2 minute read • published in partnership with CKF Systems
Case Study: Robot palletising success for a leading global snacks company
CKF has recently designed, installed, and commissioned a new £4million central robotic palletising system for an international snacks manufacturer within its UK facility dramatically increasing productivity, streamlining the operations, and reducing manual handling. The new system incorporating six ABB robots is the latest installation to be successfully completed by CKF on this site.
The cased product which outfeeds from 12 production lines, positioned in two areas of the manufacturing facility, is conveyed on CKF standard ZLP roller conveyors through to a centrally located palletising system. The cases of product are fed via Intralox DARB sortation systems and pre-collated before being palletised by six ABB IRB660 robots with custom gripper tooling. The system has been designed to handle 100 cases per minute and delivers 110 pallets per hour.
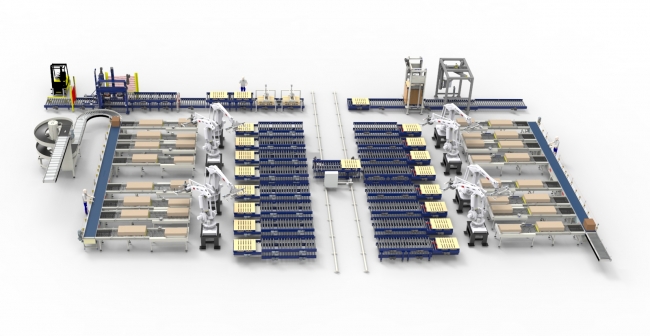
CKF Systems has helped a snacks manufacturer increase productivity and reduce manual handling with a new robotic palletising system / Picture: CKF Systems
CKF are leaders in automated robotic solutions with more than 30 years’ experience supporting different industries including Food & Beverage, Logistics, Pharmaceutical and Automotive. This is the latest robotic system to have been delivered and commissioned by the experienced engineering team at CKF, aiding the clients drive for the improvement and automation of operations within its manufacturing facility.
Pallet handling of both CHEP and Euro pallets is managed through two CKF standard de-stackers, three shuttle cars, two double pallet stackers and two Atlanta arm wrappers with LogoPak 900 series label applicators. The central shuttle car is a dual height system for feeding empty pallets in at low level to the robot cells and full pallets out at high level to meet production throughput. The pallet conveying system is derived from the CKF standard range of pallet conveying equipment. Following wrapping and labelling, CKF interfaces with the site’s Autostore system, delivering the completed pallets to one of two outfeeds into the warehousing facility. The outfeed selection is dependent on destination and desired storage location. Two CKF double pallet stacker machines were installed into the system prior to the stretch wrapping machines to meet customer storage and delivery specifications.
The system is driven on a Siemens S7 platform, with the main controls housed in a five-bay panel, adjacent to the robot system, remote panels provide power and I/O further away in the field. The robot cells are configured to fit within a designated area within the clients’ facility and utilise ABB’s MultiMove application. Safety zoning and safety enclosures delivered using Troax Safety guard fencing, and Hart, fast acting speed-doors. Operator access into the robot cells is gained through Fortress interlocked access doors.
The new system was installed in a number of agreed phases. The case feeds from the production lines are directed to a dedicated side of the central palletising system in line with product type. Of which there are two groups. This provided the opportunity for phased commissioning of the robot palletising system and production handover to suit the clients’ requirements and production demands.
The new multi-million pound system has been delivered to meet the client’s specifications and achieved the planned performance, allowing the client to re-allocate operational staff from what has been a repetitive task, with its associated risks.