5 minute read • published in partnership with FANUC
Case Study: Moulding success into UK manufacturing
The adoption of industrial robotics in UK manufacturing is still seen as divisive among industry. While it is widely accepted that technology has an important role to play, there are still a number of UK manufacturers yet to fully take advantage of the latest innovations. Some argue that adoption of industrial robots can lead to people being replaced, but one UK manufacturer, Advanced Plastics, is proving that this is not the case.
With staff growth reaching an impressive 83% in five years, Advanced Plastics continues to develop thanks to continued investment in both technology and skills in recent years. This use of technology has now seen the award-winning injection moulding manufacturer become a success story for UK manufacturing, and establish itself as a supplier to a number of OEM and tier one companies across the HVAC and automotive sectors.
New technology
With more than 200 people now working at Advanced Plastics, the technical injection moulding manufacturer utilises a combination of the latest technology and extensive experience of its engineers to provide robust solutions for client requirements. Moulding a diverse range of products, from gas boiler front panels, to automotive interior, exterior and air filtration components, Advanced Plastics has built up a healthy list of blue-chip clients over the years as it looks to continue its impressive growth.
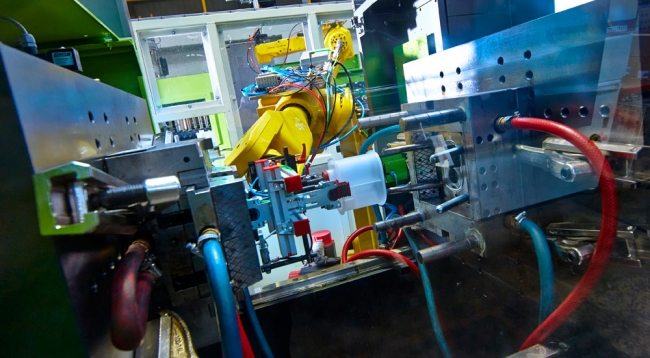
Advanced Plastics has seen staff growth reach 83% in five years thanks to investment in technology and skills / Picture: FANUC
One of the reasons for this success is the company’s adoption of the latest industrial technology, including automated systems and industrial robots. The investment has allowed them to grow at a pace that may surprise many onlookers, as the automated processes in place ensure a high demand of technically-challenging orders are delivered on time.
Edwin Darling, Process Manager at Advanced Plastics, said: “Our moulding machines produce the parts, but we now use robots to tend the machines on a constant basis, with consistent cycle times and dependable overall equipment effectiveness (OEE). All of our injection moulding machines have a robot, which is situated inside a cell and performs various applications, many with vision systems to provide 100% automated verification.”
82% of the robots used by Advanced Plastics are produced by FANUC. Due to the variety of orders that the company receives, it requires a multitude of different robotic technologies to be able to commit and complete the desired components on time.
As a result, Advanced Plastics has purchased and utilised a number of different systems from FANUC, including the M-10iA, M-20iC, M-6iB and R-2000 series, as well as ROBOSHOT injection moulding machines.
One of the benefits of FANUC’s R-2000 robots is their ability to work with pre-existing automation equipment. At Advanced Plastics, two R-2000 robots work with a moulding machine and deliver the parts to another piece of equipment that help place foam gaskets around plastic components, such as boiler covers. The R-2000 series features high performance capabilities and is perfect for applications involving high payloads. Its compact design makes it an ideal solution for Advanced Plastics, to ensure compact and efficient cell designs.
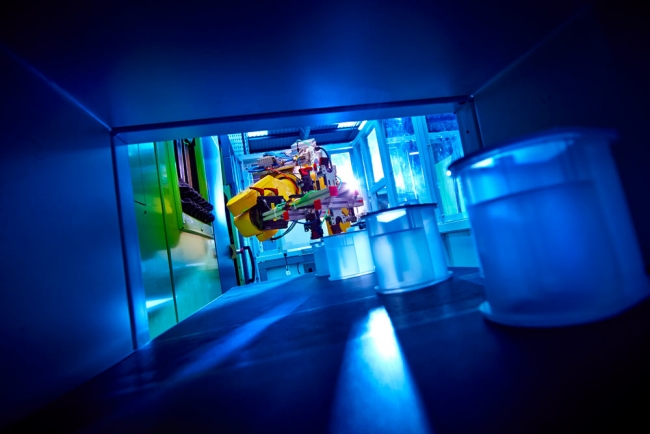
The use of robots at Advanced Plastics enables consistent cycle times and dependable overall equipment effectiveness / Picture: FANUC
Training and upskilling
One of the benefits of utilising FANUC technology is the training service the company provides both at its UK headquarters in Coventry and on-site. Four of the Advanced Plastics team learnt how to service the robots and provide the maintenance themselves, allowing the engineers the opportunity to enhance their skillset and ensuring Advanced Plastics has the tools to become even more self-sufficient as a business.
As a result, Advanced Plastics now mould more than 1,000 products on-site. Each product has its own robot programme, which are all easy to understand and maintain, with one employee operating up to six moulding machines at a time.
Edwin continues: “We have found that FANUC has the most user-friendly robots we’ve ever used and having the opportunity to go down to its headquarters for comprehensive training ensures we are well-placed to manage our operations. The speed in which we are able to complete orders means we can continue to grow and invest in further technology.”
Time savings and future growth plans
One of the robots that has proven to increase the capacity the manufacturing site is able to produce is the M-10iA. Through working with FANUC, Advanced Plastics has moved from a 3-axis robot to FANUC’s 6-axis M-10iA robot. Processes which were complicated and difficult to handle are now automated, including picking up inserts and putting them into the moulds, some of which can reach between 80-90°C making them unsafe to handle, as well as trimming tab gates from cavities once the plastic has been injected. Additionally, the adoption of the M-10iA robots has seen Advanced Plastics’ effectively double its payload, compared to its previous system, from 6kg to 12kg.
The compact system has also helped the manufacturer improve its cycle time, providing significant time savings over a year, as Edwin explains: “The machines are fast and because they have a constant cycle time, they can provide time savings of two seconds or more each time. While this doesn’t sound like a lot, by reducing the time by one to seconds each cycle, we can save around four to five weeks of time per year. Given the increase in orders that we have received, this time helps us to keep growing as a business.”
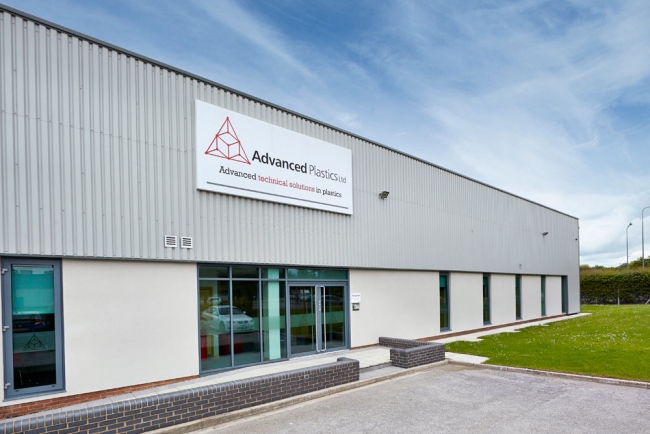
Advanced Plastics employs over 200 people, has doubled its capacity in the last 7 years and continues to invest in the latest technology & automation / Picture: FANUC
As FANUC’s robots come in a variety of different sizes, Advanced Plastics is able to mould a vast range of different products of varying technical difficulty. Currently using FANUC robots that range from 6kg to 165kg all of which are IFT approved, Advanced Plastics are able to fulfil orders for many different components at the same time.
When it moved into its current home in 2012, Advanced Plastics had 16 injection moulding machines. Today, this number has increased to 37, effectively more than doubling its capacity in the last seven years. As it continues to grow, the company is now looking to expand its capabilities with a new car park and warehouse facility, freeing up an additional 40% of manufacturing space.
It is clear that the future is bright for Advanced Plastics. Producing a high volume of components for a growing client roster has shown the benefits of introducing technology and industrial robots over a steady time period. Combining technical expertise with advanced technology has allowed the company to continue its impressive growth in East Yorkshire.