at Matter, used predominately for prototyping / Picture: Matter
Healthcare Product Development
Printing multiple iterations in clear resin on the Form 3 was critical to the project’s development. Having the 3D printer in-house provided immediate feedback, enabling same-day assessments, revisions and development. With very little post-processing required, time was spent on product development rather than model refinement.
The future moves 3D printing to more functional applications
The Formlabs SLA printers are already embedded in Matter’s workflow. Moving forward, the team will integrate more of the functional resins that replicate engineering materials such as Polypropylene to have more functional models and even end products.