4 minute read • published in partnership with Cimlogic
Insight: Maintenance – an inside view on increasing productivity and reducing downtime
As a Business Analyst, Nik Tankard from Cimlogic, is frequently involved in discussions around business challenges and with the current financial climate, he has seen a recurring theme. Businesses are under extreme pressure to improve efficiency and deliver more with less if they are to recover from the financial impact of the COVID-19 pandemic on virtually every industry. Here he shares his thoughts on how manufacturers can increase productivity and reduce downtime.
Recently, I have been discussing the topic of maintenance with several key clients and this is an area I feel can really benefit companies when implemented correctly. Obviously, regular maintenance of equipment is an important and necessary activity but it’s not just about ensuring equipment uptime. ‘Maintenance’ covers many activities, including inspection, testing, measurement, replacement, and adjustment, and is carried out in all sectors and workplaces.
Maintenance has a vital role to play in reducing the risk associated with some workplace hazards and providing safer and healthier working conditions. Insufficient/inadequate maintenance can unfortunately lead/contribute towards serious (and potentially deadly) accidents or health problems. PUWER (the Provision and Use of Work Equipment Regulations 1998) states that ‘all work equipment be maintained in an efficient state, in efficient order and in good repair’.
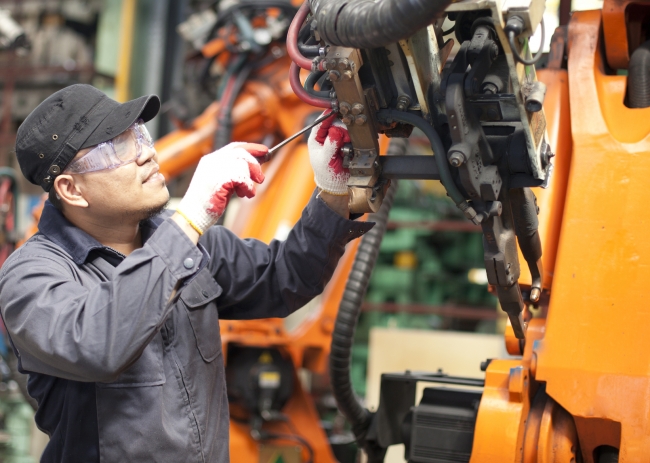
A focused and cost-effective maintenance strategy can increase factory productivity and reduce downtime / Picture: Getty/iStock
But is it cost effective, and are there benefits to exceeding the bare minimum regulation compliance?
Preventive maintenance is any regular maintenance performed on an active piece of equipment. By following a consistent maintenance strategy, a company can catch potential problems with its machinery before they occur, preventing equipment failure. But with so many other priorities currently, is now a good time to invest? Well, from my experience, implementing strategic maintenance and guaranteeing equipment availability will generally boost confidence and enhance corporate reputation. Preventive maintenance can be costly to implement, However, its benefits outweigh the costs … In the long run, preventive maintenance extends the working life of equipment and reduces maintenance costs, making it a valuable investment.
Improving OEE within a production line by just 1% through implementing preventive maintenance can see significant financial returns when factoring in:
• Equipment cost
• Repair Cost
• Depreciation
• Energy Usage
• Labour
• Increased productivity
• Increased Yield
How do we know whether maintenance is effective?
Generally, there are a few KPI’s which are recognised across industry, but it starts with benchmarking. No matter how effective you feel your systems are, there is always scope for improvement. By benchmarking KPIs such as MTBF (Mean Time Between Failure) and MTTR (Mean Time to Respond) you can ask yourselves 3 questions.
• Where are we now?
• Where do we want to be?
• What do we need to do to get there?
By monitoring the benchmark KPIs when implementing strategic maintenance, results can be very quickly visualised and quantified.
What can we do better?
Digitalisation and real time data are rapidly becoming more vital in any operation. The use of data within maintenance is therefore becoming ever more common. With remote digital connectivity, maintenance can become significantly more efficient and adaptable to suit the continuously evolving landscape of modern manufacturing:
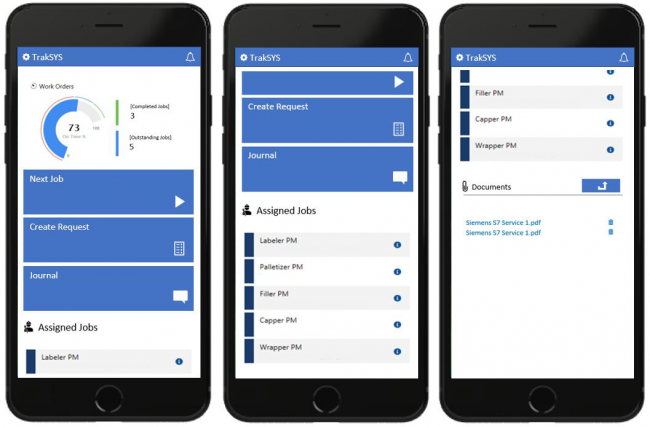
Digitalisation and real time data are rapidly becoming more vital in any operation / Graphic: Cimlogic
• Notifications can be created and responded to quicker
• Troubleshooting can become easier through mobile access to equipment documentation and history
• The cost of maintenance can be visualised and forecasted.
• Planning and scheduling become optimised across departments.
• Standardised ways of working can be very easily implemented
So, where is the best space to implement Maintenance?
It’s no secret, there is a range of systems capable of implementing maintenance, from standalone software applications to Enterprise level systems (ERP) and they all have functions and features that can support your maintenance journey. ERP systems definitely have the advantage when it comes to parts procurement and CMMS (computerised maintenance management systems) are good for asset documentation and logging historical data.
But why settle for one space or system? IIoT and the Industry 4.0 revolution now allow us to make the best of both worlds. Thanks to the connectivity capabilities within MES (Manufacturing Execution Systems), maintenance can very easily become “predictive”.
Most ERP and CMMS systems can implement preventive maintenance based on fixed time durations, but with the addition of MES, maintenance can be derived by actual production. Maintenance activities can be coordinated by how much the equipment has produced, which in turn reduces costs.
The machine learning capabilities of modern MES systems make it so easy to implement predictive maintenance through monitoring machine signals to determine when systems are at risk, making it a crucial part of any optimum maintenance strategy.
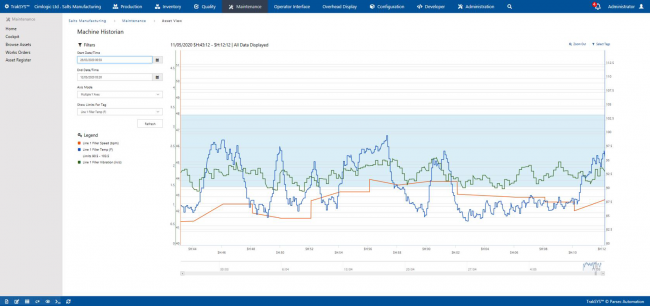
Thanks to the connectivity capabilities within MES (Manufacturing Execution Systems), maintenance can very easily become predictive / Graphic: Cimlogic
With companies facing increasing pressure to ‘make more with less’ as we go into 2021, I remain convinced that maintenance management is an area where tangible business efficiency improvements can be made.