5 minute read • published in partnership with output.industries
Insight: Are you among the 20% of manufacturers doing nothing with digital technology?
Digital technologies can deliver the efficiencies and productivity growth manufacturers need to survive and thrive. Yet, many remain unaware of the opportunities or face barriers to adoption. output.industries has built an intuitive, user-friendly solution that enables SMEs to take that crucial first step.
The Fourth Industrial Revolution (4IR) is the next phase in the ongoing transformation of manufacturing that began more than 250 years ago. Often referred to as Industry 4.0, 4IR takes the mechanisation, assembly lines and computer systems of previous revolutions and adds modern disruptive technologies like internet connectivity, data analytics and advanced automation.
The adoption of these technologies within industry certainly looks to be accelerating. Three in four* manufacturers increased spending on digital technologies over the past 12 months, and one in two** plan to increase their investments in 2023. Yet, there is still a long way to go before the heralded ‘revolution’ reaches critical mass.
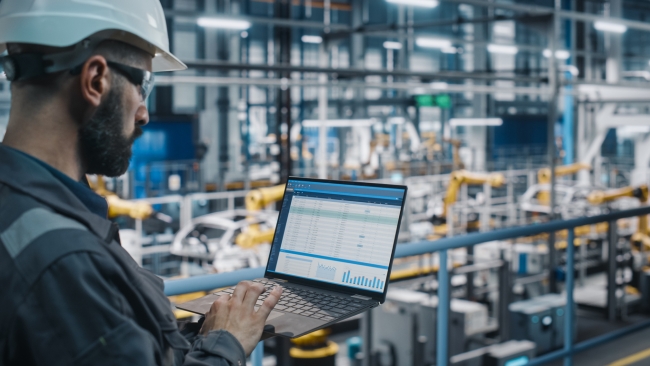
Digital technologies can deliver the efficiencies and productivity growth manufacturers need to survive and thrive / Picture Getty/iStock
There are four phases of 4IR transformation, according to manufacturing trade body, Make UK:
• Pre-conception (doing nothing) – Companies are unaware of the advantages of investing in and adopting digital technology or face barriers to do so.
• Conception (thinking about doing something) – Companies are assessing what new digital technologies can offer to their business and how to apply them successfully.
• Evolution (transforming) – Companies are capturing and analysing data and implementing changes to their processes based on these insights.
• Revolution (profiting) – Companies are using new digital technologies to change how they add and gain value and how they interact with customers and suppliers.
Encouragingly, one in two (49%) manufacturers are currently in the evolution phase and around one in 10 (8%) are in the revolution stage. In 2018, those figures were 39% and 4%, respectively. The pace of adoption is clearly increasing, just nowhere near fast enough.
“This data shows a divide with most manufacturers trapped in either the early ‘thinking’ stage of digital adoption or the later ‘transforming’ stage. Put simply, not enough have reached the ‘profiting’ stage,” explains Michael Wright, Director of Delivery at output.industries. “There is a strong link between using technology to fundamentally change how your business operates and increased productivity and profitability. The need to exploit every efficiency gain, cost-saving and competitive advantage has never been starker. Manufacturers need to be proactively moving into the revolution stage, particularly the one in five still in the ‘doing nothing’ stage.”
Understand the heartbeat of every asset
Fortunately for such companies, output.industries has a solution that is already helping manufacturers leapfrog from doing relatively little with digital to using it to transform their operation. Busroot is a performance monitoring and analysis platform that connects existing assets to the cloud to create an accurate, real-time overview of factory performance. Through pre-built, user-friendly visualisation and workflows, production managers can minimise downtime, maximise throughput and easily manage incidents on any device.
“Overall equipment effectiveness, OEE, is the accepted standard for measuring productivity and a crucial element of most continuous improvement strategies. All too often, however, OEE is calculated using guesswork, averages and outdated figures,” explains Tom Baker, Technical Director at output.industries. “Fundamentally, what OEE lacks is detail. Most manufacturers have an OEE score of between 60% and 80%. The missing 40% to 20% is exactly that, missing. It gets lost in the ether because an almost universal challenge across industry is being able to assign lost performance to a reason.”
Busroot solves that challenge through its ability to accurately account for every minute of downtime in a factory. At any given time, managers can see whether a machine is producing, and if it isn’t, why not. It could be a no-stock issue, mechanical fault, electrical problem, operator error or scheduling mix-up.
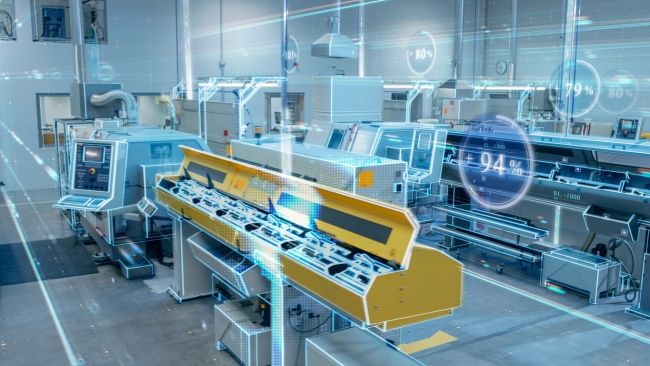
output.industries has built an intuitive, user-friendly solution that enables SMEs to take the crucial first step of using digital technologies to increase productivity / Picture: Getty/iStock
Shine the light on productivity improvements in real-time
Two OEE metrics unique to Busroot are peak average cycle time and peak weekly OEE.
Cycle time is how long it takes to produce a part or complete a process and is a crucial element of production scheduling. Peak weekly OEE is the best a machine has performed over a single week. The large number of potential variables makes calculating these figures a laborious, time-consuming task with a large margin for error.
“With peak average cycle time, we analyse all past and present data for a given machine to identify the fastest it ever made 10 of a specific product in a row. That figure is the maximum performance of that machine for that product,” Tom explains. Knowing that, and being able to automatically feed it into your production targets and digital KPI displays on the shopfloor, gives an optimised performance goal for that shift. Additionally, if you switch over to another SKU or a machine is down for maintenance, that production target dynamically changes in real-time.” Multiplying peak average cycle time and peak weekly OEE gives you a peak production target, an ambitious but eminently achievable goal, says Tom.
“It’s ambitious because you’re multiplying your peak performance and your peak OEE but we have seen a machine run at this speed and deliver this level of OEE. The evidence is there. Fundamentally, this is about giving managers confidence through truth,” concludes Michael. “All production output varies and, to a certain degree, that variance is just accepted. We don’t. Production varies for a reason; it’s not varying randomly. Busroot enables you to identify what those reasons are and work to swiftly address them. The result is less downtime, optimised factory performance and increased throughput using a system built specifically to address the needs of SMEs.”