2 minute read • published in partnership with HVM Catapult
Insight: Augmented reality – a game changer for manufacturing
Recent developments in virtual reality (VR) and augmented reality (AR) have transformed their use across various industries and applications. Danny McMahon, Digital Manufacturing Team Lead at the Advanced Forming Research Centre (AFRC), part of the High Value Manufacturing Catapult, explores why it’s a gamer changer for manufacturing.
As they enter the consumer world, many sectors are using VR and AR to improve customer experience. It’s no different for manufacturing and engineering, with the technology revolutionising the way we manufacture, measure, repair, innovate and collaborate.
Increasingly, manufacturers operate dedicated VR caves where engineers wear headsets and engage with virtual environments. These immersive headsets completely obscure the user’s vision and so for that reason the technology is rarely used on a busy factory floor.
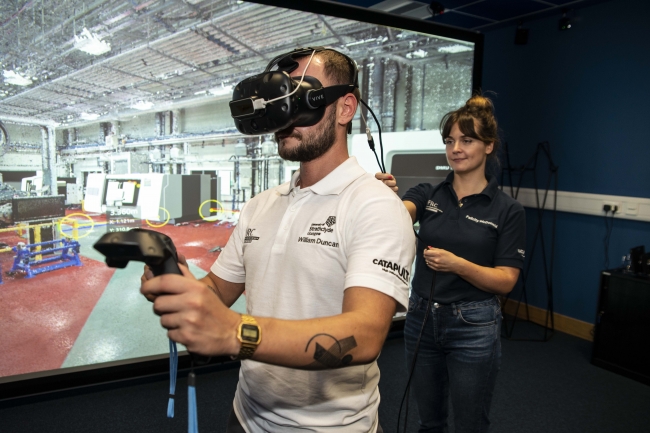
VR and AR can be incorporated into projects to achieve numerous outcomes, with endless opportunities to improve manufacturing and engineering processes / Picture: HVM Catapult
Taking the danger out of work with VR
VR allows in-depth design reviews on a highly accurate scale across numerous locations. It also plays a vital role in training, taking the dangerous situations out of real-world hazardous environments by allowing engineers to first practice the job in a virtual space.
A project at the AFRC looked at the task of transferring ammonia gas from a tanker into a storage tank using VR. Any spillage in real life would result in suffocation, so first allowing trainees to practice the procedure in the virtual world was vital.
AR, meanwhile, doesn’t require a safe space, as it retains and augments the user’s real-world location with virtual holograms. This provides more context than VR, delivering intelligent data that can be used across a variety of applications and industries.
Fixing equipment remotely using AR
One huge impact of AR is enabling experts to fix equipment remotely, feeding instructions to technicians, saving travel costs while also reducing repair time from days to hours.
Like VR, AR will also transform staff training. Rather than instructions fed to employees with complicated descriptions and rough drawings, AR technology reviews what the employee is looking at and shows them how to complete the next step, providing instructions in real time.
Current AFRC project, The Augmented Worker, uses AR to provide real time access to individualised data, analytics and instructions during the construction and operational stages on a building site or shop floor.
This removes requirements for engineers to translate, compensate and visualise 2D drawings into 3D, which is a skill that is difficult to teach and a hurdle that many prospective engineers struggle to overcome.
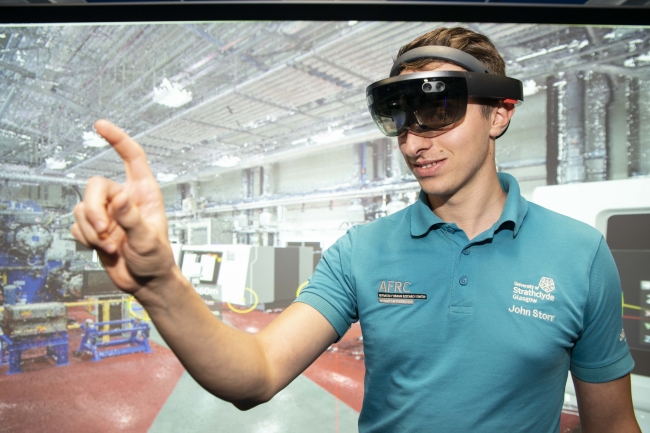
One huge impact of AR is enabling experts to fix equipment remotely, feeding instructions to technicians, saving travel costs while also reducing repair time from days to hours / Picture: HVM Catapult
The future of AR and VR in manufacturing
5G rollout across the UK will impact AR usage on-site, but VR will continue to be used within safe spaces. As we go mobile with the technology, anything that can transfer data quicker will enable application in any 5G location. As we develop VR and AR, we can incorporate them into projects to achieve numerous outcomes, with endless opportunities to improve manufacturing and engineering processes.