5 minute read • published in partnership with output.industries
Insight: Increase your production by 10% without additional machines or workers
With input costs soaring, manufacturers are laser-focused on reducing production losses, increasing throughput and resolving issues faster. output.industries has built an intuitive solution that empowers SMEs to do exactly this and much more besides.
In the face of extreme supplier shortages, record inflation and fluctuating demand, operational efficiency is vital for survival and growth. The companies most likely to succeed are those who adapt their processes, digitalise their systems and embrace new technologies.
Manufacturers recognise this fact, as reflected by the one in two* planning to increase their investments in digital technologies and data analytics over the next 12 months. Yet, that figure slumps to just one in four when it comes to small and medium-sized enterprises (SMEs).
That’s worrying, not least because SMEs form the backbone of the manufacturing sector, representing around 96% of industrial businesses. Small manufacturers frequently cite a lack of skills, finance and vision as the primary barriers to increasing their digital adoption. But increasingly, these aren’t as big an obstacle as perceived.
Research has shown that manufacturers who invest between £100,000 and £500,000 in digital technologies** have seen productivity gains by as much as 50%. Whereas a sizeable number of those who invested more than £1m saw productivity decline by between 10% and 25%. When it comes to digital technologies, it appears that small and strategic trump enterprise-wide and disruptive.
Additionally, leading-edge digital tools don’t require companies to have in-house data engineering teams or expansive data lakes. “We can provide an enormous amount of value with relatively little factory data, and we can start to deliver that value from day one,” explains Tom Baker, Technical Director at output industries.
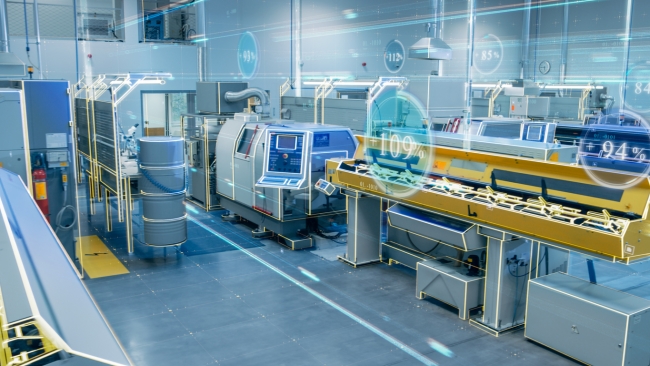
Manufacturers most likely to succeed are those who adapt their processes, digitalise their systems and embrace new technologies / Picture: Getty/iStock
Proactively driving manufacturing performance
According to Tom, this value typically presents itself as 20% less unplanned maintenance and a 50% reduction in stoppage time. A tantalising prospect at the best of times but especially so given the soaring cost of downtime.
The cost of unplanned downtime is now at least 50% more than pre-Covid*** because of spiralling inflation and production lines running at higher capacity. It is also taking factories longer to recover. The average plant loses two full shifts of production (24 hours) a month to unplanned downtime.
“An almost universal challenge across industry is being able to accurately assign lost performance to a reason,” explains Tom. “You know your factory can produce 1,000 products a day but it only makes 800. Where are the missing 200? Few manufacturers have a full picture of where they are losing performance and productivity.”
That’s where output industries’ Busroot comes in and its ability to account for every minute of downtime in a factory. At any given time, you will be able to see whether a machine is producing or not and if it’s not, the reason why. It could be a no-stock issue, mechanical fault, electrical problem, operator error or scheduling mix-up.
“Busroot is able to do that because once a problem is resolved, we follow up with the person who acknowledged it and make sure they give a reason why,” Tom continues. “In so many cases that information is just lost in the wind, it never gets recorded. Machine goes down, someone jumps in, fixes it and then gets on with their day.”
By streamlining and making that communication process proactive, Busroot shines a light on productivity improvements in real-time that were previously hidden. Knowing that 75% of production loss is due to not having enough stock on hand enables factory managers to fix the root cause. As Tom describes it, Busroot “closes the loop” in terms of the downtime process.
“If your factory has 10 machines, we can effectively add an 11th ‘virtual machine’ through performance gains and optimising how issues are resolved. That’s an immediate 10% boost to your productivity without the need to go out and acquire additional machines or workers.”
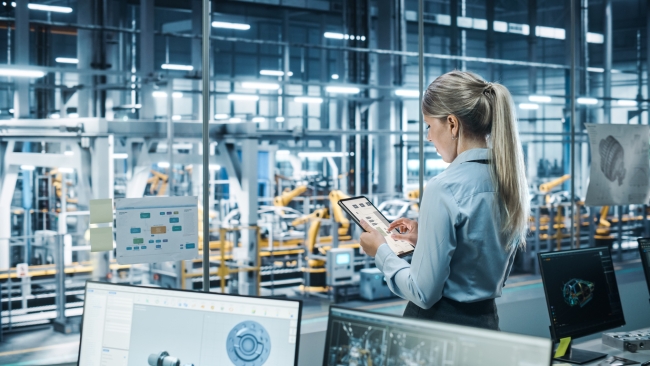
Busroot shines a light on productivity improvements in real-time that were previously hidden / Picture: Getty/iStock
Understand the heartbeat of every asset
So, how does it work? Busroot is a performance monitoring and analysis platform that connects existing assets to the cloud to create an accurate and real-time overview of factory performance.
Through pre-built, easy-to-understand visualisations and workflows, managers can minimise downtime, maximise throughput and easily manage incidents on any device.
Designed and built specifically to address the needs of SME manufacturers, Busroot puts OEM-level capabilities in the hands of much smaller organisations. Furthermore, the development team understands deeply what’s needed to optimise a factory floor.
“Most SMEs have well-established brownfield sites,” explains Tom, the former Head of Digital for one of the world’s largest tyre manufacturers. “They don’t want to have to rip out and replace their existing assets and re-engineer every process. Busroot offers the opportunity to retrofit machinery and receive the same benefits if not more as the latest-generation PLC without the high cost and associated disruption.”
A key capability of Busroot is its speed of communication, getting the right message to the right person at the right time and getting machines back up and running as swiftly as possible. Think of Busroot as a ‘digital supervisor’, someone who is watching every one of your machines like a hawk and as soon as an event occurs, the appropriate person knows about it and can work to resolve it.
One of the most exciting things about output industries is that the journey doesn’t end there. The company is continuously broadening out the solution and adding new capabilities, often in direct response to customer feedback.
Currently, the team is developing a recognition engine so that once an issue with an asset is resolved, the next time it occurs the platform can work to resolve it before the issue has even been acknowledged.
“If the same machine goes down consistently for similar reasons, say a stock issue, Busroot will very soon be able to identify a pattern and as soon as that machine goes down, it will automatically contact the planner for you. Issue, diagnosis and resolution with minimal time between steps. That’s where the value of Busroot truly starts to transform manufacturing.”
To find out more and transform your factory, visit: output.industries