7 minute read • published in partnership with 1st MTA
Feature: Automation to boost reshoring in the UK
The recent appointment of Salisbury-based 1st Machine Tool Accessories as UK sales agent for Dutch robotic machine tending systems manufacturer Halter CNC Automation makes available to British machine tool users an extensive range of third-party component loading and unloading cells of the highest quality and reliability. The cells are easy to program and have frequently been shown to out-perform similar equipment offered by the machine manufacturers themselves.
The COVID-19 pandemic has been a trigger for many OEMs and large manufacturing companies to rethink their often-complex supply chains. When China stopped production in early 2020, followed by other countries, manufacturers in Western Europe and the United States were forced to close their factories due to lack of parts. The blockade of the Suez Canal by the container ship Ever Given showed in a different way how vulnerable world trade has become after decades of globalisation.
Do companies still want to be dependent on distant supply lines from low-wage countries? In the coming years, climate policy will ensure that this question remains at the top of the agenda. Transparency regarding the real costs of outsourcing in the Far East will lead to shifts in global supply chains.
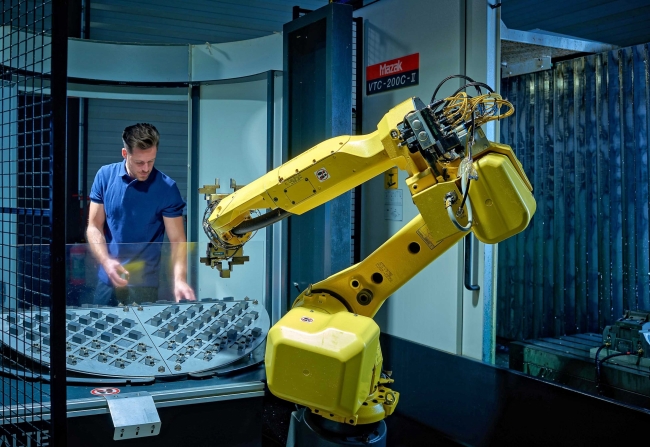
Picture: 1st Machine Tool Accessories/Halter
The playing field for the manufacturing industry is changing as work comes back from low-wage countries. It is creating opportunities for local manufacturing companies, provided that they can respond flexibly to demand and keep their overheads low. Automation and digitalisation are the solution for seizing the opportunities that are presenting themselves in the post-COVID-19 era.
From offshoring to reshoring
The discussion about bringing production back from low-wage countries to the West is not new. Reshoring initiatives were launched a decade ago, aimed at making OEMs aware that the real cost of a product from China or India, for example, consists of more than just the unit price charged by the supplier.
This has become a hot topic, as at the macroeconomic level, growth and employment are crucial. Western countries have seen millions of high-wage industrial jobs disappear since globalisation started 25 years ago. This really dawned on policy makers after the 2008/09 credit crisis. Reshoring creates stable, well-paid jobs.
In the US, since a reshoring initiative started in 2009, well over 600,000 jobs have been created in the country’s manufacturing industry by taking back work from low-wage countries. That is 44% of the total number of industrial jobs created since 2010. The trade war between the US and China has further fuelled the trend towards reshoring and the COVID-19 pandemic will only serve to accelerate it.
In addition, there is increasing pressure from financial markets on OEMs to reduce their carbon footprint. Transport from the Far East plays a major role. It is expected that CO2 costs will increasingly be included in the price of manufactured products. This creates a fairer playing field, as if they are made close to the OEM they become relatively less expensive due to the smaller carbon footprint.
Consultancy firm Roland Berger predicts that the trend in the automotive industry to include the CO2 emissions of suppliers in the total ‘green’ performance assessment will trickle down into the supply chains and spread to other branches of industry. In the future, a CO2 certificate may have to be supplied for each part in a vehicle and that will lead to more local supply chains.
A third trend that favours onshoring is the ever-shorter life cycle of many consumer products. It is causing a shift towards build-to-demand, where suppliers respond quickly and supply the products that are requested by the end customer in a short time frame. In markets with limited product life cycles, the risks of inventories are too great, as is the disadvantage of long delivery times due to outsourcing from afar.
Flexible automation is the key
To reduce the cost of manufacture and compete successfully against low-wage countries, machining companies in the West need to reduce their overheads. They can do this robustly and reliably by automating and digitalising their manufacturing processes to lower the labour cost content of products.
Flexible automation with robot cells to provide unattended running is the perfect solution, not only to reduce costs but also to enable production to be scaled up or down quickly to meet customer demand, especially in view of the increasing scarcity of skilled machinists.
Automation gives SME manufacturing companies the means to respond. Apart from the advantage of lower wage costs and more flexibility, automation is more in line with what young employees expect from their jobs. Setter-operators who are prepared to remove a workpiece from a fixture and replace it with new material dozens of times a day are increasingly difficult for employers to find and retain.
Quality is also improved by autonomous production, which cannot succeed if processes are unreliable. During unmanned running, a chip left in a fixture, a broken cutter or an insert with a shorter service life than expected can stop production. Automation forces companies to view their processes in detail and optimise them where necessary. It is the first logical step towards Industry 4.0.
However, there are mental barriers to its adoption by SMEs, notably the perceived high cost of robotisation, a lack of programming experience and too few integrators for servicing the various potential end user industries. Customers therefore want robot systems that are easy to program and simple to link to existing or new CNC machines and to manufacturing industry software.
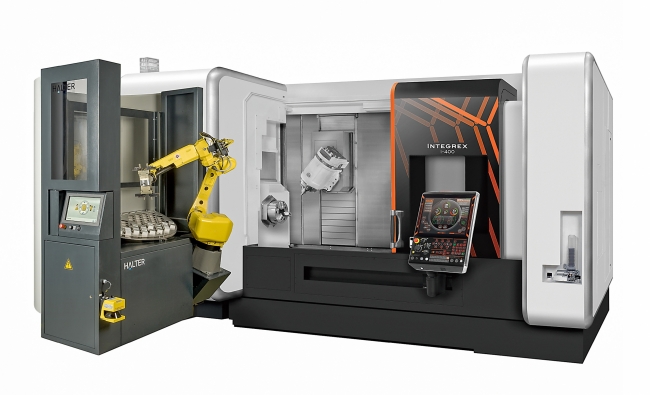
Picture: 1st Machine Tool Accessories/Halter
HALTER LoadAssistants are the answer
With batch sizes becoming ever smaller, coupled with a shortage of skilled operators and machine tools that are too expensive in relation to their output if manually loaded and unloaded, it is clear that automation offers the solution to many of the problems facing manufacturing industry today. HALTER CNC Automation’s plug-and-play robotic machine tool tending systems are perfect for fitting to any make of CNC machine of suitable size at any time, existing or new, regardless of its age and the type of control.
Renowned for their compactness, reliability and the strength of the service and support provided by the manufacturer, both locally and remotely from the Dutch factory, the cells are available in four series for handling components weighing up to 70 kg: TurnStacker for automating workpiece handling in fixed-head CNC turning machines; MillStacker for providing similar functionality for machining centres; Universal, capable of feeding parts automatically for either rotational or prismatic machining; and workpiece-specific solutions.
Nearly 95% of Halter customers across 25 countries report a return on investment within 18 months for their automation systems, with some saying it is as short as five months. So there is much to be gained in terms of extracting greater manufacturing efficiency and profits from either new machine tools or existing models on a shop floor.
Simple programming and operation
The programming software in the SmartControl of a HALTER LoadAssistant is so intuitive that switching to the next batch run takes just a few minutes, minimising downtime and lost production. The manufacturer has a team of software engineers that understands the need to make robot programming easy and fast, whether off-line or at the control on the shop floor while production continues.
Even if a person has no robot knowledge, he or she can be trained to program and operate a cell in just a few hours and it does not matter if a production cycle includes subsidiary operations like deburring, washing, metrology and/or laser marking.
The workpiece table may be replenished with billets or other raw material at any time, even while the robot arm continues loading the CNC machine tool. This is a unique feature of the HALTER LoadAssistant and helps to extract the maximum output from a machine, as the spindle almost never has to stop.
Another facet of these all-in-one automation solutions is that the equipment may be moved easily by pallet truck from one CNC machine to another. The new machine is automatically identified and recalibration is rapid owing to self-centring anchors which fix the robot’s reference position. Operator safety is paramount and scanners are provided that first slow and then stop the robot arm if an operator approaches.
In conclusion
The most important consideration when automating machine tools on a shop floor is the experience and reliability of the automation partner chosen. In this respect HALTER leads the field. For manufacturers in the UK, the extra back-up provided by 1st MTA coupled with its extensive workholding knowledge and product range will prove invaluable.
HALTER’s business development manager Rik Peer, explained: “1st MTA is the first formal sales agent we have appointed in Britain. As our LoadAssistants are fitted to such a broad range of machine tools, we were keen to find an independent agent that nevertheless had in-depth knowledge of the industry.
“We believe we have found that company in 1st MTA, with its long experience of supplying bar feed automation for lathes and a wide variety of workholding equipment and other accessories for both turning and milling.”