5 minute read • published in partnership with Cimlogic
Insight: Managing capacity to increase output, reduce costs, and improve customer satisfaction
Capacity constraints will prevent manufacturers from achieving more output. These might include minor bottlenecks but also lack of labour, unexpected demand fluctuations, raw materials supply etc. How well is your manufacturing plant prepared to cope with unexpected (or expected) constraints? Cimlogic shares its insight on where manufacturers should start and how to reduce capacity constraints.
Demand is neither predictable nor stable for most manufacturers, and adding capacity takes time and money. Competitors vie for market share, and manufacturers are constantly seeking to reduce costs whilst meeting the challenges of shorter product life cycles.
There is no simple formula to work out how much capacity you need, currently or in the longer term, but much can be done to manage constraints to meet both demand and strategic business needs. Determining the correct capacity level for a manufacturing plant at any given time to satisfy customer demand needs experienced assessment and evaluation.
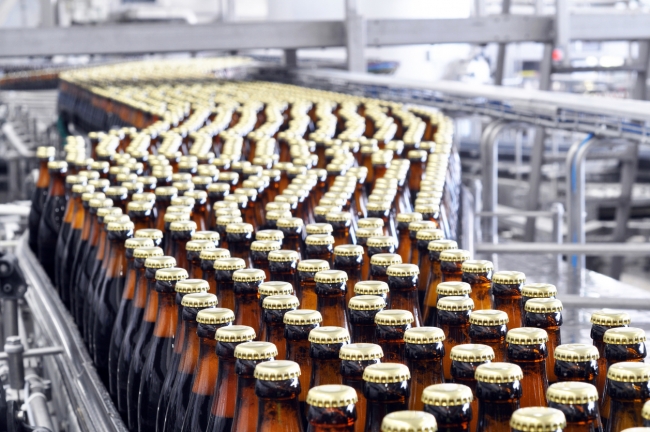
Manufacturers should develop a capacity management plan to help increase output and reduce costs / Picture: Getty/iStock
So, where should you start? When developing a capacity management plan, manufacturers need to understand the following:
How variable is customer demand? If demand were consistent, operations would be straightforward. However, this is not a typical scenario. Seasonal fluctuations are common, but what about unforeseen political and environmental challenges? Preparations for Brexit have been well underway for some time, but no one could have foreseen the implications of COVID19 on manufacturing demand (both positive and negative). With variable demand, manufacturers may need more capacity and/or inventory to cover demand spikes.
What is the ideal level of stock inventory? Manufacturers need to understand inventory holding costs and the impact of storage on product quality (many foodstuffs have a finite shelf life, for example). What are the customer expectations re delivery timescales? Are competitors able to supply from inventory in times of urgent demand?
What is the cost of increased capacity? For manufacturers to evaluate the value of increased capacity, it is crucial to understand the costs of obtaining (and maintaining) this additional capacity versus the business benefits (the ability to meet surges in demand). Can additional capacity be scaled back once demand has peaked?
What are customer expectations for your product or service? Lead times (and expectations) vary greatly by industry. Is a 24-hr turnaround vital to avoid losing business to a competitor, or are longer lead times acceptable for your product? Manufacturers need to be aware of how long a customer expects to wait between placing the order and receiving the product. Customer satisfaction can be very reliant on delivery timescales being met or exceeded.
How long does it take to add new capacity? If additional skilled staff or new equipment are required, careful planning will be needed in advance to manage increases in capacity. Alternatively, overtime or temporary staff, or reallocation of equipment may be used to manage short-term supply challenges.
Where are the typical internal bottlenecks which affect capacity?
Aside from the above external considerations which affect demand, capacity issues within manufacturing plants typically fall into three areas:
1 – Reliability of machinery
Downtime can reduce the effective capacity of the entire production line. How do you measure downtime? Is your maintenance system fit for purpose to maximise uptime and productivity? Are you confident your production line is running as efficiently as possible?
2 – Physical space
Do you have enough space in the factory to add a production line if needed? What alternatives are there? Are social distancing rules affecting your production targets?
3 – Labour
Many manufacturers blame reduced productivity on a lack of skills in the workforce. How are you addressing this? Skills shortages are increasingly common and many companies are seeking to automate processes to allow staff to be reallocated (with appropriate training) into more valuable roles.
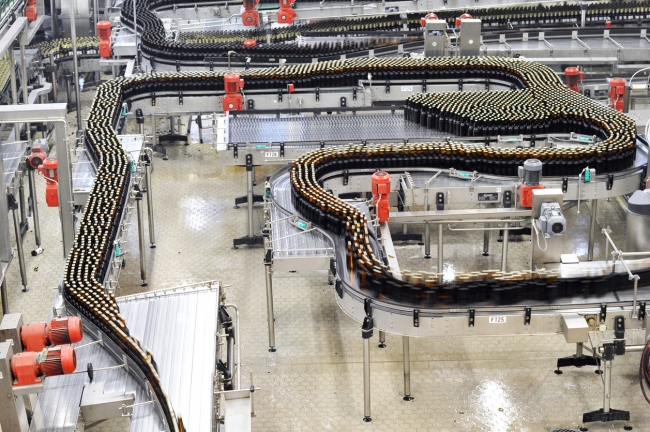
Manufacturers who can address capacity management will be able to maximise output, overcome constraints whilst improving the integration of other key processes across the supply chain / Picture: Getty/iStock
Do you know where your capacity constraints are?
Many companies routinely hit capacity constraints and immediately consider adding overtime for existing workers, hiring workers for a new shift, or buying a new line. But is there any guarantee this will solve the capacity challenge?
Before you invest in new machinery or additional labour, can you be certain this will solve your capacity challenge? Research suggests 8 out of 10 organisations are initially mistaken as to where their bottleneck is*. Take time to understand the true cause(s) of reduced efficiency/capacity and you might avoid unnecessary costs:
• Look beyond ERP (eg is your Quality system fit for purpose?)
• The most expensive machine is not necessarily the bottleneck (don’t jump to conclusions about where you think the bottleneck should be!)
• Quality control/quality documentation cause significant workload issues and are often a constraint.
• Understand significant changes in the recent past which may impact capacity:
– New quality legislation
– Cost cutting initiatives.
– New technology/equipment
– Managerial changes/new processes
– Change in raw materials/components
– New competition
Are you trying to meet today’s productivity targets with yesterday’s resources/processes?
Don’t forget to TEST the bottleneck. Once the bottleneck has been addressed, how much does productivity increase? Be wary of simply moving the bottleneck elsewhere!
Capacity planning – next steps
Global disruption, both political and environmental, threatens supply chains worldwide and manufacturers need practical, flexible capacity planning strategies to adapt to constantly moving goalposts.
Many manufacturers use analytical solutions to identify (and address) root causes of capacity constraints across the whole supply chain. Indeed, hiring additional labour, outsourcing processes and/or investing in additional capacity should not be embarked upon without a full (and accurate) picture of the capacity challenges faced by manufacturers.
For manufacturers with multiple production sites and product lines, (and options to move manufacturing between sites/products), the permutations for capacity planning can be overwhelming. Companies might revert to traditional MES/ERP tools to achieve a workable solution to meet demand.
Ultimately, though, manufacturers who can answer the following questions will be able to maximise output, overcome capacity constraints whilst improving the integration of other key processes across the enterprise supply chain:
• What is my cost per unit (labour included) and how long does it take to make a product?
• How do I get more output from the same amount of labour?
• I want to expand our products but don’t know if we have the capacity to do it?
• Are we investing in the best areas of capacity improvement?
• What is the cost of losing a customer due to poor lead-times and unfulfilled orders?
• How can I collect the right data and insight to make accurate supply and demand forecasting decisions?
• I want better visibility of processes such as inventory planning, production scheduling, sourcing and capacity planning to enable improved integration across the supply chain, but don’t know how?
Cimlogic works with manufacturers to answer the above questions, enabling clients to manage capacity constraints to improve customer relations, increase output and reduce costs.