4 minute read • published in partnership with SCCG
Insight: Creating a fit for purpose logistics network strategy
In the second of a series of articles, The Supply Chain Consulting Group looks at developing a sustainable logistics network strategy and why if it’s no longer fit-for-purpose, it’s time for a refit.
The pre-requisite for a successful logistics network strategy is a clearly articulated business strategy. You need to have answers to these questions:
• what products are we offering?
• what is our pricing strategy?
• how are we going to sell these products?
• what level of service do our customers expect?
Rapid changes to the B2B and B2C marketplace are creating major pressure on logistics networks. Customer demand is driving the disruption. Distribution and transport solutions that worked in the past decade are no longer fit-for-purpose. More agile solutions are needed to support the trend towards more choice, smaller order sizes and shorter lead times.
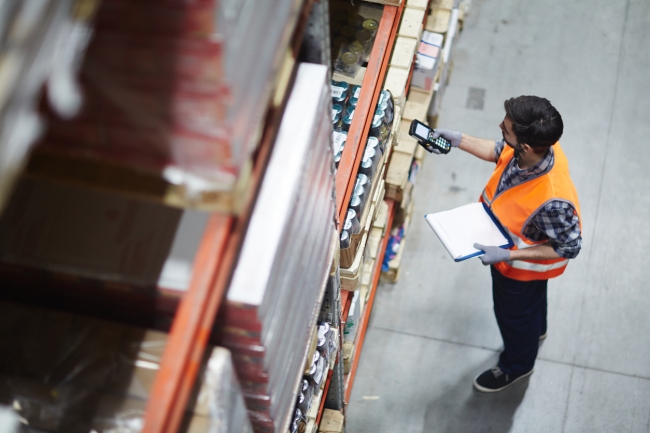
An efficient and sustainable logistics network responds better and more quickly to market disruption / Picture: Getty/iStock
Companies need expertise and resources to continually redesign their networks. The objective stays the same: reduce costs, minimise risk and satisfy customers. An “optimal” distribution network is one that fulfils these goals. Modelling software tools are often used to create scenarios that inform the plan towards that optimised solution. But we need to do some preparation.
1 – Data collection
The first step is to document the current network and all related activities. This involves interrogating all existing systems and manual processes and extracting the complete data for a defined period. In a typical distribution facility, at a minimum it would include:
• Current distribution costs (both fixed and operational) for each location. Dimensions and layout of facilities, systems in use, human resources, moveable equipment and other assets.
• Current transport costs. Number and type of current fleet assets and/or 3PL or 4PL contracts, data on modes of transport, mileage history and any limiting criteria.
• Detailed inventory data per facility including product master data, stock holdings and reorder levels, shipment sizes
• Customer information. Storage facilities, delivery locations, demand patterns per product line, seasonal peaks
For each of these areas, a detailed cost analysis must be calculated. For example, warehouse cost calculations must be granular, down to the task/resource level. Added to this will be any information about known changes to systems or processes and predictions about future projected growth if any.
2 – Data analysis and validation
All data that may be relevant to any potential solution must be included in the analysis. The data collected must be sorted, cleansed and classified before it can be converted into information to use as a basis for modelling. Data cleansing involves ensuring that the data has no duplicates and it is organized into a logical structure. Complete and accurate data is critical: the phrase “garbage in = garbage out” applies here. Quality data will save valuable time and reduce uncertainty in the next step: modelling.
3 – The modelling
On completion of the process of documenting the current network, we want to develop various possible solutions. The modelling of scenarios aims to reach a workable solution that satisfies business goals bearing in mind financial and physical limitations. The aim is to achieve the “sweet spot”, the optimal balance of locations and resources. Trade-offs must be made; there will be capacity constraints, limited asset availability and customer considerations.
There are a few ways to do modelling using software solutions, either bespoke or using proprietary or black box software. A bespoke or semi-bespoke tool allows for specific emphasis on unique or complex aspects of the business which may not be catered for in off-the-shelf or black-box software. Transparency and insight into the calculations and methods used are important when modelling alternative network scenarios. For example, the transport model should reflect all the specific dynamics of the operation, both simple or complex, and must interact with routing and scheduling logic and limitations.
Typical questions to be answered for any distribution facility include:
• What SKUs are to be stored at which facility?
• Will all sites hold inventory, or will some be used only for cross-docking?
• What is the maximum number of achievable drops per truckload?
• What impact would each scenario have on current suppliers?
If the objectives are clear, mathematical optimisation techniques can be used to find the “best” solution. If the goal is cost reduction, the chosen solution will be different from one that is focused on customer satisfaction and speed of delivery. We need to find the lowest annual overall cost of the distribution network that satisfies customer service demands. Required changes to systems or processes, as identified in the data collection phase, must be factored into all possible scenarios.
4 – Take action
To achieve the “best” result:
1 – Define logistics requirements based on business goals
2 – Establish current and estimate future customer demand
3 – Document distribution, transportation, and servicing data
4 – Analyse and validate the data and document it
5 – Model various logistics network options
6 – Consider alternative solutions and select the “optimal” one for present conditions
An efficient network responds better and more quickly to market disruption. Revisit your logistics strategy when it is evident that is not fully functional: i.e. you want to reduce costs, mitigate risk or improve customer service – it is a circular process.