4 minute read • published in partnership with Cimlogic
Insight: Making sustainable manufacturing work for you
Sustainable manufacturing means many different things to many people. As companies reinvent themselves they look upon ways of showcasing their bold moves in taking accountability for the environmental impact of their offerings. A core component of this industrial paradigm shift is the increasing use of digital technologies – the bringing together of automation, the Internet of Things (IoT), artificial intelligence, digital twins, business processes, big data and cloud computing. Cimlogic explores the steps manufacturers in food & beverage and pharmaceuticals & life sciences can take to embrace sustainability.
These industries are growing fast and are heavily regulated. Both of these industries also produce a large number of emissions. These are two industries that we utilise on a daily basis and their moves towards sustainability are ever visible. Looking at things from a different perspective, however, both of these industries are already well into their digitalisation journey. Just think of track and trace technologies to help identify the components that make up each and every batch of corn flakes or Covid-19 vaccine.
Outside of raw material processing and production, there is packaging and distribution to take into account. The subject of using sustainable and recyclable materials in product packaging, whilst important, is not the primary focus of this article but is still a major driving force as large multinationals continue to shoulder increasing corporate responsibility. Besides, it makes good business sense. A recent study from Nielsen showed that 66% of consumers are willing to spend more money on brands that are promoting eco-friendly and sustainable practices.
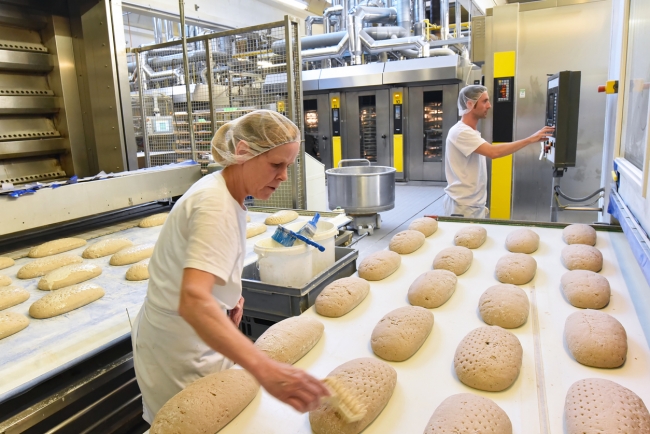
Optimisation of water, air, gas, electricity and steam consumption can lead to typical annual savings of between 5-15% / Picture: Getty/iStock
As we have already established, factory automation is key for minimising food waste whilst keeping production running as quickly and efficiently as possible. More eco-friendly packaging, using recyclable, compostable, or biodegradable materials are easily visible to the consumer and hence boost brand reputation.
This brings us to the energy used inside the factory. Manufacturers need to meet emissions targets and still fulfil consumer demands. In the previous article, we touched upon some of the well-established technologies within factory automation used today: the use of variable speed drives and motors and using alternative energy systems where possible.
The energy used is broken down into 5 key components – Water, Air, Gas, Electricity, and Steam – WAGES. Optimisation of any or all of the WAGES components can lead to typical annual savings of between 5-15% the equivalent of millions of pounds for large multinational corporations. So, how do we do this? How do we successfully monitor and target our energy usage?
The first step in gaining control of your energy costs is to measure the total amount of energy that flows through your system. Let’s take a look at each component.
WATER – Water plays a critical role in just about every industry, with chilled water, process water, cleaning water and effluent water flowing freely in a production plant. We need to be able to measure water flow and pressure to determine if and where water losses are occurring. Secondly, heating or chilling water uses vast amounts of energy, but is the process efficient?
AIR – Compressed air is used throughout manufacturing operations and is typically designed to handle high demand events. However, these are for short durations, leaving the system at over capacity most of the time. Let’s not forget leaks, one of the greatest sources of energy loss in compressed air systems.
GAS – Whether for process or as fuel gas consumption has quite an impact on costs. Any processes that require high gas usage should be coordinated to meet low demand times when purchase costs are lower.
ELECTRICITY – Similar to gas usage, electricity usage is about balancing supply and demand. Electrical power quality issues such as harmonics should be addressed to prolong equipment life.
STEAM – Steam is an essential service in many parts of the food and life science industry, primarily as a source of heat for product processing or equipment decontamination. Heating water to produce steam is expensive, and any leaks or damage to equipment needs to be minimised.
Each of the WAGES components needs to be successfully measured, monitored and analysed successfully before making any decisions on making changes. There is a plentiful supply of off the shelf smart sensing and metering products available. Integration of data from these devices is straightforward and easy to set up thanks to advances in network communications and secure data transmission.
The key is the ability to capture real-time data so that corrective actions can be decisive and lead to cost savings. Cimlogic has many years of experience in setting up energy monitoring systems, from installing smart devices and other enabling technologies for data collection to software platforms for providing an easy display of data, allowing for complex decisions to be made easily.