4 minute read • published in partnership with Cimlogic
Insight: 10 manufacturing KPIs to track and what they mean to your business
Successful businesses typically rely on key performance indicator (KPI) measurements to evaluate business performance and efficiency, and improve decision-making. Whilst some of these measurements are standard business analytics for accounting purposes (profit and loss, cash flow etc), smart manufacturers include these and other industry-specific measurements as input to data-driven decision-making. Cimlogic shares the the top manufacturing KPIs and how they deliver real business value.
What should you measure? Production rates? Inventory turnover? Availability? With an abundance of data available to manufacturers, it can be so easy to miss key trends, hidden in a sea of data reports. Savvy businesses understand the critical KPIs for their industry and present these in easily understood dashboard formats, allowing dynamic decision making and swift response to underlying trends.
Which manufacturing KPIs matter?
Data collection and analytics tools allow access to so much data it can be overwhelming for a manufacturing director to identify the key KPIs needed for maximum business efficiency and performance. Traditional metrics such as OEE (Overall Equipment Effectiveness) and downtime are valid but have limitations when it comes to evaluating overall manufacturing efficiency and productivity. Additional metrics are needed for monitoring overall business performance accurately.
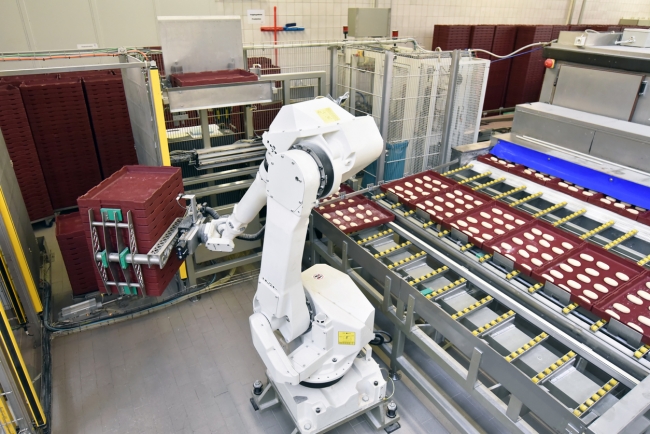
World-class manufacturers should measure and monitor an agreed set of KPIs and use these as input to decision making and strategy / Picture: Getty/iStock
So, which KPIs should you track?
1. On Time Delivery in Full (OTIF)
Are you delivering orders on time to your customers? A critical KPI, as customers will soon walk away if orders are not fulfilled within required timeframes. Are you achieving 100% on-time delivery of orders? If not, do you know why? Most other KPIs are redundant if you lose customers due to non-delivery of products.
2. Production Scheduling
What percentage of production is completed on time? Linked to delivery, this KPI tracks production against target levels and aims to reduce performance issues causing delays. Tracking delivery without production scheduling might not highlight potential bottlenecks in the production process which could be impacting competitiveness (or could you shorten delivery times and stand out from your competitors?).
3. Total Cycle Time
How long is the total cycle time from customer order to delivery? This represents the full time required to convert raw materials into finished goods. Additional KPIs for Machine Cycle Time and Cell Cycle Time might be included as a measure of plant performance, but the total elapsed time from incoming order to customer delivery is a key metric for measuring efficiency.
4. Throughput
How many units (on average) is a machine, cell or line producing over time? (eg xx units/minute). Can this be improved? Is there a significant variance in throughput? A number of factors contribute to this KPI, including machine downtime, shortstops, raw material availability, machine calibrations, maintenance etc.
5. Capacity Utilisation
Are your machines running at 100% capacity? If not, why not? Can utilisation be improved? This KPI enables manufacturers to understand options for increasing production or implementing job scheduling.
6. Changeover Time
Changeover time for shift changes, calibration, new jobs, machine loading/unloading etc all contributes to reduced production capacity. This KPI can help identify bottlenecks and options for improvement eg job types, operator training, maintenance scheduling. When analysed regularly, this KPI can help determine which job types and parts might require process changes or additional planning to proactively reduce changeover times.
7. Yield
Yield is a measure of quality and performance and is at the heart of production efficiency and profitability. Companies should target 100% yield (ie no defective units produced). Yield measurement identifies which processes cause unwanted re-work which in turn affects throughout and total cycle time.
8. Planned Maintenance Percentage (PMP)
Maintenance managers need to have a clear understanding of scheduled/planned maintenance vs emergency breakdown callouts. What is your ideal PMP? Emergency fixes are costly (machine downtime, production line stoppages, increased cycle times) and this metric offers a tangible measure to help allocate resources for preventative maintenance, leading to improved uptime and reduced operating costs.
9. Availability
A crucial KPI for all manufacturers. Downtime costs money, whether planned or unplanned. Analysis of downtime reasons offers vital insight into where improvements can be made, identifying whether machines, operators, shift patterns or a combination of these and other factors are impacting availability.
10. OEE – Overall Equipment Effectiveness
OEE, the traditional manufacturer’s yardstick for performance, availability and quality, has its place, but is deliberately placed at number 10 in this list. OEE should not be measured in isolation, and a high OEE should not be the only measure of manufacturing excellence.
There are other KPIs that didn’t make the shortlist which you might consider, depending on your industry/ production process. Examples such as Scrap (this includes defective units as well as discarded or leftover raw material) help manufacturers identify options for cost reduction and improving product quality. Additionally, Customer Returns offer a measure of product quality and might indicate an issue with the production or quality control process if a significant percentage of products need rework. Inventory Turns is another measurement in lean manufacturing, where keeping inventories low can improve cash flow and allow speedy response to changing customer needs.
The list is not exhaustive but aims to give manufacturers some ideas as to which KPIs are relevant to the production process. World-class manufacturers measure and monitor an agreed set of KPIs and use these as input to decision making and strategy. Cimlogic works with its clients to understand the key business drivers and recommend the best solutions to deliver tangible business value – helping you define and achieve your manufacturing KPIs.